Welcome to the world of manufacturing, where innovation meets precision. As industries mature and technology progresses at an unprecedented rate, one thing remains constant: Fixed Assets.
In finance and accounting, it is a fundamental concept crucial to a company’s financial health. It is an integral part of business balance sheets and significantly impacts financial stability. From towering machines to cutting-edge robotics, these tangible investments or long-term assets play a vital role in shaping the success of manufacturing companies worldwide.
In this blog, we will delve into fixed assets,what is fixed assets meaning, how businesses manage them, and understand why they are more than just items on a balance sheet.
So, whether you are a seasoned professional or just a newbie in the field of manufacturing, join us as we explore how these invaluable assets fuel innovation, streamline operations and pave the way for tomorrow’s breakthroughs in this exhilarating industry.
What are Fixed Assets?
Fixed or non-current assets are physical assets that a business owns for an extended period, typically more than one year, to produce goods or services. These assets include equipment, machinery, buildings, vehicles, and other physical assets essential for day-to-day operations. These assets are not meant for resale but are critical for generating revenues for the organizations. It is necessary for the day-to-day operations of a company. Unlike inventory or other short-term assets, fixed assets are not for resale and are also called long-term assets.
Fixed assets Examples include:
- Property: Land, buildings, and any improvements on the land or buildings are a few long-term assets associated with organizations.
- Plant: Machinery, equipment, and vehicles used in the production or operations of the business.
- Equipment: Office furniture, computers, and other tools used for business operations.
- Intangible Assets: While not tangible, patents, copyrights, trademarks, and goodwill are also considered long-term assets.
Fixed assets are subject to depreciation, representing the allocation of the asset’s cost over its useful life. Depreciation is a way to reflect the asset’s wear and tear and match the asset’s price with the revenue it generates over time. Tracking long-term assets is crucial for reporting, tax purposes, and managing a company’s resources.
Why are Fixed Assets Essential?
Fixed Assets are the backbone of a business, encompassing tangible assets like property and equipment. Beyond their operational significance, these long-term investments contribute to revenue generation, serve as collateral for financing, and impact strategic decision-making. Understanding their value and management is essential for sustained business success.
Here are a Few Reasons Why Fixed Asset is Crucial in Business:
- Operational Necessity: Fixed assets play a vital role in the day-to-day operations of a business. For instance, machinery and equipment are essential for manufacturing processes, while office buildings and computers are crucial for administrative functions. These assets are necessary for many businesses to function effectively.
- Long-Term Value: Long-term assets are a significant investment for organizations as they are usually more expensive and have longer lifespans than other assets. Nevertheless, they also provide long-term value. For instance, a company’s manufacturing equipment contributes to its production capacity over several years.
- Revenue Generation: Various Fixed assets are directly involved in revenue generation. For example, a delivery truck for a logistics company or manufacturing machinery in a factory directly contributes to the production and delivery of goods and services, ultimately generating revenue.
- The basis for Lonas and Financing: Organizations can leverage their valuable long-term assets as loan collateral, enhancing their worthiness and increasing their chances of obtaining financing for strategic initiatives. Lenders are often more inclined to extend credit or loans to businesses with significant fixed assets, as they provide a tangible and reliable source of repayment. The availability of financing can be critical in supporting business growth, innovation, and expansion, enabling organizations to pursue new opportunities and achieve their strategic goals.
- Depreciation for Tax Purposes: Over time, the value of long-term assets decreases due to wear and tear, known as depreciation. However, businesses can benefit from depreciation as it is a non-cash expense to lower their taxable income. These fixed asset accounting practices allocate the asset’s cost over time, reducing the asset’s book value on the balance sheets. It is essential regarding tax planning and managing cash flow. It, in turn, helps to reflect the company’s financial position accurately.
- Investor and Creditor Confidence: Well-maintained and efficiently used fixed assets foster confidence among investors and creditors. They are a testament to a business’s ability to operate efficiently over the long haul and its strategic investment in its infrastructure. These assets reflect the company’s sound financial management, leading to a sustainable and profitable business.
- Strategic Decision-Making: Accurate knowledge of long-term assets’ value, condition, and valuable life is crucial for businesses to make strategic decisions. It is essential to determine the appropriate time to upgrade, replace, or dispose of assets to maintain competitiveness and efficiency.
Long-term assets are vital for a business’s ongoing operations and growth. It contributes to revenue generation, can be used as collateral, has tax implications, and plays a crucial role in financial health and strategic decision-making.
