The quest for operational excellence is relentless in today’s fiercely competitive business landscape. Organizations of all sizes constantly seek ways to streamline processes, enhance productivity, and efficiently deliver high-quality products and services. In this pursuit, one indispensable metric has emerged as a beacon of guidance: Overall Operations Effectiveness. In this comprehensive guide, we will broadly explain key concepts of OOE, explore its paramount importance in business operations, discuss its implementation’s myriad benefits, and outline the essential steps to integrate OOE seamlessly into your business setting.
What is OOE?
OOE, or Overall Operations Effectiveness, is a performance metric that comprehensively measures the efficiency and effectiveness of a manufacturing or production process. It provides a holistic view of a specific operation, production line, or entire facility’s performance, encompassing every aspect from the initial stages to the final output.
At its core, Overall Operations Effectiveness quantifies how much an organization’s resources—such as time, labor, materials, and equipment—are optimally utilized to deliver high-quality products or services. It offers a complete picture of individual metrics by assessing multiple facets of an operation, allowing decision-makers to identify improvement and strategic enhancement areas.
OOE, like OEE (Overall Equipment Efficiency), assesses and improves efficiency within a manufacturing or production environment. They help organizations identify improvement areas for increased efficiency and competitiveness.
Overall Operations Effectiveness is a comprehensive metric that evaluates a manufacturing operation’s overall efficiency and effectiveness, considering three key components: Availability, Performance, and Quality.
These three pillars— Availability, Performance, and Quality—are interrelated and mutually reinforced within the framework of Overall Operations Effectiveness. Together, they provide a comprehensive assessment of an operation’s overall performance. Fogwing machine monitoring solution simplifies these three Overall Operations Effectiveness metrics parameters with an automated dashboard visualization.
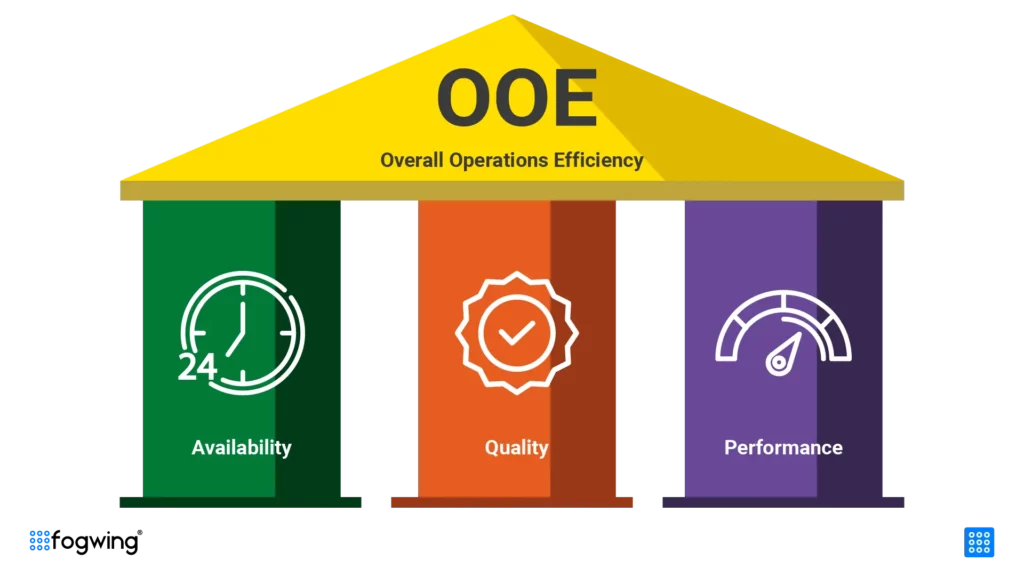
Efficiency vs. Effectiveness
Efficiency and effectiveness are two fundamental concepts that underpin Overall Operations Effectiveness:
Efficiency refers to how effectively resources, such as time, materials, and labor, are utilized in production. It involves minimizing waste and optimizing processes to achieve maximum output with minimal input.
Effectiveness, on the other hand, focuses on achieving the desired results or outcomes. In the context of OOE, effectiveness pertains to the ability of a business to meet its goals and deliver products or services that satisfy customer expectations.
Measuring Overall Operations Effectiveness requires striking a balance between these two concepts. It’s not just about doing things efficiently but also ensuring that those efficient processes yield effective results.
