In the ever-evolving world of manufacturing, the pursuit of efficiency is paramount. At its center lies the concept of manufacturing throughput, a crucial metric determining how efficiently products are created and delivered to customers. It serves as the pulse of any production facility, and manufacturers are perpetually on the quest to elevate throughput while maintaining quality and cost-effectiveness. In this comprehensive guide, we will explore manufacturing throughput. We’ll unravel its intricate components, explore the fundamental strategies required to maximize efficiency and provide actionable insights for industry professionals.
What is Throughput?
In manufacturing, it simply refers to the production rate, the number of units produced over a while, or the speed at which something is processed. It’s often used to describe the number of products that move through the manufacturing process in a given period.
It can be measured in units per hour and is a key metric for evaluating manufacturing efficiency. Various factors can influence throughput, including factory layout, equipment utilization, operator productivity, and workflow.
Improving through put requires a holistic approach that looks at all aspects of the manufacturing process. Some common strategies for increasing through put include:
- Eliminating or reducing bottlenecks in the production line.
- Improving equipment utilization.
- Increasing operator productivity.
- Optimizing workflows.
- Improving communication and coordination among all stakeholders.
What are 3 Factors That Would Influence Throughput?
A variety of factors exert their influence on this metric. Discerning and effectively managing these factors are essential for enhancing operational efficiency:
Equipment Efficiency
The performance of manufacturing equipment is pivotal in determining through put. Downtime due to equipment breakdowns or routine maintenance can drastically impede throughput. Hence, implementing a robust maintenance regime and investing in high-caliber machinery are quintessential.
Workforce Productivity
The workforce’s productivity is another cornerstone of throughput optimization. A skilled and motivated workforce contributes significantly to maintaining high throughput levels. Strategies encompassing workforce training, efficient scheduling, and employee engagement initiatives become imperative to augment productivity.
Process Optimization
The efficiency of manufacturing processes is the bedrock upon which throughput stands. Detecting bottlenecks, streamlining workflows, and embracing lean manufacturing principles are pivotal to process optimization and the subsequent elevation of throughput.
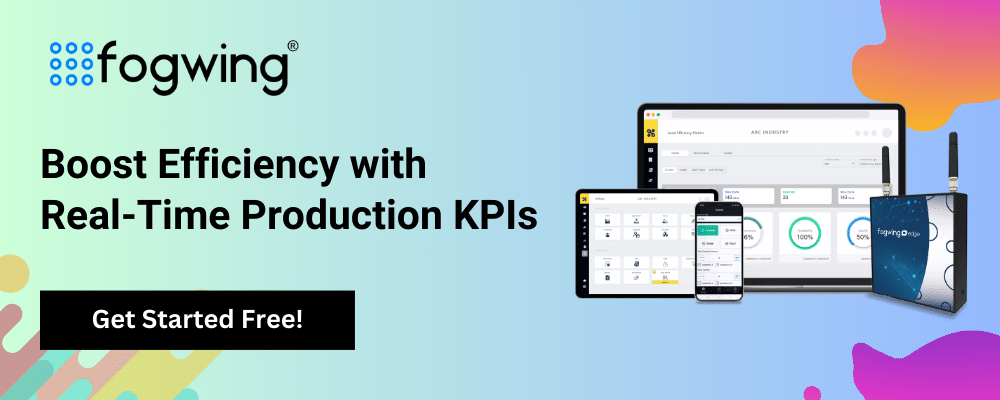
What is the Formula for Throughput in Manufacturing?
In manufacturing, throughput measures the number of units that move through the production process in a given period.
The formula for throughput calculation is:
Units produced per day / Average time to make one unit
Throughput is increased by increasing the number of units produced daily or reducing the average time to make one unit. There are a variety of strategies to increase throughput and improve efficiency in manufacturing.
Difference Between Capacity and Throughput in Manufacturing?
Capacity and throughput are two crucial concepts in manufacturing, and they refer to different aspects of a manufacturing process. Capacity is the theoretical maximum output that a manufacturing system can achieve under ideal conditions. At the same time, throughput represents the actual production rate, considering real-world factors and constraints. Both capacity and throughput are essential for managing and optimizing manufacturing processes. Still, they serve different purposes and provide different perspectives on performance.