How do we Maintain Fixed Assets in Manufacturing Industries?
Maintaining Fixed Assets in manufacturing industries involves a comprehensive approach to ensure longevity, efficiency, and compliance. Organizations follow a few critical practices to keep a fixed asset.
- Regular Inspections: Regular inspections are the key players of proactive fixed asset management in manufacturing. Consistently inspecting machinery and equipment reveals signs of wear, tear, or potential issues, enabling swift corrective action. This vigilant approach mitigates the risk of costly breakdowns and optimizes operational efficiency. Organizations foster a culture of reliability and sustainability by addressing emerging concerns early on through timely repairs or replacements. The strategic integration of routine inspections aligns with a forward-thinking maintenance model, ensuring that fixed assets examples operate at peak performance, contributing to a seamless production process, and fortifying the resilience of the manufacturing infrastructure.
- Preventive Maintenance Program: A robust preventative maintenance program is paramount in sustaining the manufacturing efficiency of fixed assets. Adhere to manufacturer recommendations to create tailored schedules that proactively address potential issues. Regular servicing and lubrication of machinery are integral components, systematically enhancing their lifespan and optimizing overall performance. This strategic commitment averts unforeseen disruptions and fosters a culture of proactive care, ensuring equipment operates at peak efficiency. Organizations can utilize Fogwing Asset+, an innovative CMMS application, to prioritize preventive maintenance measures on long-term assets to bolster reliability, minimize downtime, and fortify the longevity of crucial assets, ultimately contributing to streamlined operations and sustained productivity in manufacturing industries.
- Asset Tracking and Management: Harnessing the power of advanced asset-tracking systems is pivotal while managing the fixed assets within the manufacturing landscape. It offers real-time insight into each asset’s location, condition, and maintenance history. With this advanced data, organizations can strategically plan maintenance schedules, ensuring timely interventions to prevent more extensive damage to long-term assets in the long run. Additionally, the complete visibility provided by the asset tracking software facilitates the optimization of asset usage, enabling informed decision-making and resource allocation. Integrating robust asset tracking and management systems becomes a cornerstone in enhancing operational efficiency and maintaining the health of valuable manufacturing assets.
- Employee Training: Enhancing the operational proficiency of the fixed assets begins with providing ample employee training. Focusing on the proper usage and care of equipment in the manufacturing setting is very much essential. Staff will receive training on equipment functions and maintenance protocols to minimize misuse-related damages. The investment in training not only cultivates a skilled workforce but also acts as a preventive measure, mitigating potential equipment breakdowns. The symbiotic relationship between informed employees and well-maintained machinery converges to amplify overall operation effectiveness. They foster a culture of expertise, care, and fixed asset management within the manufacturing ecosystem.
- Documentation and Record Keeping: Introducing a robust system for documentation and record keeping of fixed assets is pivotal in effectively managing the assets within the organization. Comprehensive records encompass purchase dates, maintenance history, and depreciation details, a base for intact financial reporting. It ensures compliance with regulations and informed strategic decision-making. This meticulous documentation enhances transparency and accountability and is valuable for audits and assessments. Maintaining accurate records becomes indispensable, aligning the manufacturing enterprise with financial best practices and facilitating informed data-driven choices for sustainable growth.
- Depreciation Monitoring: Vigilant monitoring of fixed asset depreciation is vital for sound financial management in manufacturing. Regularly reviewing and updating the depreciation schedule ensures accurate fixed asset valuation. Practice is indispensable for proper financial planning, aligning budgets with absolute fixed asset values, and facilitating precise reporting. By keeping depreciation schedules dynamic, manufacturing enterprises enhance fiscal transparency, enabling stakeholders to make informed decisions based on up-to-date and accurate assessments of asset worth. This strategic approach fortifies financial integrity and contributes to a comprehensive and forward-looking financial strategy for sustained success.
- Energy Efficiency: Prioritizing energy efficiency is critical for maintaining fixed assets in manufacturing industries. Implementing energy-efficient practices for machinery and equipment not only serves to cut operational costs but also aligns with broader sustainability initiatives. Manufacturing enterprises enhance their bottom line by optimizing energy consumption and contributing to environmental responsibility and fixed asset management. This dual impact reflects a commitment to financial judgment and economic stewardship, reinforcing the industry’s resilience in an era where sustainable practices are integral to long-term success. Investing in energy efficiency is the cornerstone for cost-effectiveness and corporate responsibility in manufacturing.