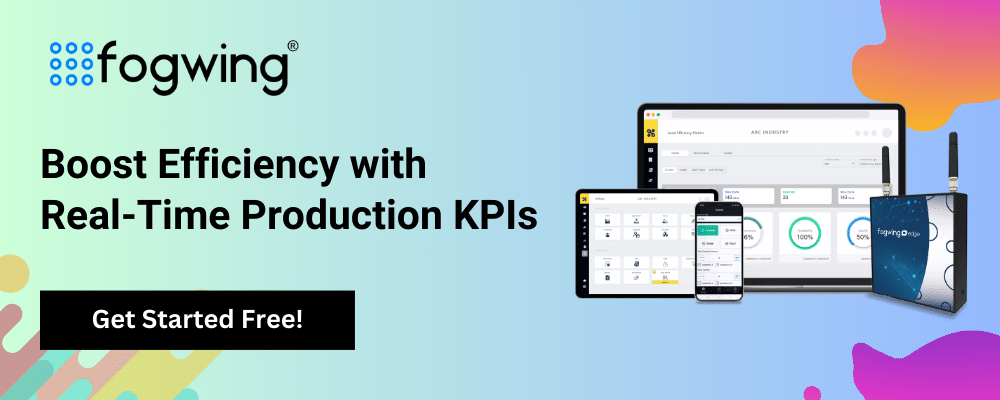
How to Measure OOE?
Measuring OOE is a systematic process involving collecting, analyzing, and interpreting data to derive a quantifiable metric. While the exact formula used to calculate OOE can be tailored to specific business needs, the fundamental components of both OOE and OEE typically include the following:
Availability: Availability refers to the actual time an operation is available for production. It is often measured as a percentage, with higher values indicating more uptime and availability. The formula for availability is:
Availability (%) = (Operating Time / Uptime) x 100
Performance: Performance assesses how well an operation performs compared to its maximum potential. It considers factors such as machine speed, cycle times, and stoppages. The formula for performance is:
Performance (%) = (Actual Production / Ideal Production) x 100
Quality: Quality evaluates the rate of production that meets pre-defined quality standards. It accounts for defects, rework, and scrap. The quality formula is:
Quality (%) = (Good Units Produced / Total Units Started) x 100
Overall Operations Effectiveness: It is the ultimate metric integrating availability, performance, and quality into a single value, offering a comprehensive view of operational effectiveness. The formula for OOE is:
OOE (%) = Performance (%) x Quality x (%) Availability (%) (Here, Availability is the actual production time/uptime)
Whereas in the OEE Calculation Formula,
OEE (%) = Performance (%) x Quality x (%) Availability (%) (Here, Availability is the scheduled production time).
To explore OEE in detail, read this 5 Ways To Improve OEE In Manufacturing Operations | Fogwing.io
By calculating OOE using these components, businesses obtain a clear and concise metric that represents the overall performance of their operations. This metric serves as a valuable benchmark for tracking progress and identifying areas for improvement. It makes the manufacturer’s life simple when they have automated OOE measurement data through Fogwing machine monitoring solution to help excel their operational efficiency.
Benefits of Implementing OOE in Business Operations
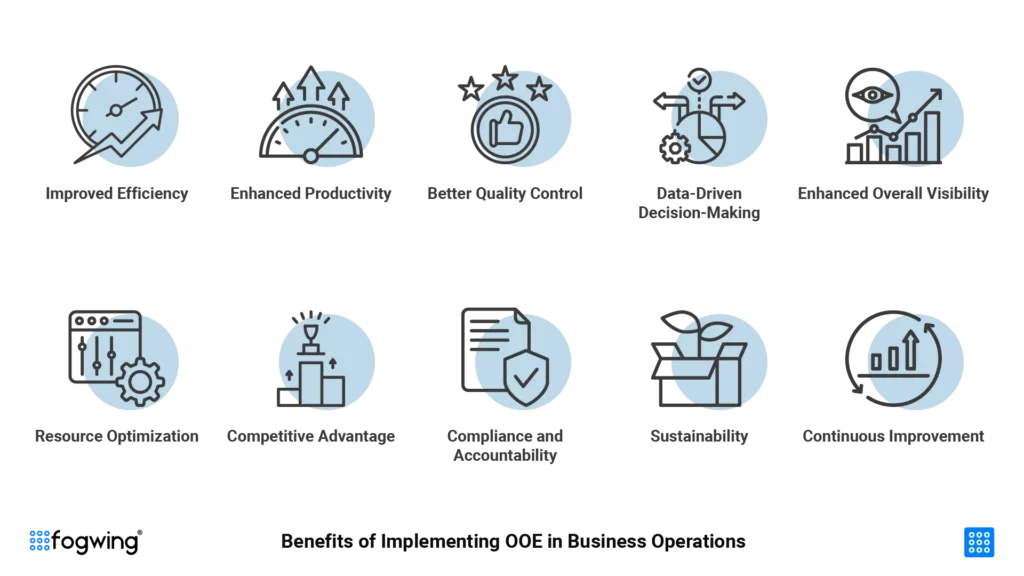
Implementing Overall Operations Effectiveness in manufacturing operations offers many advantages across various business aspects. Let’s delve into the key benefits of adopting Overall Operations Effectiveness:
Improved Efficiency: It enables organizations to identify bottlenecks, eliminate wasteful processes, and streamline workflows. Doing so drives operational efficiency, reduces resource wastage, and optimizes resource allocation.