How Do You Increase Throughput?
Increasing throughput in manufacturing is essential for improving productivity, reducing costs, and effectively meeting customer demand. To boost this, you can employ a variety of strategies and best practices:
Improve Equipment and Technology
Increasing throughput in manufacturing is essential for improving productivity, reducing costs, and effectively meeting customer demand. To boost throughput, you can employ a variety of strategies and best practices:
Optimize Production Processes
- Streamline and simplify processes to minimize unnecessary steps and delays.
- Apply lean manufacturing principles to eliminate waste and improve efficiency.
- Implement process automation where possible to reduce manual labor and human error.
Improve Equipment and Technology
- Invest in modern machinery and equipment that can handle larger volumes and operate at higher speeds.
- Ensure that your equipment is properly maintained to minimize downtime.
- Implement predictive maintenance to prevent unexpected breakdowns.
Data Analysis and Continuous Improvement
- Collect and analyze data on production processes to identify areas for improvement.
- Implement continuous improvement methodologies such as Six Sigma or Kaizen.
- Monitor key performance indicators (KPIs) related to throughput and make data-driven decisions.
Workforce Training and Development
- Train employees to operate equipment efficiently and safely.
- Cross-train workers to perform multiple tasks and fill in for one another when necessary.
- Encourage a culture of continuous improvement and employee involvement in problem-solving.
Supply Chain Management
- Optimize your supply chain to ensure a steady flow of materials and components.
- Consider using just-in-time inventory systems to reduce excess inventory holding costs.
- Collaborate closely with suppliers to improve lead times and minimize supply disruptions.
Quality Control and Quality Assurance
- Implement robust quality control measures to reduce defects and rework.
- Use statistical process control (SPC) techniques to monitor and maintain product quality.
- Reduce the need for inspections by building quality into the production process.
Production Scheduling
- Implement efficient production scheduling algorithms and software.
- Use capacity planning to balance production with demand.
- Consider using flexible manufacturing systems that can adapt to changing production needs.
Bottleneck Analysis
- Identify and address production bottlenecks that limit throughput.
- Prioritize improvements in bottleneck areas to impact overall throughput the most.
Inventory Management
- Optimize inventory levels to avoid overstocking or stockouts.
- Use demand forecasting to plan production and inventory more accurately.
Capacity Expansion
- If demand consistently outpaces production capacity, consider expanding your facilities or adding additional shifts.
- Ensure that any capacity expansion is well-planned and cost-effective.
Kaizen Principles for Sustainable High Throughput Growth
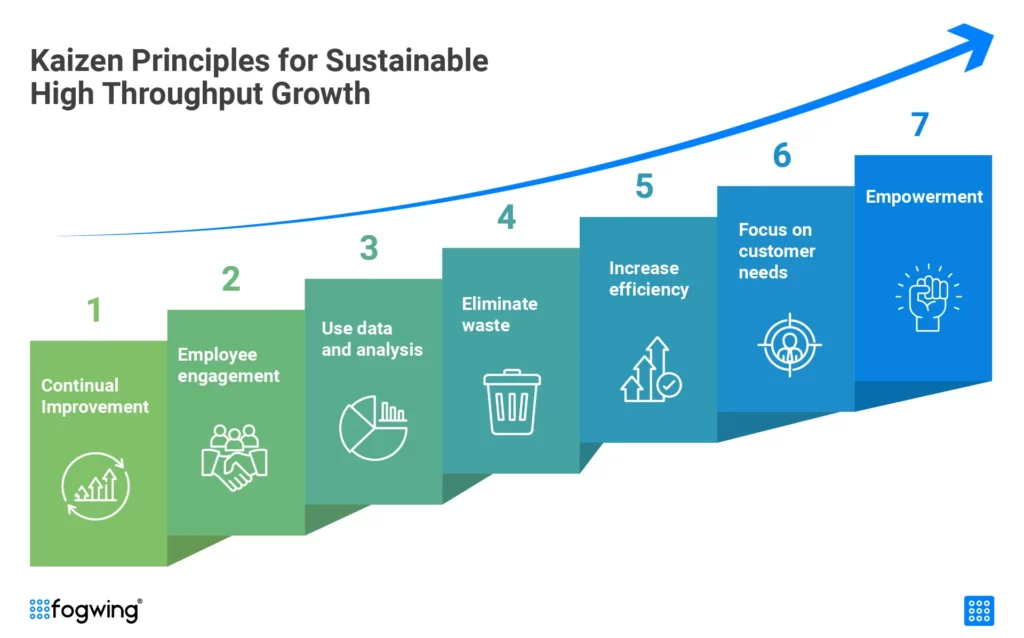
Kaizen principles, a Japanese word meaning “improvement” or “change for the better,” can be applied to manufacturing to achieve sustainable throughput growth. The main objective of Kaizen is to eliminate waste in all types or forms, including overproduction, waiting, transportation, inventory, motion, and defects. By doing so, manufacturing organizations can increase efficiency and productivity while reducing costs.
