Welcome to our blog post on “Decoding Common Causes of Machine Failure” – a topic that every industrial enthusiast and business owner should pay attention to! Imagine the frustration of encountering unexpected machine breakdowns, leading to costly repairs, production delays, and lost revenue. But fear not! This insightful article will dive deep into various industries’ most pervasive culprits behind machine failures. So, fasten your seatbelts for this journey to equip yourselves with practical knowledge on preventing machine malfunctions!
What is machinery failure?
Machinery failures occur when a piece of equipment, machinery, or mechanical system ceases to function as intended due to various factors. These factors can be technical, electrical, operational, or environmental. Machinery failures can disrupt normal operations, leading to downtime, decreased productivity, increased maintenance costs, and potentially even safety hazards.
Machine failure can manifest in different forms, ranging from minor malfunctions to complete breakdowns. Identifying and addressing the root causes of machinery failure is crucial for industries and businesses relying heavily on equipment to maintain operations. Proper maintenance, regular inspections, and implementation of preventive measures are essential to minimize the occurrence of machinery failures and their associated negative impacts.
Common causes of machine failures
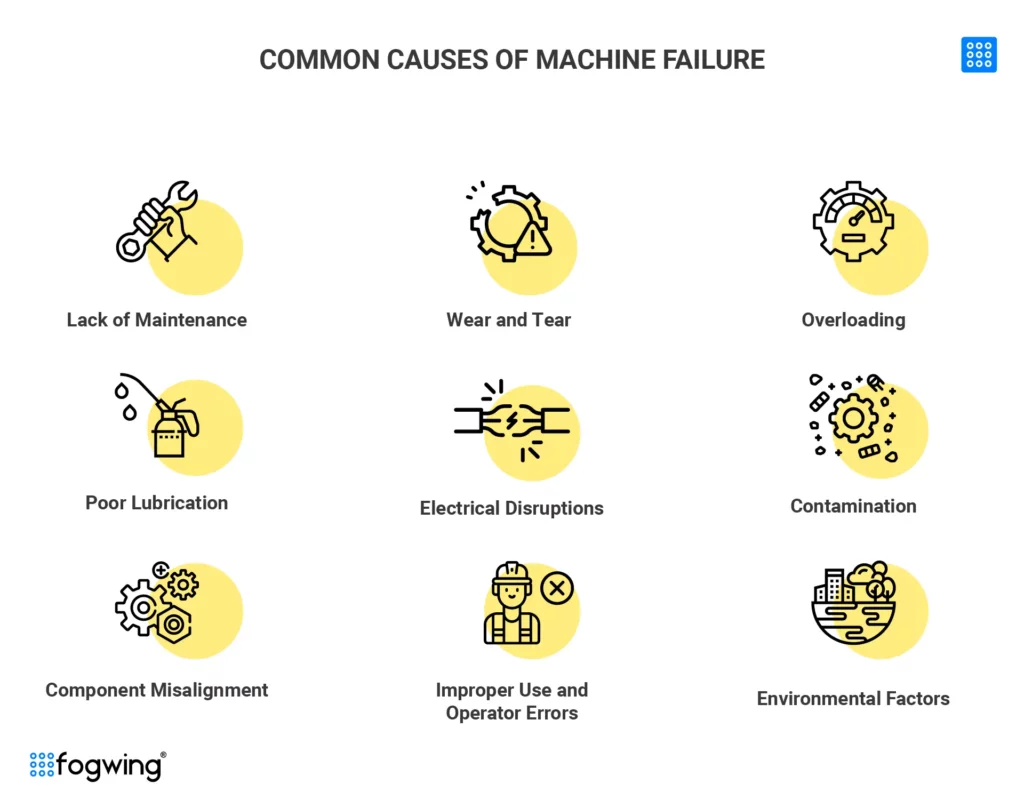
The common causes of machine failure can vary depending on the type of equipment, industry, and operational conditions. However, some general factors that often contribute to machine failures include:
Lack of Maintenance
Inadequate or irregular maintenance can lead to worn-out components, decreased lubrication, and increased chances of failure over time.
