If lengthy periods of transitioning between tasks are exhausting and hindering your productivity, you are not alone. We understand the difficulties that arise from these prolonged changeover times. That’s why we’re here to introduce a game-changing solution –SFactrix production monitoring. In this blog post, we’ll walk you through how leveraging data can revolutionize your operations and help significantly reduce changeover time. Get ready to bid adieu to downtime as we delve into the exciting world of turning data into action!
What is Changeover Time in Manufacturing?
Changeover time, also known as setup time or switch time, refers to the duration required to transition a production line or equipment from producing one product or batch to another. It involves various tasks such as machine adjustments, tool changes, material handling, cleaning, and other activities necessary to prepare the production line for the new product or process. In some cases, it may also involve reconfiguring the machinery or equipment used in production. Once these activities are completed, the actual process of manufacturing the new product can begin.
In any manufacturing process, some time is needed to switch from making one product to another. It can significantly impact productivity and efficiency, so it’s essential to understand what it is and how to reduce Changeover time.
The goal is to minimize changeover duration so production can ramp up quickly after a change. There are a few different ways to do this, such as using standard operating procedures (SOPs), investing in automated systems, and streamlining communication between departments.
If you want to reduce changeover time in your manufacturing operation, start by evaluating your current process and identifying areas where improvements can occur. Then, put together a plan of action and implement changes accordingly. You can significantly impact your bottom line with a little effort.
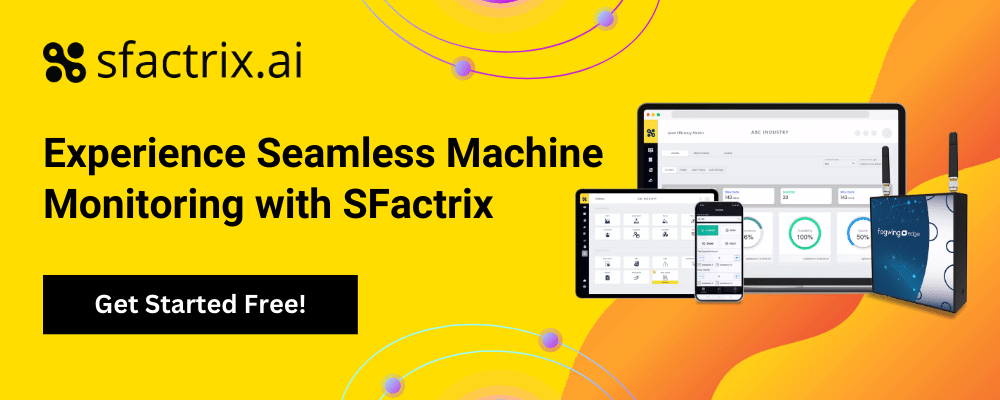
Benefits of Improving Changeover Time
Operational efficiency is crucial to success in any manufacturing organization. One of the primary indicators of operational efficiency is the changeover time or the time it takes to transition from one production cycle to another. Improving time changeover in manufacturing operations offers several significant benefits. Here are some key advantages:
Increased Productivity:
By reducing changeover time, manufacturers can minimize production line downtime and maximize the time spent on actual production. It leads to increased output and higher overall productivity. More products can be manufactured within the same timeframe, allowing companies to meet customer demands more efficiently and capture additional market share.
Enhanced Flexibility:
Shorter changeover duration prompts manufacturers to quickly switch between different products or batches. This flexibility is precious in industries with high product variety or frequent changes in customer demands. Efficient changeovers allow manufacturers to respond promptly to market changes, introduce new products faster, and adapt to evolving customer preferences.
Cost Savings:
Lengthy changeover times result in wasted resources, including labor, energy, and raw materials. By reducing changeover duration, manufacturers can optimize resource allocation and minimize waste. Additionally, shorter changeovers lessen the need for excess inventory and storage space, leading to cost savings in inventory management.
Improved Equipment Utilization:
Changeovers often involve adjusting machine settings, replacing tools, or reconfiguring equipment. Minimizing changeover times enables manufacturers to maximize equipment utilization by reducing the idle time between product runs. It ensures that machines are operational for more of the production cycle, resulting in higher overall equipment efficiency (OEE).