There are seven core principles of Kaizen:
1. Continual improvement – Kaizen is an ongoing process that should be embedded into an organization’s culture. It should be seen as a never-ending journey rather than a destination.
2. Engagement of all employees – The entire workforce in the organization should be involved in the Kaizen process from the top down. It ensures that every employee is working towards the same goal and that there are no silos within the organization.
3. Use data and analysis – Data should drive decision-making in Kaizen initiatives. It helps to ensure that improvements are based on evidence rather than assumptions.
4. Eliminate waste – As mentioned above, one of the main goals of Kaizen is to eliminate waste in all forms. It includes anything that does not add value to the final product or service.
5. Increase efficiency – Organizations can do more with less by eliminating waste and increasing efficiency. It allows them to reinvest savings into other business areas or pass on savings to customers through lower prices.
6. Focus on customer needs – Kaizen should always be focused on meeting customer needs as efficiently and effectively as possible. It ensures that the organization provides value to its customers, which helps build loyalty and trust.
7. Empowerment – Employees should be empowered to own their work. It encourages creativity and fosters a culture of innovation, which can lead to more efficient processes and higher levels of throughput growth.
Analyzing Performance Metrics
It is critical to analyze your performance metrics to maximize your manufacturing throughput. There are several different ways to do this. Still, using a statistical analysis software package is one of the most effective. This type of software will allow you to see how your manufacturing process is performing over time and identify any areas that need improvement.
One of the critical things to look for when analyzing your performance metrics is bottlenecks in your manufacturing process. These bottlenecks can severely limit your throughput and cause significant disruptions in your operation. By identifying these bottlenecks and addressing them, you can often significantly improve your overall manufacturing efficiency.
Another essential thing to remember when analyzing your performance metrics is that they should be constantly monitored and updated. As your manufacturing process changes, so will the way your metrics need to be explored. By keeping an up-to-date record of your performance data, you can ensure that you are always making the most informed decisions about how to improve your manufacturing process.