Wear and Tear
Continuous operation and friction can lead to gradual wear and tear of machine components, reducing their efficiency and lifespan.
Overloading
Exceeding a machine’s designed capacity can stress its components excessively, leading to premature failure.
Poor Lubrication
Insufficient or improper lubrication can result in friction, heat buildup, and increased wear and tear on moving parts.
Electrical Disruptions
Electrical problems such as short circuits, power fluctuations, or faulty connections can disrupt the functioning of machines and their components.
Contamination
Dust, debris, moisture, and other contaminants can infiltrate machinery, causing machine breakdown and malfunctions.
Component Misalignment
Misaligned components can lead to friction, wear, and parts malfunction, contributing to overall machine failure.
Fatigue Failure
Repeated cyclic loading and unloading of components can lead to fatigue failure, especially in high-stress areas of machinery.
Improper Use and Operator Errors
Incorrect operation, misuse, or lack of proper training for operators can lead to unintended stress on machines and their components.
Environmental Factors
Extreme temperatures, humidity, vibrations, and other environmental conditions can contribute to the wear and failure of machinery. For example, exposure to moisture and corrosive environments can lead to corrosion and rust.
Understanding these common causes of machine failure is essential for implementing preventive measures, regular maintenance, and proper operational practices to ensure the reliability and longevity of equipment.
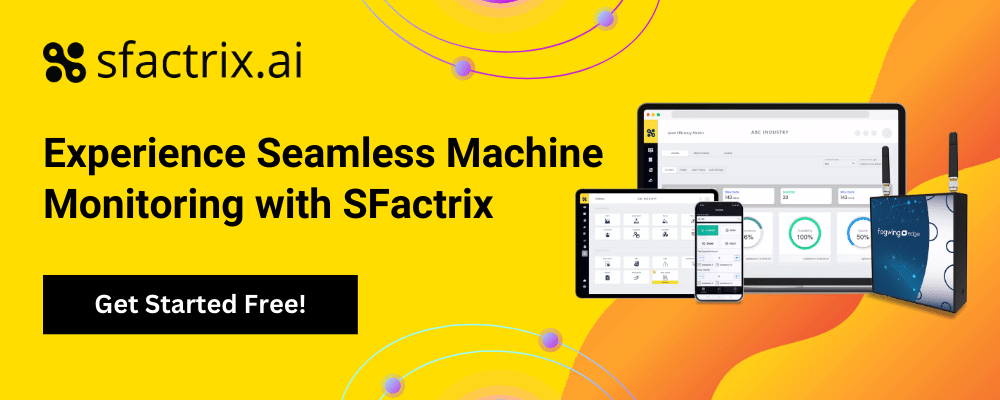
What are the effects of machine failure?
Machinery failures can significantly impact operations, productivity, and overall business performance. Here are some of the critical impacts of machine failure:
Downtime and Reduced Productivity: Machine failures often lead to unplanned downtime, causing production stoppages and reduced output. It directly affects productivity levels and can disrupt the supply chain and delivery schedules.
Increased Operating Costs: Repairing or replacing failed machinery is costly, especially if it involves emergency maintenance or expedited part orders. Additional expenses may also arise from overtime pay for maintenance staff and loss of revenue due to halted production.
Missed Deadlines: Production delays resulting from machine failure can lead to missed delivery deadlines, contractual obligations, and customer commitments. This can impact relationships with clients and harm the company’s reputation.
Higher Maintenance Costs: If the manufacturers do not address the machine failures promptly, they can escalate into more complex issues, requiring extensive repairs or replacements. Delayed maintenance leads to higher costs and longer downtime.
Quality Issues: Machines in failure or malfunction can produce defective products or subpar-quality items. It affects customer satisfaction and may necessitate rework or disposal of faulty products.