Quality and Consistency:
Changeover processes ensure proper setup and equipment calibration for the new product. By streamlining changeover procedures, manufacturers can enhance product quality and consistency. With shorter changeover times, there is less room for errors or misconfigurations that could impact product quality. It leads to higher customer satisfaction, reduced rework, improved product reliability, and higher manufacturing efficiency.
Continuous Improvement Culture:
Focusing on improving changeover times fosters a culture of constant improvement within the organization. By monitoring and analyzing changeover processes, manufacturers can identify bottlenecks, inefficiencies, and areas for improvement. This data-driven approach encourages teams to collaborate, experiment with innovative ideas, and implement changes to optimize changeover times and overall operational efficiency.
Collecting the Data You Need to Improve Changeover Times
When it comes to reducing changeover time, gathering the correct data is essential. Production monitoring can provide real-time insights into what is happening on the shop floor, helping you identify potential bottlenecks and inefficiencies.
Shop floor data can be collected manually or through production monitoring software. When gathering data manually, it is essential to have a consistent process so that all data is accurate and comparable. Production monitoring software can automate data collection and provide real-time visibility into production performance.
Once you have collected the data you need, it is time to analyze it to identify areas for improvement. Look for patterns and trends that can help you pinpoint where changeover duration can be reduced. Utilize historical and real-time data analysis to get a complete picture of your production process.
With the right data in hand, you can take action to reduce changeover time and improve efficiency on the shop floor. You can drive tangible improvements in your manufacturing operation by leveraging production monitoring.
Analyzing the Data to Identify Areas of Opportunities
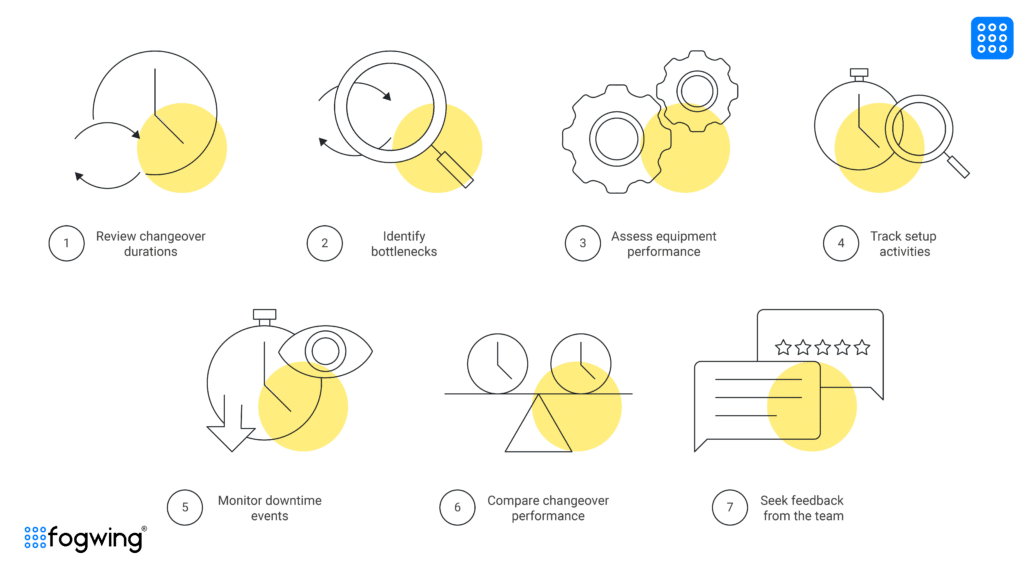
Analyzing the data collected during changeovers can help identify areas of opportunity for improving changeover times. Here’s how you can leverage data analysis to identify these areas:
Review changeover durations
Examine the data to determine the average changeover duration for different products or batches. Look for significant variations in changeover times between different setups. This analysis can help pinpoint specific changeovers that take longer than others, indicating areas where improvements can be made.
Identify bottlenecks
Analyze the data to identify bottlenecks or inefficiencies in the changeover process. Look for tasks or activities that consistently take longer or cause delays. These bottlenecks could be related to equipment setup, tool changes, material handling, or cleaning procedures. By identifying these bottlenecks, you can focus on streamlining those specific areas to reduce changeover times.