Enhanced Productivity: Productivity gains are a direct outcome of OOE implementation. By optimizing processes and ensuring the efficient use of resources, it empowers businesses to produce more output with the same or fewer inputs.
Better Quality Control: Quality is paramount in today’s competitive marketplace. OOE strongly emphasizes quality control, helping manufacturing industries reduce defects, improve product consistency, and enhance customer satisfaction.
Data-Driven Decision-Making: OOE relies on real-time data collection and analysis. This wealth of data empowers decision-makers with valuable insights into operations, enabling data-driven decision-making. By making informed choices, businesses can respond promptly to changes in demand or market conditions.
Enhanced Overall Visibility: OOE provides a comprehensive view of the entire production process. This enhanced visibility enables businesses to figure out potential issues before they escalate, leading to more proactive problem-solving.
Resource Optimization: With a focus on efficiency and productivity, OOE assists businesses in optimizing resource utilization. This results in cost savings, reduced operational expenses, and improved profitability.
Competitive Advantage: Businesses that embrace OOE gain a significant competitive advantage. They are better equipped to respond to market fluctuations, deliver consistent, high-quality products or services, and outperform competitors.
Compliance and Accountability: It helps businesses meet regulatory compliance standards by ensuring processes adhere to defined specifications and guidelines. This accountability is essential in industries with strict regulatory requirements.
Sustainability: By minimizing resource wastage and optimizing processes, It contributes to sustainability efforts. It reduces a business’s environmental footprint and aligns with corporate social responsibility initiatives.
Continuous Improvement: OOE fosters a culture of continuous improvement within an organization. Businesses remain agile and responsive to evolving market conditions by regularly analyzing data and identifying areas for enhancement.
Implementing OOE is not just about improving one aspect of operations; it’s a holistic approach that enhances efficiency, productivity, and quality while delivering numerous benefits across the entire organization.
Real-Time Examples of Successful Implementation of OOE
To illustrate the practical application of OOE and its transformative impact on organizations, let’s explore a few real-time examples:
Example 1: Automotive Manufacturing
A prominent automotive manufacturer sought to enhance the efficiency of its production line. By implementing OOE principles, the company identified and rectified bottlenecks in the assembly process, reduced downtime due to equipment failures, and optimized worker performance. As a result, the production line’s OOE increased by 20%, substantially reducing production costs and significantly improving product quality.
Example 2: Pharmaceutical Production
A pharmaceutical company aimed to improve the quality control of its drug manufacturing process. By implementing OOE monitoring, the company could track and analyze the entire production cycle in real-time. Any deviations from quality standards were promptly identified and addressed, reducing the rate of product recalls and enhancing patient safety. This proactive approach safeguarded the company’s reputation and resulted in cost savings associated with quality assurance.
Example 3: Food Processing Industry
A food processing facility faced challenges regarding efficient resource use and consistent product quality. Through OOE implementation, the company optimized its production lines, minimized waste, and ensured the uniformity of its food products. The OOE-driven improvements led to a 15% increase in production output and a corresponding reduction in operational costs, ultimately bolstering the company’s market competitiveness.
The above examples demonstrate that OOE is not a theoretical concept but a practical and effective tool for enhancing operational performance, reducing costs, and enhancing the quality of products or services. Explore Fogwing Machine Monitoring Solution for a highly effective OOE application designed to serve every industry requirement.
Challenges and Solutions in Adopting OOE
While OOE offers many benefits, its successful adoption has its challenges. Businesses may encounter the following obstacles while implementing it:
Resistance to Change: Employees may resist changes to existing processes and workflows. To address this, businesses should communicate the benefits of OOE, involve employees in the transition, and provide training and support.
Data Integration: Integrating data from various sources, such as production equipment, sensors, and software systems, can be complex. Implementing a robust data integration strategy and using compatible technologies can mitigate this challenge.
Initial Investment: There may be initial costs associated with OOE implementation, including hardware, software, and training expenses. However, the long-term benefits typically outweigh these upfront investments.
Data Security: Overall Operations Effectiveness relies heavily on data collection and analysis, ensuring data security and compliance with data protection regulations is crucial. Organizations should implement robust security measures and adhere to data privacy standards.
Employee Training: Effective Overall Operations Effectiveness implementation requires employees to understand and embrace the new methodologies. Businesses must invest in training programs to upskill their workforce and ensure proficiency in OOE concepts and tools.
Fogwing Machine Monitoring solution is devoid of all these challenges as its Overall Operations Effectiveness application is highly automated. No training special training is required to implement this cost-effective solution.