Safety Risks: Some machine failures can pose safety hazards to employees and the working environment. Malfunctioning equipment can lead to accidents, injuries, and potential legal liabilities.
Supply Chain Disruptions: Machine failure can affect downstream processes and disrupt the supply chain, leading to delays and inventory shortages.
Resource Waste: When machines fail, the materials, energy, and labor invested in the production process can go to waste. This inefficient resource utilization negatively impacts overall operational efficiency.
Decreased Employee Morale: Frequent machinery failures and disruptions create a stressful work environment for employees. The uncertainty caused by unreliable equipment can reduce morale and job satisfaction.
Financial Losses: The combined impact of machine downtime, decreased productivity, increased maintenance costs, and potential reputational damage results in significant financial losses for the business.
Customer Dissatisfaction: Delays in product delivery, quality issues, and unmet commitments due to machine failures can lead to customer dissatisfaction and harm the company’s brand image.
How To Reduce or Prevent Machine Failures
Reducing or preventing factory machine failure is essential for maintaining productivity, minimizing machine downtime, and ensuring the safety of workers. Here are some strategies and best practices to help you achieve this:
Real-Time Monitoring
With the help of sensors and IoT technology, machine performance can be monitored in real-time. It enables immediate detection of anomalies and deviations from normal operating conditions. These sensors continuously collect data on various parameters such as temperature, vibration, pressure, fluid levels, etc.
Remote Monitoring
Embrace the power of IoT that enables remote monitoring solutions. This approach allows factories to monitor their machines’ health and performance from anywhere, facilitating timely intervention continuously. Remote monitoring is particularly valuable for industries with critical and complex machinery, such as manufacturing, energy production, and transportation.
Predictive Maintenance
Predictive maintenance is an advanced maintenance strategy that uses data, sensors, and analytics to predict when a machine or equipment will likely fail. It allows maintenance to be performed just in time to prevent machine failure. Predictive maintenance aims to maximize the uptime and reliability of machinery while minimizing downtime and reducing unnecessary maintenance costs. Utilize data analytics and historical information to predict when machines are likely to fail. This approach allows for proactive maintenance before issues escalate.
Condition-Based Alerts
Implement automated alert systems that notify maintenance teams when specific conditions, such as temperature or vibration levels, exceed predetermined thresholds. With condition-based monitoring, the maintenance strategy is tailored to the particular condition of each machine. For example, a machine in excellent condition may not require maintenance as frequently as one showing signs of wear and tear. This approach maximizes the use of resources and minimizes unnecessary maintenance tasks.
Data Analysis for Insights
Regularly monitor and analyze data to uncover trends, patterns, and potential correlations to reduce machine failure to a large extent. By analyzing the data collected from sensors and other sources, organizations can gain valuable insights into the condition and performance of their machines. This data-driven approach enhances understanding of machine behavior and aids in preventive actions that include detecting anomalies, predicting potential failures, and making informed maintenance and operational improvement decisions.
To learn more about manufacturing data analytics, read this blog. Data Analytics In Manufacturing – The Essentials | Fogwing.io
Historical Data Analysis
By examining historical data, factories can identify recurring issues, assess the effectiveness of past maintenance efforts, and pinpoint the root causes of previous failures. This data allows for proactive maintenance strategies and helps predict potential failure points. By addressing these issues before they escalate, maintenance teams can reduce unplanned downtime, optimize resource allocation, extend machine lifespan, and enhance overall operational efficiency (OOE). Historical data analysis empowers businesses to learn from the past and take data-driven actions to prevent future machine failure occurrences, saving time and resources.
Troubleshooting Techniques for identifying wear and tear in Machine
Troubleshooting techniques for identifying machine wear and tear are essential for maintaining equipment and preventing costly failures. Here are five troubleshooting techniques to help identify wear and tear.
