Imagine having a crystal ball that lets you know when your equipment will fail before it even happens. It sounds like science fiction. Well, not anymore! With machine monitoring in manufacturing, you can predict equipment failures and prevent costly downtime. In this blog post, we’ll dive deep into how the manufacturing industry is transforming for the better with machine monitoring software. So, learn about this innovative technology that could revolutionize your business!
What is Machine Monitoring?
Manufacturing plants must produce high-quality products at a lower cost and shorter time frame. To meet these goals, manufacturers rely on machines to execute various tasks in the production process. However, assets are subject to wear and tear and can break down unexpectedly, leading to production delays and increased costs.
To avoid these problems, manufacturers use machine monitoring systems to track the performance of their machines. These systems collect data on machine speed, temperature, and vibration. This data is then analyzed to specify trends and potential issues. It helps manufacturers optimize their production process by reducing downtime and increasing efficiency. They also allow manufacturers to identify and fix problems before they cause significant disruptions. Some companies also use this to track utilization and calculate equipment cost per unit produced.
What is Machine Monitoring in Manufacturing?
The industrial revolution saw the introduction of many new technologies that changed how we manufacture products. One of these technologies is machine monitoring software. It is considered the process of tracking and recording information about machines in a manufacturing setting. This information includes the machine’s operating status, performance data, and maintenance records.
This software enables the improvement of manufacturing efficiency and quality control. By tracking information about machines, manufacturers can identify areas where machines are not operating correctly or where there could be improvement. Later this information is used to change the manufacturing process to improve efficiency and quality. Additionally, a machine monitoring platform can generate a machine’s performance history. This history can later help diagnose problems with assets or predict future issues.
How Does Machine Monitoring Work?
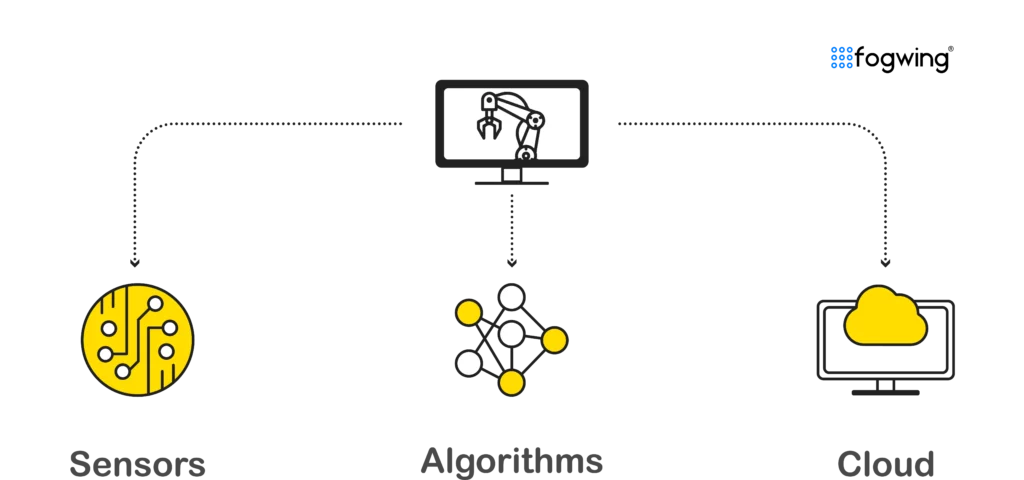
In manufacturing, the process of using sensors and other technology to track the performance of machines on the factory floor is known as a machine monitoring solution. The data gathered can enable organizations to improve efficiency and quality control and identify potential problems before they cause downtime.
There are a variety of ways to conduct machine monitoring, including using the following:
- Sensors that track things like vibration, sound, temperature, and power usage
- Machine learning algorithms that analyze data to identify patterns
- Cloud-based software that enables real-time monitoring and reporting
Generally, sensors connect to machines via wires or wireless networks, and data collected by the sensors is transmitted to a central computer for analysis. Machine learning algorithms help to detect patterns in this data that may indicate problems with a machine, such as unusual vibrations that could indicate an imbalance or a change in the sound profile that shows wear on bearings. Cloud-based software can provide real-time monitoring and alerts to address asset issues before they cause downtime.
