In the ever-evolving landscape of industrial machinery, precision and efficiency are paramount. Ensuring optimal performance and preventing costly downtime has become the holy grail of machine operators and maintenance teams. That’s where the role of machine data collection assumes its rightful place, shining a spotlight on the path to effective and proactive maintenance strategies.
Machine data collection refers to gathering data from machine sensors and other sources to track the performance and condition of the machine. This data can be used to identify trends, diagnose machine conditions or problems with the machine, and plan preventive maintenance. Welcome to a world where machines function and communicate, providing invaluable insights into their condition based monitoring.
What is Condition Based Monitoring?
Condition based monitoring is a proactive approach to maintenance that focuses on monitoring the operational condition of machines and equipment to identify potential issues before they lead to failures. By continuously collecting and analyzing machine data, industries can optimize maintenance schedules, minimize downtime, and reduce costs associated with unexpected breakdowns.
By harnessing the power of machine data collection, industries can optimize performance and increase overall productivity. So, if you’re ready to dive deep into the fascinating realm of intelligent machines and learn how they can revolutionize your business operations, keep reading!
Benefits of Machine Data Collection in Condition Based Monitoring
In condition based monitoring, machine data collection offers many benefits that revolutionize traditional maintenance approaches. With the power of machine data, businesses can enhance predictive maintenance capabilities and optimize machine performance, resulting in significant cost savings and operational efficiency improvements.
Improved Predictive Maintenance
Machine data collection enables early detection of potential machine failures, allowing maintenance teams to take proactive measures before costly breakdowns occur. Maintenance personnel can identify impending issues and initiate timely repairs or replacements by monitoring key performance indicators and analyzing trends, anomalies, and patterns in machine data.
Furthermore, minimizing unscheduled downtime is a crucial advantage of machine data collection. By continuously monitoring machine-generated data, businesses can identify deviations from normal operating conditions, enabling them to schedule maintenance activities during planned downtime, thereby reducing the impact on production schedules.
Enhanced Equipment Performance
Optimizing machine utilization and efficiency is a primary goal for any business. Machine data collection provides actionable insights into factors influencing equipment performance, such as operating parameters, environmental conditions, and usage patterns. By analyzing this data, businesses can identify performance bottlenecks and implement targeted improvements to enhance overall equipment effectiveness (OEE).
Cost Savings and Operational Efficiency
Effective machine data collection contributes to significant cost savings and improved operational efficiency. Industries can identify maintenance requirements and allocate resources more effectively by monitoring machine health and performance closely. This reduces unnecessary maintenance activities and lowers costs associated with reactive approaches. Additionally, by optimizing maintenance schedules based on actual machine conditions, industries can extend machine lifespan and maximize return on investment.
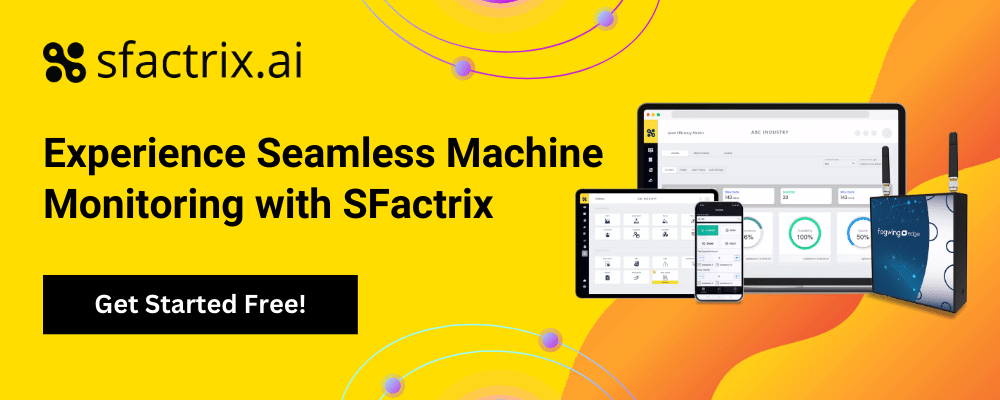
How Does Machine Data Collection Work?
Machine data collecting helps you track the health and performance of your machines so you can prevent issues before they happen. Here’s how it works:
Sensors are installed on your machines to collect data about their usage, environment, and performance. This data is then transmitted to a cloud-based monitoring system to be analyzed in real-time.
The data is used to create models of normal machine behavior. These models are then used to identify early warning signs of potential problems. This allows you to take preventive action before an issue causes downtime or expensive repairs.
Types of Data Collected for Improving Machine Performance
Industries are collecting a large volume of machine data for a good reason. Machine data collection is essential for condition based monitoring, which allows industries to detect and diagnose problems before they cause downtime or affect performance.
Machines are collecting various types of data; a few are listed below.
Vibration data: Vibration sensors measure the magnitude and frequency of vibrations, providing real-time data into the mechanical condition of rotating equipment.
Temperature data: Temperature sensors monitor the heat generated by machines and equipment, helping identify abnormal temperature variations that may indicate potential issues.
Pressure data: Pressure sensors measure fluid or gas pressure, enabling the monitoring of hydraulic and pneumatic systems for leaks, blockages, or pressure irregularities.