Vibration Analysis
Utilize vibration sensors to detect abnormal levels of vibration in machine components. Increased vibration can indicate misalignment, imbalance, or worn-out parts.
Thermal Imaging
Employ infrared cameras to visualize heat patterns on machine surfaces. Hot spots may suggest friction, excessive load, or deteriorating components.
Visual Inspection
Conduct regular visual inspections to look for signs of wear, such as rust, corrosion, cracks, or worn-out seals. It can reveal issues like leaks or material degradation.
Noise Analysis
Monitor the unusual sounds during machine operation. Clanking, grinding, or squeaking noises could signal friction, loose parts, or imminent machine failure.
Performance Monitoring
Continuously track performance metrics like speed, output, and efficiency. Declining performance over time can indicate wear and tear in components.
Types of Machine Breakdown and Their Unique Failures
Machine breakdowns can manifest in various ways, each associated with unique failures and causes. Understanding these types of breakdowns is essential for effective maintenance and troubleshooting. Here are common types of machine breakdowns and their notable shortcomings:
Abrupt / Sudden Failures:
Abrupt breakdowns occur often without any warning. Machine failure may result from component fatigue, material defects, or overloading in this context. Unique issues include sudden fractures in critical components, electrical shorts, or catastrophic system failures. For instance, a conveyor belt snapping due to wear and tear can halt production abruptly.
Gradual Failures:
Gradual failures develop slowly over time due to wear and tear, corrosion, or material degradation. Distinctive problems encompass worn-out bearings, deteriorating seals, declining motor efficiency, or gradually decreasing machine performance. For instance, an industrial pump may experience reduced flow rates and efficiency due to gradual wear in its impeller.
Intermittent Failures:
Intermittent breakdowns are irregular and unpredictable, caused by factors like loose connections, temperature variations, or electrical interference. These issues manifest as sporadic malfunctions, erratic sensor readings, or transient faults in electrical circuits. A classic example is flickering lights caused by loose electrical connections.
Operator-Induced Failures:
Operator-induced machine failure results from human error, misuse, or negligence. It encompasses issues like incorrect settings, overloading, or accidental damage due to operator mishandling or inadequate maintenance. For instance, an operator incorrectly setting the temperature on an industrial oven can lead to product defects.
Environmental Failures