Assess equipment performance
Examine the data to understand equipment performance during changeovers. Look for instances of equipment breakdowns or malfunctions that resulted in extended downtime. Identify patterns or recurring issues that affect changeover times and prioritize addressing them to improve overall equipment reliability and minimize unplanned downtime.
Track setup activities
Analyze the data to track the time spent on various setup activities during changeovers. It can include adjusting machine settings, calibrating equipment, installing new tools, or changing product configurations. Identify any time-consuming activities that could be optimized or eliminated to expedite changeovers.
Monitor downtime events
Examine the data to identify instances and causes of downtime during changeovers. Look for reasons such as waiting for materials, unavailability of resources, or delays in accessing tools or equipment. Analyzing downtime events can help uncover opportunities to reduce or eliminate downtime by improving planning, resource allocation, or material handling processes.
Compare changeover performance
Compare changeover time across different shifts, operators, or production lines. Look for variations in performance and identify any best practices or areas where improvements can be shared and replicated. This analysis can help standardize changeover processes and drive consistency in performance across the organization.
Seek feedback from the team
Engage with the team involved in changeovers to gather their insights and observations. Their practical experience and knowledge can provide valuable context and help identify specific pain points or challenges that may not be evident from the data alone. Collaborative discussions can also foster a culture of continuous improvement and generate innovative ideas for optimizing changeover times.
How to optimize equipment setup and tooling to reduce changeover time?
Optimizing equipment setup and tooling is essential for minimizing changeover time in manufacturing processes. One approach is to standardize setup procedures by documenting and communicating clear instructions for equipment setup and tooling changes. By establishing standardized procedures, operators can follow a consistent and efficient process, reducing the likelihood of errors and delays during changeovers.
Another strategy is to pre-stage tools and materials near the production line. Having the necessary tools and materials readily available saves time by eliminating the need for operators to search for or retrieve items from remote locations. Setting up well-organized staging areas with labeled and easily accessible tools and materials allows quick and seamless access during changeovers.
In addition, implementing quick-change mechanisms can expedite equipment setup and tooling changes. Utilizing standardized connectors, quick-release fasteners, or modular components enables rapid adjustments or exchanges, minimizing the time required for disassembly, reconfiguration, and reassembly.
Furthermore, utilizing dedicated tooling carts or storage systems can improve efficiency. These carts can be specifically designed to hold and organize tools required for each product or process, ensuring that the necessary tools are easily accessible and readily available during changeovers.
Manufacturers can significantly reduce changeover time and enhance operational efficiency by optimizing equipment setup and tooling through standardization, pre-staging, quick-change mechanisms, and dedicated tooling carts.
Developing Strategies for Reducing Production Changeover in Manufacturing
As the saying goes, “Time is money.” It couldn’t be more accurate in the world of production and manufacturing. Changeover time is the time it takes to switch from producing one product to another. Ideally, this time would be as short as possible to minimize downtime and maximize efficiency.
Several strategies can be employed to reduce changeovers. One is to streamline the process itself by eliminating unnecessary steps. Another is to ensure that all the equipment and tools needed for the changeover are readily available and in good working order. Proper personnel training is also crucial so that every worker knows their role and responsibilities in the process.
By employing these strategies, manufacturers can reduce changeover duration and increase productivity.
Implementing the Strategies and Testing Results
Implementing the strategies mentioned above requires a systematic approach. Start by providing comprehensive training to operators, enhancing communication, and utilizing visual aids and checklists to streamline the changeover process. Simplify procedures by eliminating unnecessary tasks and parallelizing activities whenever possible to minimize idle time.
SMED in Manufacturing
Implementing Single-Minute Exchange of Dies (SMED) is a lean manufacturing technique that significantly reducing changeover times. SMED in manufacturing emphasizes separating internal and external setup tasks, converting internal tasks to external ones, and simplifying and streamlining the remaining internal tasks. This systematic approach helps optimize the changeover process.