- Risk Management: In the manufacturing industry, it is crucial to have proactive risk management strategies in place to protect fixed assets. Conducting thorough assessments to identify and mitigate risks associated with assets, such as cybersecurity threats affecting automated systems and safety hazards associated with heavy machinery, is essential. Businesses face unseen disruptions by addressing vulnerability, ensuring operational continuity and employee safety. The risk management approach protects assets and bolsters the overall security posture of the manufacturing ecosystem.
- Collaboration with Suppliers: Nurturing collaborative relationships with equipment suppliers is crucial for effective fixed asset management in manufacturing. Open communication ensures businesses stay updated on important information, such as recommended maintenance procedures provided by manufacturers and recalls. It enhances equipment reliability and performance and enables swift response to emerging asset-related issues. Manufacturers can navigate challenges seamlessly, optimize asset functionality, and stay aligned with industry best practices by cultivating dynamic partnerships with suppliers. It also contributes to a resilient and well-informed operational framework.
Is there Any Software to Maintain Fixed Assets in Manufacturing Industries?
Fogwing Asset+ is a Smart CMMS solution with IoT and AI technology capabilities. With the Fogwing Asset+ platform, organizations will have tools that will enable them to streamline their maintenance operations on the Fixed assets, offering real-time insights that lead to enhanced operational efficiency and reduce maintenance-related costs. Some of the standard functionalities provided by Fogwing Asset+ in fixed assets management in manufacturing industries are:
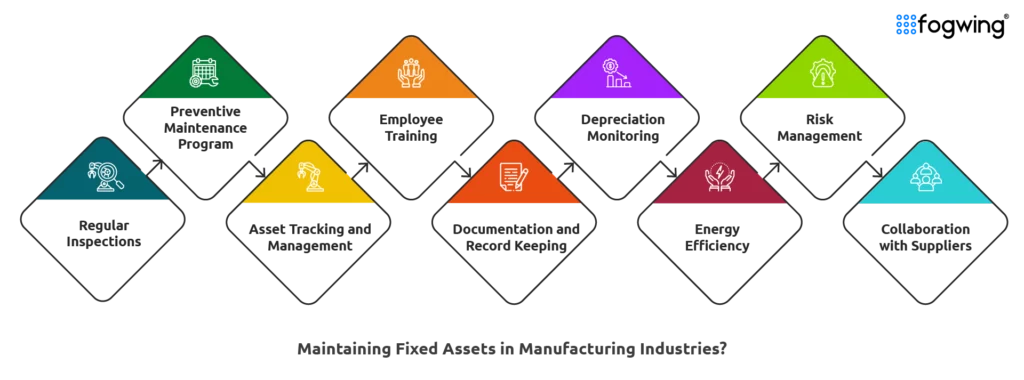
Asset Tracking Software and Visibility: The Fogwing Asset+ platform likely provides real-time tracking and visibility of the location and status of fixed assets. It is a feature that is crucial for managing and locating organizational assets effectively within a manufacturing facility.
Preventive Maintenance: The Fogwing Asset+ system offers advanced features for smart asset management and maintenance, like scheduling and tracking preventive maintenance tasks. It enables organizations to ensure that machinery and equipment are regularly serviced and maintained to prevent breakdowns and downtimes.
Documentation and compliance: Fogwing Asset+, a Smart CMMS software, enables organizations to maintain accurate records regarding fixed assets, including purchase details, maintaining history, and compliance documentation. It will be essential for audits, compliance reporting, and strategic decision-making.
Integration With IoT Sensors: The Fogwing Asset+ is a smart asset management software incorporating IoT capabilities that leverage sensors to gather real-time data on equipment performance. Organizations can later utilize the data collected for predictive maintenance, enabling them to identify potential issues before they become critical.
Supplier Collaboration: The Fogwing Asset+ System facilitates and simplifies communication with the parts suppliers, allowing timely updates, recalls, and recommended maintenance procedures. It enables organizations to stay informed about the fixed assets and maintain them according to the manufacturer’s guidelines.
Methods to Calculate Fixed Asset Depreciation
Long-term asset depreciation is an approach to accounting for the decrease in the fixed value over time. It is a fixed asset accounting principle that enables organizations or businesses to spread out the cost of an asset over its useful life rather than expensing it all at once.
Here are some methods utilized to calculate fixed asset depreciation:
- Stright-line method: The straight-line method is the most common and straightforward method for calculating the depreciation of fixed assets in organizations. This method deducts equal depreciation each year over the asset’s useful life.