Environmental breakdowns stem from exposure to harsh conditions, such as extreme temperatures, humidity, or contaminants. Unique failures include corrosion, rust, electrical shorts due to moisture, or clogged filters. An example is the corrosion of outdoor metal equipment due to exposure to salty air in coastal environments.
Prevent Machine Failure with SFactrix Machine Monitoring
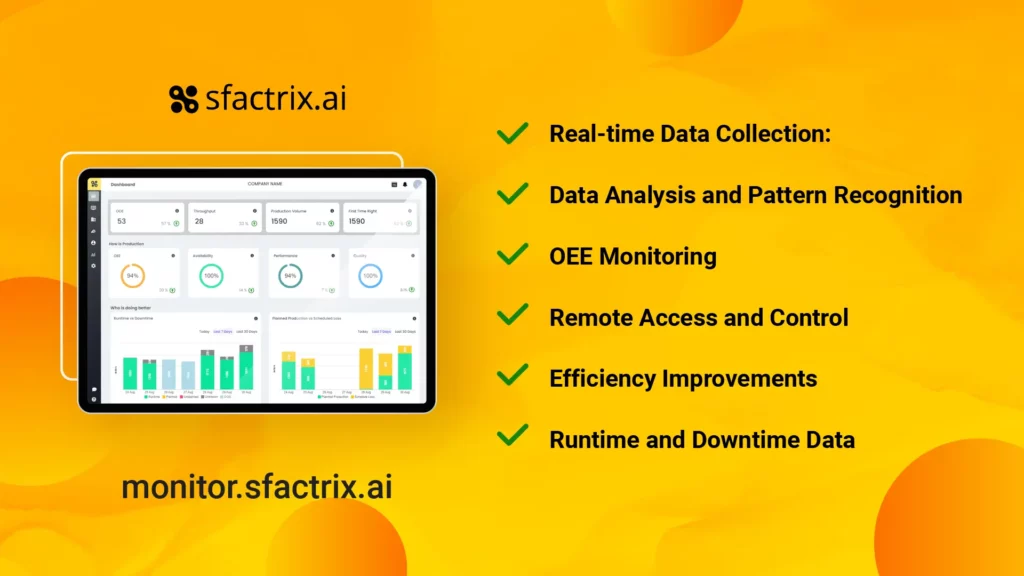
SFactrix machine monitoring solution enables factories and manufacturers to connect their machines to the software via IoT connectivity and monitor end-to-end data from machines. SFactrix, integrated with IoT, a robust manufacturing intelligence module, provides a comprehensive suite of features to visualize your machine data, including performance, efficiency, availability, runtime, downtime, and more on the dashboard. SFactrix machine monitoring solutions typically prevent machine failures through the following mechanisms:
Real-time Data Collection
SFactrix machine monitoring system continuously collects data from sensors placed on or near the machines.
Data Analysis and Pattern Recognition:
The collected data is analyzed through machine learning techniques to identify standard operating patterns and deviations. Anomalies in data can indicate potential issues.
OEE Monitoring
SFactrix machine monitoring offers OEE monitoring that helps prevent machine failure by providing real-time and historical data on machine performance, allowing organizations to detect issues early, schedule maintenance proactively, and optimize their equipment.
Remote Access and Control
SFactrix provides remote access to machine data and control, enabling experts to monitor and troubleshoot machines from off-site locations.
Efficiency Improvements
SFactrix Machine monitoring can lead to energy savings and improved operational efficiency by optimizing machine operation.
Runtime and Downtime Data
Runtime and downtime data can significantly aid in preventing machine breakdowns and improving overall equipment reliability. By leveraging this, manufacturers can identify the underlying reasons for the machine failure, enabling corrective actions to prevent recurrence.
To learn more about how to visualize your factory machines’ data, read this blog Visual Factory: A Comprehensive Introduction | Fogwing.io
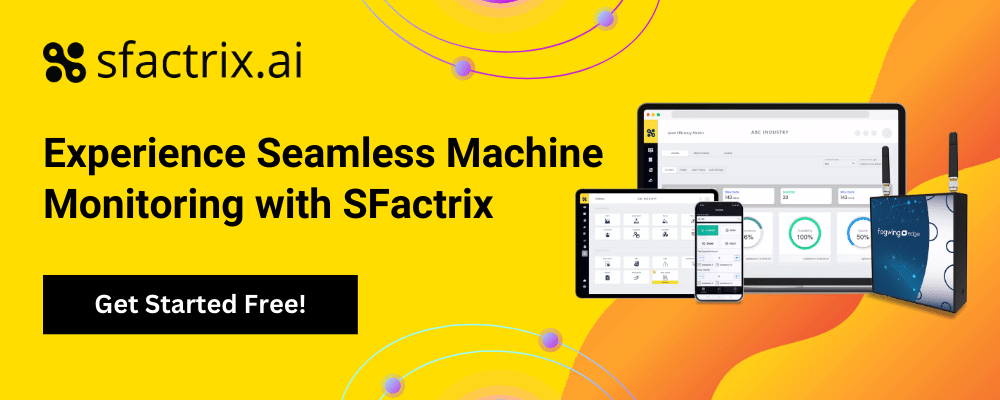
Conclusion
Understanding the nuances of machine failure is crucial for maintaining operational efficiency and productivity. Tailoring machine monitoring practices to address the possible or specific failure modes helps ensure machinery’s reliability and longevity. By taking a preventative approach, you can reduce the risk of costly downtime and ensure optimal performance throughout your facility.