Benefits of the Machine Monitoring System
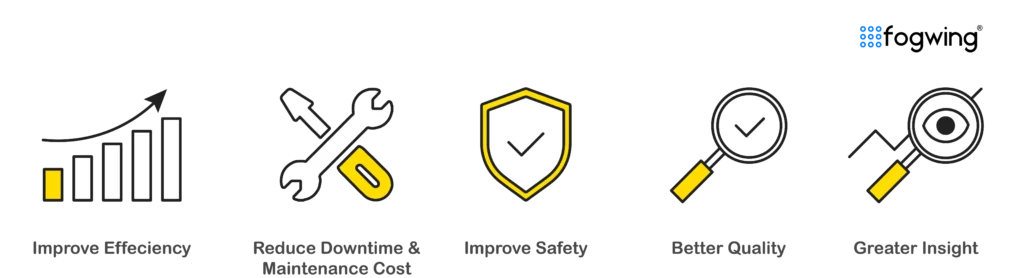
An equipment monitoring system can provide many benefits for a manufacturing business, including :
Improved Efficiency and Productivity:
By tracking the performance of individual machines, a manufacturing business can identify any bottlenecks or inefficiencies in its production process, which enables the organizations to make the essential modifications to enhance the overall efficiency of the operation.
Reduced Downtime and Maintenance Costs:
By identifying potential problems before they occur, machine monitoring can help to reduce downtime and associated maintenance costs.
Improved Safety:
By monitoring the status of machines and equipment, machine monitoring Software can help to identify potential safety hazards before they occur.
Better Quality Control:
By constantly monitoring your machines, you can more easily identify any issues with the quality of your products and take steps to correct them.
Greater Insight into your Business:
A machine monitoring system can provide valuable data and insights into how your business runs, which can help you make good decisions about where to concentrate your resources.
Machine monitoring vs Condition monitoring
The industrial revolution saw the introduction of machines into the manufacturing process, and with that came the need to monitor and maintain those machines. Over time, two different approaches to asset monitoring have emerged: machine monitoring and condition monitoring.
What is the difference between these two methods?
The machine monitoring solution is the more traditional approach and involves manually inspecting machines regularly to look for signs of wear or damage. It can be time-consuming and expensive, mainly if many devices are involved.
Condition monitoring is a newer approach that uses technology to monitor the condition of machines automatically. The data helps manufacturers identify potential problems early on before they cause downtime. Condition monitoring can be used to develop predictive maintenance models that can schedule maintenance activities based on the real-time conditions of machines.
IoT for Machine Monitoring
The Internet of Things (IoT) revolutionizes the manufacturing industry by providing real-time data and insights into machine operations. With IoT-enabled sensors, manufacturers can monitor their machines remotely and gain visibility into critical performance metrics such as temperature, vibration, energy consumption, and more.
By leveraging IoT for equipment monitoring, manufacturers can predict when a machine will fail before it does. This solution allows them to schedule maintenance proactively instead of waiting for a breakdown, which can lead to costly downtime.
IoT also enables real-time predictive maintenance through advanced analytics and machine learning algorithms that continuously analyze machine performance data. By identifying patterns and trends over time, these algorithms can identify potential issues before they become major problems.
Moreover, with IoT- enabled machine monitoring systems in place, manufacturers can access actionable insights that can help them optimize production processes and increase efficiency across their entire operation. These insights include information on how specific machines operate at different times throughout the day or week and factors affecting overall productivity, such as weather or other external factors.
IoT-based industrial machine monitoring systems represent a significant opportunity for manufacturers seeking to improve their operations by gaining greater visibility into how their equipment is performing on an ongoing basis.
IT / OT Integration for Equipment Monitoring System
IT/OT integration is crucial to equipment monitoring in the manufacturing industry. The convergence of information technology (IT) and operational technology (OT) is essential to ensure effective communication between various systems, devices, applications, and databases.
Integrating IT/OT enables better industrial – process data collection, analysis, and decision-making capabilities. It allows manufacturers to monitor their machines effectively by providing real-time insights into performance metrics such as uptime, downtime, production rates, energy consumption levels, etc.
Furthermore, IT/OT integration streamlines workflow processes from design to production by automating tasks previously performed manually. This solution reduces errors while increasing overall efficiency in manufacturing operations.
By leveraging IoT- enabled platforms for machine monitoring with integrated IT/OT infrastructure, manufacturers can lower maintenance costs by identifying potential faults before they occur. They can also optimize production schedules while minimizing unplanned downtime due to unforeseen equipment failures or breakdowns.
Incorporating IT/OT Integration with machine monitoring platforms provides tremendous benefits for manufacturers seeking operational efficiencies through automation and real-time analytics across their factory floor.
How to Choose a Machine Monitoring Platform ?
There are many factors to consider when choosing a monitoring solution for your machines in the manufacturing business. The most important factor is compatibility with your existing machinery and software. Other factors include price, features, support, and ease of use.
Compatibility is essential because you want a machine monitoring platform that will work with the equipment you already have in place. Otherwise, you’ll have to purchase new machinery or find a software workaround, which is not ideal.
Price is also an important consideration. You don’t want to overspend on a platform that doesn’t offer enough features or isn’t compatible with your existing setup. However, you also want to ensure machine monitoring quality while saving money.