How Fogwing Improves OOE
Fogwing machine monitoring is an IoT (Internet of Things) based solution that offers a range of features to improve Overall Operations Effectiveness in manufacturing. Fogwing machine monitoring allows manufacturers to collect real-time data through sensors to monitor the various parameters of production operations. It plays a crucial role in monitoring Overall Operations Effectiveness by providing real-time visibility into multiple aspects of the manufacturing process. Here’s how Fogwing can enhance Overall Operations Effectiveness.
Data Collection: Production monitoring software collects data from various sources within the manufacturing environment, such as sensors, machines, PLCs (Programmable Logic Controllers), and other equipment. This data includes information on machine status, production rates, quality measurements, and more.
Real-time Monitoring: The software continuously monitors the data in real time, providing a live view of the production floor. This real-time monitoring allows operators and managers to quickly identify issues impacting Overall Operations Effectiveness, such as machine breakdowns, bottlenecks, or quality deviations.
Key Performance Indicators (KPIs): Production monitoring software tracks and calculates key performance indicators related to Availability, Performance, and Quality, the three components of Overall Operations Effectiveness. Such as,
- Availability: It tracks machine uptime and downtime, including reasons for downtime (e.g., maintenance, changeovers, breakdowns).
- Performance: It monitors production rates and efficiency, highlighting speed losses, idling, or minor stoppages.
- Quality: It tracks quality metrics, detecting defects, scrap, and rework.
Visualization and Dashboards: Fogwing presents this data in a highly comprehensive and user-friendly dashboard.

Historical Data Analysis: Fogwing machine monitoring solution stores historical data, enabling organizations to analyze trends and patterns in OOE metrics over time. This analysis can help in identifying recurring issues and planning for improvements.
Continuous Improvement: Fogwing supports ongoing improvement initiatives by providing actionable insights. Manufacturers can use the data to optimize processes, reduce downtime, improve quality, and enhance overall operational efficiency.
By leveraging Fogwing’s highly automated and cost-effective OOE capabilities, businesses can streamline operations, reduce downtime, improve product quality, and optimize resource utilization. This ultimately leads to a significant enhancement in Overall Operations Effectiveness. It offers a comprehensive approach to measuring, optimizing, and continuously improving business operations’ efficiency, productivity, and quality.
Read this to learn more about how Fogwing machine monitoring helps manufacturers in master production monitoring 5 Why Analysis For Production Monitoring | Fogwing.io
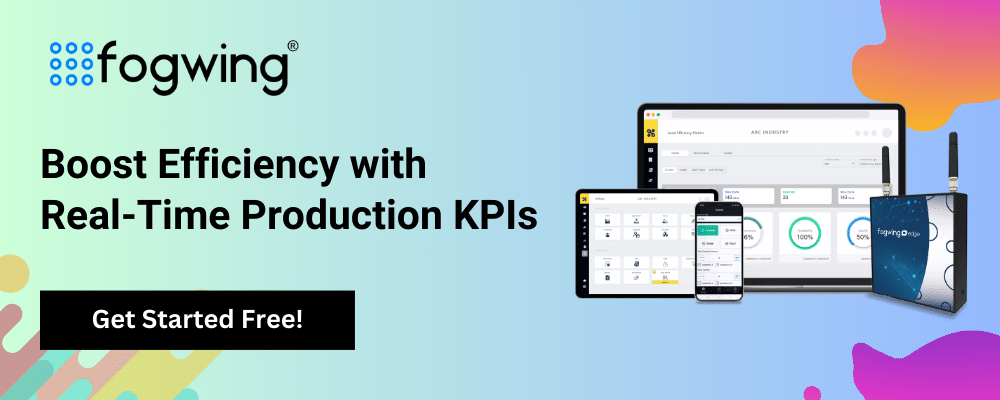
Conclusion: Unlocking the Potential of OOE in Business Operations
In this blog, we’ve explored the definition and significance of Overall Operations Effectiveness, delved into key concepts of it, and highlighted the numerous benefits of OOE implementation, from cost savings to enhanced customer satisfaction.
Additionally, we’ve outlined the essential steps for seamlessly integrating Overall Operations Effectiveness into your business setting, emphasizing the importance of data-driven decision-making, continuous improvement, and fostering a culture of OOE throughout your organization.
In a world where efficiency and effectiveness are paramount, Overall Operations Effectiveness serves as a catalyst for achieving business success. By understanding what is Overall Operations Effectiveness and embracing its holistic approach to performance measurement and improvement, organizations can unlock their full operational potential, ensuring that their processes are efficient, productive, and capable of delivering high-quality products or services. In doing so, they position themselves for sustained growth, profitability, and competitiveness in an ever-changing business landscape. OOE is not just a concept; it is a catalyst for success.