The Fixed Asset Formula for calculating straight-line depreciation is:
Depreciation expense = (Initial Cost – Salvage value) / Useful life
Where:
- The initial cost is the original cost or purchase price of the assets.
- Salvage Value is the asset’s estimated value at the end of its useful life.
- Useful life is the estimated years the asset will be productive or in use.
Example: A company purchases a computer for $1500 with a salvage value of $200 and a useful life of 5 years. The annual depreciation expense would be $260.
- Declining Balance Depreciation: This method assigns a higher depreciation expenditure to the early years of a fixed asset’s useful life and a lower depreciation expense to later years.
The Fixed Asset Formula for calculating declining balance depreciation is:
Depreciation Expense = (Book Value at the beginning of the year) x (Declining balance rate)
Where:
- Depreciation Rate is a fixed percentage determined based on the chosen method (Example: double declining balance, 150% declining balance).
- Book Value at the beginning of the year is the asset’s book value at the start of the current accounting period.
Example: A company purchases a car for $20,000 with a salvage value of $1,000 and a useful life of year five years. The declining balance rate is 30%. The annual depreciation expense in the first year would be $3,000. The annual fixed asset depreciation expense in the second year would be $1,800, and so on.
- Unit of Production Method: The unit of production method is based on the actual usage of the fixed assets. It is a method used for depreciated assets based on usage rather than age. The depreciation expense varies with the number of units the long-term assets produce.
The Fixed Asset Formula for calculating units of production depreciation is:
Depreciation expense = (Units produced during the year / Estimated total units to be produced) x (Cost – salvage value of assets)
Where:
- The number of Units Produced in a given is the actual number of units produced during the accounting period.
- The Total Estimated Unit is the total number of units the fixed asset is expected to produce over its useful life.
- The total cost of the asset is the fixed asset’s original cost or purchase price.
Example: A company purchases a truck for $25,000 with a salvage value of $2,500 and an estimated useful life of 100,000 miles. The car travels for 20,000 miles in the first year. The annual depreciation expense would be $5,000 ((20,000 miles / 100,000 miles) x $22,500).
Sum-of-the-year-digits (SYD) depreciation, double-decreeing balance, and MACRS (Modified Accelerate Cost Recovery System) are additional methods to calculate fixed asset depreciation. Remember that the choice of method can impact financial statements, tax liability, and cash flow. It’s essential to consult fixed asset accounting standards like GAAP or IFRS and seek advice from accounting professionals to determine the most appropriate method for your situation.
Conclusion
In conclusion, fixed assets are integral in driving efficiency and growth in the manufacturing industry. Properly managing and utilizing these assets enables organizations to reduce operating costs, increase productivity, and drive profitability.
It is a key to sustaining success and staying ahead of competition in today’s fast-paced market. As technology advances, demand for quality products increases, so companies need to recognize the importance of their long-term assets in achieving long-term success.
So, organizations need to utilize an advanced cutting-edge CMMS platform like Fogwing Asset+ to maintain their fixed assets effectively. Its advanced features enabled organizations to ensure long-term success and continued growth in an ever-evolving industry. The potential for growth and success in the manufacturing industry is endless with the proper utilization of fixed asset management.
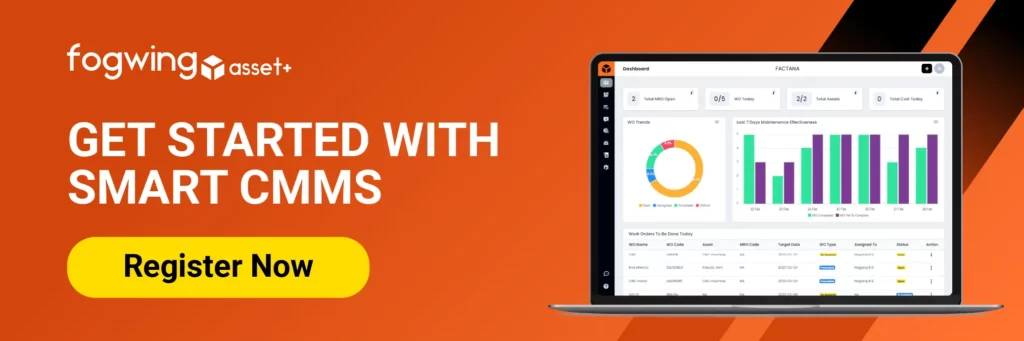