Increase your Throughput with Fogwing Machine Monitoring
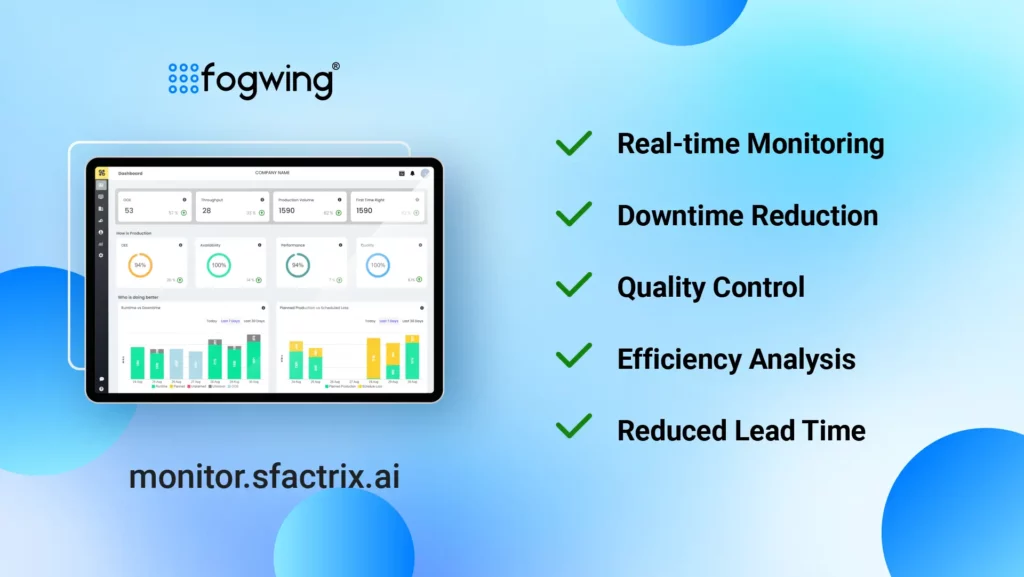
Fogwing machine monitoring solution significantly increases manufacturing throughput by providing real-time visibility, data analysis, and insights into machine performance and production processes. Here’s how Fogwing machine monitoring contributes to high throughput:
Real-time Monitoring
- Fogwing machine monitoring solution collects real-time data from machines and equipment using sensors. It presents the data on the application dashboard.
- Operators and managers can monitor machine status, production rates, and other critical information at a glance through this intuitive dashboard.
Downtime Reduction
- Fogwing machine monitoring solution helps identify and categorize downtime events due to equipment breakdowns, changeovers, or other reasons.
- By pinpointing the causes of downtime, manufacturers can take corrective actions to minimize interruptions and keep machines running optimally.
Quality Control
- Machine metrics software can monitor the quality of products.
- Immediate alerts can be generated if quality deviations are detected,
Efficiency Analysis
- Fogwing provides insights into machine cycle times, setup times, and production rates.
- Manufacturers can identify inefficiencies and bottlenecks in the production process and make necessary adjustments to optimize throughput.
Reduced Lead Times
- Lead times can be minimized by closely monitoring machine performance and production processes.
Fogwing machine monitoring solution empowers manufacturers with the data and insights to optimize machine and production efficiency, reduce downtime, improve quality, and make informed decisions. By leveraging these capabilities, manufacturing throughput can be increased, leading to higher productivity and competitiveness in the market.
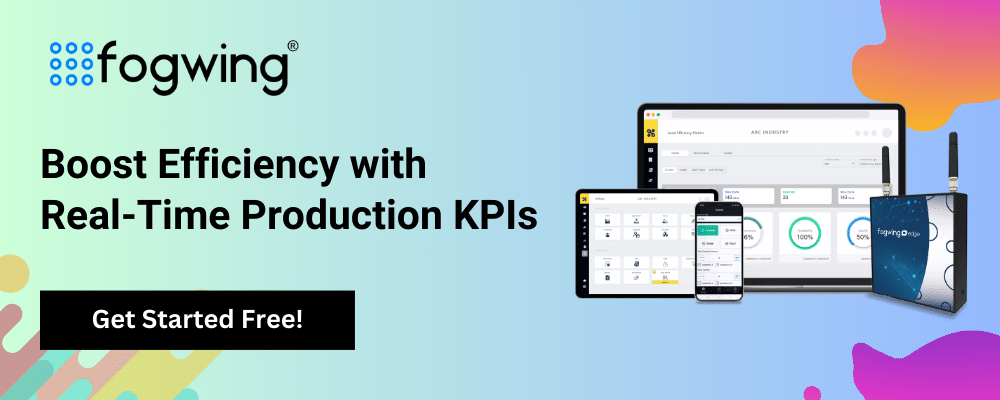
Conclusion
Manufacturing throughput stands as the lifeblood of any production establishment. It represents not only the quantity but also the efficiency with which products are created and delivered. With a clear understanding of the factors influencing it, equipped with the throughputs formula and a treasure trove of strategies, manufacturers can embark on a voyage to optimize their operations and secure a competitive edge in the ever-evolving market scenario. It’s imperative to remember that the pursuit of heightened throughput is not merely a destination but an ongoing expedition, necessitating perpetual improvement and adaptability to the dynamic tides of manufacturing.