Electrical data: Electrical sensors monitor parameters such as voltage, current, and power consumption, providing information about the electrical health of machines and detecting abnormalities.
Fluid analysis data involves collecting samples from machines’ lubricants, coolants, or other fluids. This analysis helps identify contaminants, wear particles, or degradation affecting machine performance.
Best Practices to Optimize Machine Data Collection Processes
Machine data collection is critical to any condition-based monitoring program. With accurate and timely data, it is possible to make informed decisions about the health of your machines. Several best practices can help optimize your machine data collection processes:
1. Define Your Data Collection Goals
Before collecting data, it is essential first to define your goals. What information do you hope to glean from the data? What decision points will you use the data for? By clearly understanding your goals, you can ensure that you collect the right type and amount of data.
2. Select the Right Data Sources
Many machine data sources exist, including sensors, PLCs, SCADA systems, etc. Selecting the right mix of sources is crucial based on your specific needs. When choosing, consider factors such as accuracy, granularity, timeliness, cost, and availability.
3. Implement Effective Data Filtering
Not all machine data is created equal. Some data types may be more critical than others or need to be filtered to be helpful. For example, sensor data may need to be screened for noise before being used for condition monitoring. Implementing effective filtering techniques can improve the quality of your machine data and make it more useful for decision-making.
4. Use Automation Where Possible
Automating the collection and analysis of machine data can significantly improve the efficiency of your process. For example, software automatically detecting anomalies or trends in machine data can save time and effort. Automation can also help reduce errors and ensure the data collected is up-to-date and accurate.
5. Monitor Performance Regularly
Monitoring the performance of your machine data collection system regularly is essential for ensuring that it continues to meet your goals. Keep track of metrics such as speed, accuracy, and reliability over time to ensure you get the most out of your data collection system. Make any necessary adjustments as needed to keep it running optimally.
Future Trends in Machine Data Collection
Machine data collection is an ever-evolving field, with future trends promising further advancements. Integrating artificial intelligence and machine learning techniques enables more sophisticated data analysis and predictive capabilities. The convergence of machine data collection with Internet of Things (IoT) technologies opens new opportunities for interconnected and intelligent industrial systems. These emerging trends will shape the future of machine monitoring and maintenance practices.
Manufacturing industries heavily rely on machines. Data collected from sensors on factory machines helps manufacturers know how machines are performing, optimize their maintenance, reduce machine downtime, and even predict when machines might go wrong. This brings us to the next big trend in the manufacturing industry.