Features and support are both important considerations as well. Some platforms offer more features than others, so choosing one with the features you need is important. Additionally, good support can be essential if you face any platform problems.
Ease of use is another critical consideration. You want a comfortable machine monitoring platform to set up and use so you can start utilizing it as soon as possible without any headaches.
Once you’ve considered these aspects, you should be able to pick a platform that’s right for your business.
Fogwing for Machine Monitoring Solution
The Fogwing IIoT platform is one of the most efficient and reliable industrial machine monitoring systems. This cloud-based platform offers real-time data analysis, predictive maintenance, and remote machine access.
One of the key features that make Fogwing IIoT Platform stand out is its scalability. It can easily integrate with existing systems in a manufacturing plant, regardless of their size or complexity. Additionally, it has been designed to support multiple protocols such as MQTT, API, and UDP.
The platform also offers customizable dashboards that allow users to visualize critical parameters such as temperature, pressure, or humidity levels from sensors installed on various machines in real-time. This feature enables plant managers to make informed decisions about machine maintenance schedules and avoid unexpected downtime.
Another great advantage of using Fogwing’s IIoT platform is its ability to perform analytics on large datasets generated by different machines over long periods. By leveraging AI algorithms, it identifies trends in data patterns that could indicate potential faults before they occur.
Using an IIoT platform like Fogwing for machine monitoring provides manufacturers with valuable insights into their machinery’s performance while improving efficiency through reduced downtime costs associated with unplanned equipment breakdowns.
How to Get Started with an Industrial Machine Monitoring Software?
If you’re new to machine monitoring systems for industries and looking to get started with them in your manufacturing business, there are a few things you need to know. It is a process of tracking and collecting data on manufacturing equipment performance. The data collected enables manufacturers to improve productivity and efficiency, identify issues early, and make informed decisions about maintenance and repairs.
Select the right software according to your needs to start with an machine monitoring. There are various options on the market, so it’s essential to research and find the solution that best fits your company’s requirements. Once you’ve selected a software solution, you must install it on your machines and configure it according to your preferences.
Once everything runs, you can gather data on the machine’s performance. This data will help you recognize areas where improvements can be made, such as increased speeds or reduced downtime. By making these changes, you can enhance your overall manufacturing process and keep your equipment running at its best.
Conclusion
Machine monitoring in manufacturing provides many advantages to businesses, both large and small. By collecting data on machine efficiency, manufacturers can make informed decisions about preventive maintenance activities, improve safety protocols, and reduce the risks of costly downtime. Additionally, real-time monitoring machines enable proactive corrective action when issues arise. It ensures that all processes are running smoothly with minimal delay or interruption, which leads to higher productivity and profit for the organization.
Fogwing IIoT Platform is an excellent example of a machine monitoring system that enables remote monitoring, predictive maintenance, and data analytics in one comprehensive platform. By leveraging Fogwing’s capabilities, manufacturers can automate their processes further, reduce manual intervention, improve quality control measures, and minimize waste production, among other benefits.
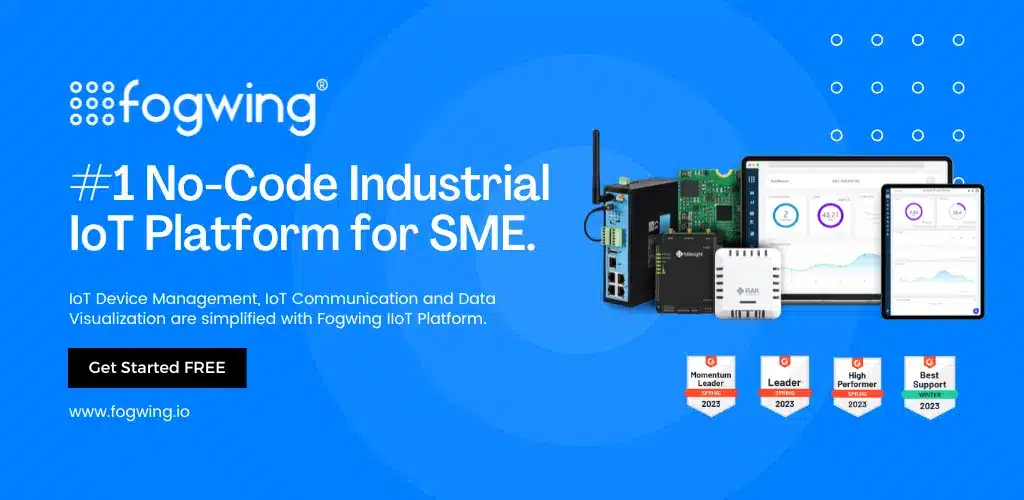