Continuously monitor and evaluate changeover performance by collecting data and tracking relevant metrics. Analyze the results to identify areas for further improvement. By testing the strategies, manufacturers can measure their impact on changeover times and overall operational efficiency. Regular evaluation allows for iterative adjustments and the identification of additional opportunities for optimization.
By implementing these strategies and testing the results, manufacturers can reduce changeover time, improve productivity, and enhance overall operational efficiency.
After a new production line has been installed and is operational, monitoring performance to identify any issues that may arise is essential. Monitoring performance makes it possible to quickly identify and correct problems, reducing changeover time.
Several factors should be monitored when assessing production line performance. These include overall equipment effectiveness (OEE), cycle time, yield, and scrap rate. Additionally, it is essential to track the number of changeovers that are required to maintain production levels. Tracking these factors makes it possible to identify trends and areas for improvement.
Monitoring performance after implementation is crucial to ensure the new production line runs smoothly and efficiently. Tracking the relevant metrics makes it possible to make necessary improvements and reduce changeover time.
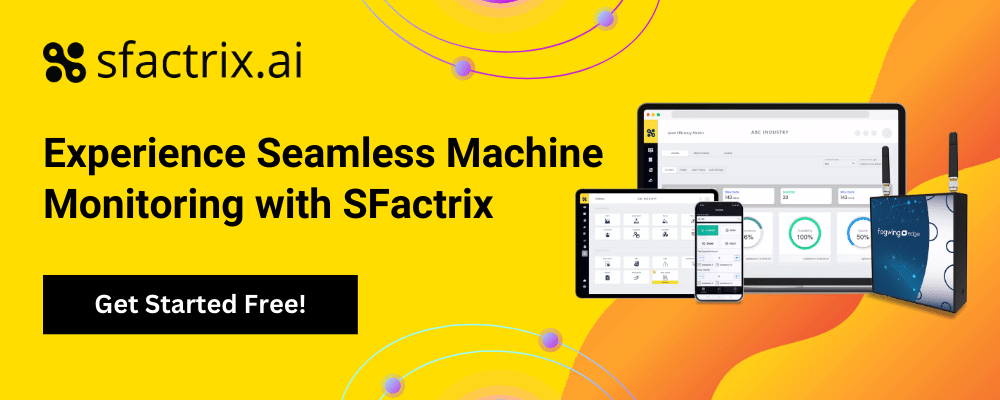
How to Reduce Changeover Time using SFactrix?
SFactrix production monitoring significantly reduces changeover time by offering real-time data into production processes. By continuously monitoring and analyzing production data, it identifies bottlenecks, inefficiencies, and areas for improvement in changeover procedures. With this valuable data, manufacturers can optimize changeover sequences, streamline processes, and implement best practices to minimize downtime during changeovers. SFactrix’s data-driven approach empowers businesses to make informed decisions, fostering a culture of continuous improvement. As a result, production changeover becomes more efficient and seamless, leading to increased productivity, reduced operational costs, and enhanced overall manufacturing efficiency.
SFactrix production monitoring is an all-in-one digital platform to automatically capture data, perform real-time data analysis, and track operational efficiency. SFactrix production monitoring solution seamlessly connects with your machines, capturing operational data without human intervention.
With the inbuilt Manufacturing Intelligence module, SFactrix provides a comprehensive suite of features designed to enhance your production efficiency. Machine data helps gain valuable insights into key performance indicators (KPIs), offers real-time downtime alerts, tracks loss-based metrics, analyzes scrap trends, and effortlessly monitors quality metrics.
Integrated with Fogwing IoT, the SFactrix production monitoring system helps manufacturers access actionable insights that can enable them to optimize production processes and increase efficiency across the entire production line.
Conclusion
Changeover time is a crucial part of the overall production process, and effective data-driven action can make all the difference. Manufacturers can assess the strategies’ effectiveness by collecting and analyzing relevant data, tracking key performance indicators, reviewing changeover procedures, and engaging with the team. This ongoing monitoring enables the identification of areas for further improvement. It ensures that the goal of minimizing changeover time is achieved. By continuously evaluating performance and making necessary adjustments, manufacturers can optimize changeover processes, enhance operational efficiency, and maintain a competitive edge in the dynamic manufacturing landscape.