To learn more about IoT for machine monitoring, read What Is Machine Monitoring In Manufacturing? | Fogwing.io
SFactrix for Machine-generated Data Collection and Monitoring
SFactrix Machine Monitoring system
It is a prime example of a machine monitoring system or machine data collection software that enables predictive maintenance, remote monitoring, and data analytics in one comprehensive platform. By leveraging its capabilities, manufacturers can automate their processes further, reduce manual intervention, improve quality control measures, and minimize waste production, among other benefits.
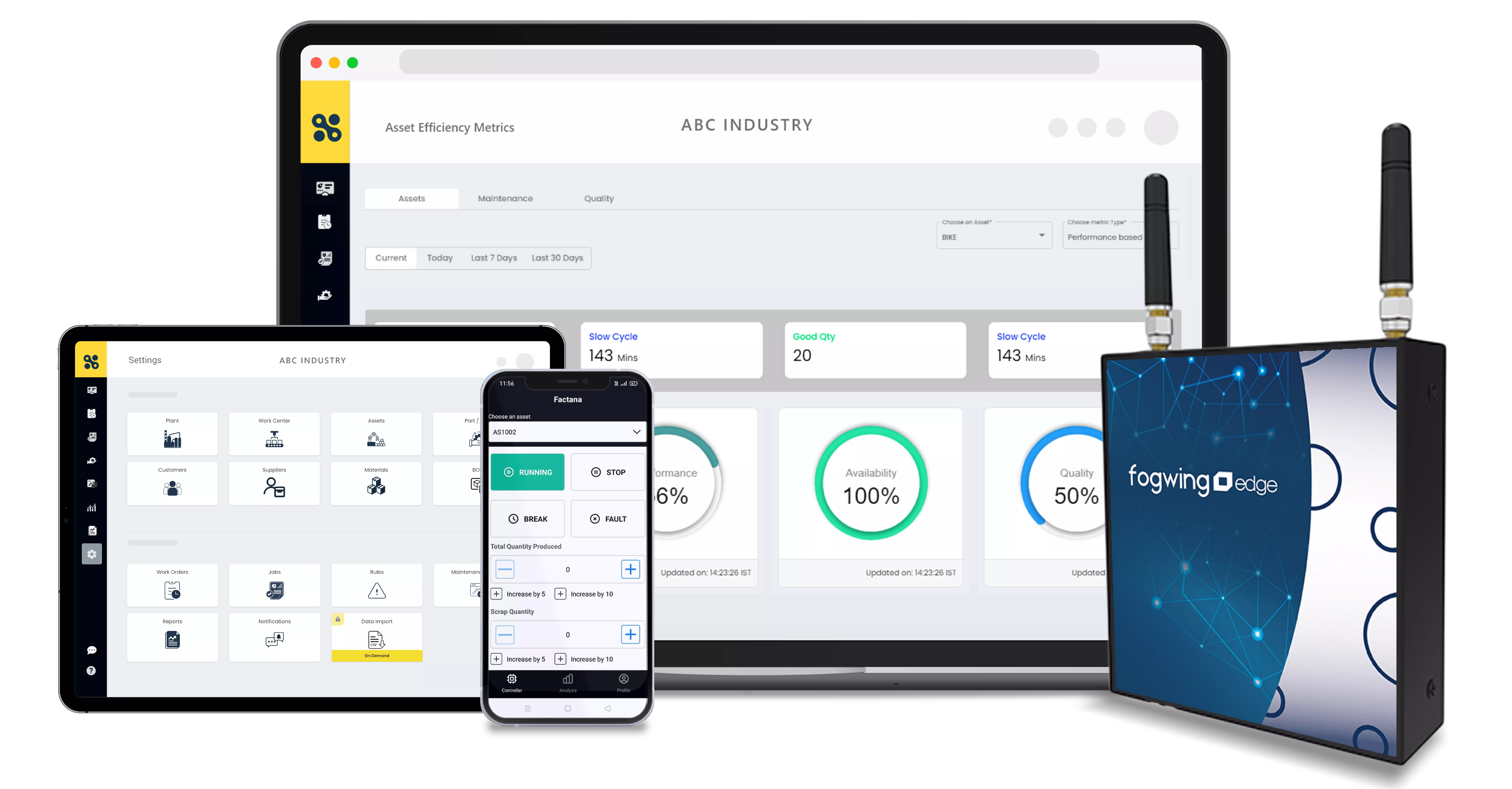
A few most efficient features of SFactrix machine monitoring are:
- SFactrix machine monitoring helps get complete visibility of production operations by automatically capturing machine data.
- It provides real-time data on the machine’s status and performance and improves the machine’s overall performance and efficiency.
- SFactrix machine condition monitoring software enables manufacturers to connect their machines to the software through IoT connectivity to monitor various key performance indicators (KPIs) on availability, performance, quality production, energy consumption, OEE, and many more.
- With the SFactrix machine monitoring system, businesses can monitor the real-time data of their machines and make the right moves and actions to improve the machine’s overall operability.
Machine monitoring aims to connect machines by deploying internet-enabled sensors that facilitate machine data collection and machine data transfer to the cloud. This data is further analyzed by advanced analytics tools to monitor machine performance.
SFactrix machine monitoring application powered with the cutting-edge Fogwing IIoT and HMI (Human-Machine Interfaces) device brings a new level of automation and intelligence to your machine data collection and analytics.
SFactrix machine monitoring is a game-changing solution that enhances the user experience in their Industry 4.0 journey. Real-time machine data collection is done through Fogwing IIoT and HMI and integrated into the central repository of the SFactrix machine monitoring application.
This cloud-based machine monitoring solution analyzes the data and presents the highly automated OEE metrics on the dashboard. This approach helps manufacturers with effortless machine OEE monitoring, utilization, downtime tracking, and optimization.
To learn more about how to automate production monitoring with the power of IoT, go through this page, Best Production Monitoring Solution | Fogwing Industrial Cloud SFactrix.ai
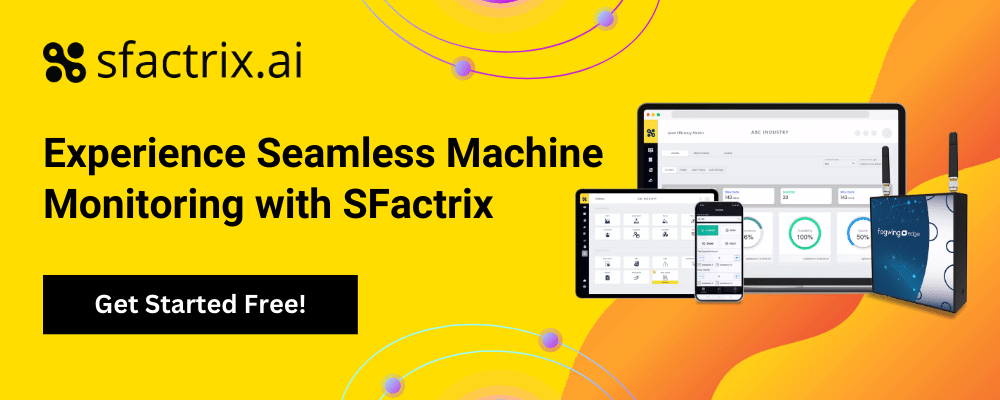
Conclusion
Therefore, machine data collection is essential for condition based monitoring. By collecting and analyzing real-time data from machines, industries can better understand their equipment’s performance and predict when service or maintenance will be needed. This knowledge improves safety and reliability while preventing costly downtime and repairs. Leveraging the power of big data analytics to collect accurate information about machines can give businesses an edge by keeping their machinery running efficiently.