Maintaining optimal equipment performance is vital for the smooth running of any organization. Imagine you are in the middle of a busy workday, relying entirely on your equipment, and suddenly everything comes to a grinding halt; your machine breaks down, pausing your production tasks. The culprit? Neglected maintenance.
Whether it’s a computer glitch or an unexpected breakdown, we’ve lost productivity due to failing of equipment at a crucial point. It’s why considering Periodic maintenance is not just an option – it’s an absolute must-do for anyone looking to keep their machine or assets running smoothly to avoid dreaded movements of downtime, ensuring longevity, efficiency, and safety by systematically inspecting, repairing, and fine-tuning machinery.
This blog delves into the significance of periodic maintenance service, exploring how this proactive approach prevents unexpected breakdowns and enhances your assets’ overall productivity. It is essential for organizations to regularly upkeep the maintenance process to have a consistent, reliable performance of the equipment.
What is Periodic Maintenance?
Periodic maintenance is the regularly scheduled process of inspecting, cleaning, lubricating, adjusting, and upkeeping equipment to prevent breakdowns and extend lifespan and is performed at predetermined intervals, such as every month, every quarter, or every year.
The frequency of maintenance will differ based on the equipment type, environment, and utilization. This proactive approach involves routine inspection, servicing, and adjustments to ensure equipment remains in optimal working condition.
This practice is commonly followed in various industries, including manufacturing, energy, transportation, and more, to reduce the likelihood of significant repairs, extend the asset lifespan, minimize the disruption caused by equipment failures, and maintain its efficiency and reliability over time.
During periodic maintenance, the organization follows a schedule of regular tasks. Here’s a detailed breakdown of the processes describing the importance of periodic maintenance :
- Scheduled Inspections: Maintenance technicians in organizations inspect the assets thoroughly during each maintenance interval. They look for wear, damage, or deterioration in various components. It enables them to identify potential issues before it escalates into significant ones.
- Cleaning and Lubrication: In organizations, cleaning is essential, as dirt and debris can impact equipment performance. When assigned the maintenance task, the maintenance technician cleans components, removes buildup, and ensures that parts are properly lubricated to reduce friction and wear in the equipment.
- Parts Replacements: With time, certain equipment parts may degrade or wear out in an organization. During periodic maintenance, technicians replace these parts as needed. It includes elements like filters, belts, seals, and other consumables.
- Calibration and Adjustment: Some assets in an organization require precise calibration to function effectively. Technicians check and adjust settings to ensure equipment operates within the specified parameters in periodic maintenance service.
- Performance check: After completing the maintenance tasks, technicians often conduct performance tests to ensure that equipment operates as expected. It might involve using the equipment under different circumstances and conditions to verify its functionality.
- Documentation: Every organization maintains proper documentation of each maintenance session conducted on an asset in an organization. It includes the details on tasks performed, any issues identified, issues addressed, parts replaced, and maintenance date. This record enables the organizations to track the equipment’s maintenance history.
- Predictive Analysis: With the help of advanced technologies, predictive analysis enhances some of the periodic maintenance practices. Sensors attached to the equipment collect real-time data, and data analytics can provide insights into the equipment’s condition, allowing the maintenance team to precisely perform maintenance when needed based on actual usage and wear.
Routine maintenance is a proactive strategy to maximize assets’ operational life while minimizing downtime and unexpected failures. It’s an essential practice for industries that rely on machinery and equipment to ensure consistence performance, safety, and efficiency.
Examples of Periodic Maintenance
Periodic maintenance emerges as one of the efficient maintenance practices. Each asset demands timely attention, from crucial HVAC systems that regulate comfort to intricate machinery pushing industries forward. Here are some examples of periodic maintenance tasks that organizations commonly perform on various types of equipment and technique:
HVAC Systems (Heating, Ventilating, and Air Conditioning)
An organization’s heating ventilating, and air conditions need regular maintenance to perform efficiently. Periodically changing air filters helps organizations maintain clean air quality and prevents strains on the system.
Annually cleaning coils and condensers ensures optimal heat exchange and energy efficiency. Inspecting and lubricating fan motors and belts semi-annually prevents friction and prolongs their lifespan, promoting a cost-effective indoor environment with routine maintenance.
Automobile
Automobile industries utilize periodic maintenance as it is essential for its safety and longevity. Changing engine oil and filtering every predefined mile prevents engines wear and ensures smooth operations.
Regularly rotating tires and checking pressures improves fuel efficiency and enhances traction. As the manufacturer recommends, the air filters and spark plug replacement enable the organizations to maintain engine performance and fuel economy.
Manufacturing Machinery
Effective maintenance of manufacturing equipment maximizes productivity. Regularly lubricating moving parts prevents friction-related issues and extends the lifespan of the components.
Calibrating sensors and instruments quarterly with periodic maintenance service ensures accurate maintenance quality control. Regularly checking belts, chains, and bearings for wear and tear prevents costly downtime and production interruptions.
Fire Safety System
Proper fire safety system maintenance is essential for building safety. Here is where periodic maintenance comes to play. Testing fire alarms and sprinkler system every quarter ensure safety and functionality during emergencies.
Replacement of batteries in the smoke detector annually ensures the reliability of their operations. Comprehensive system checks annually identify any issues, ensuring that fire safety remains operational and practical.
What are the Different Types of Periodic Maintenance?
Periodic maintenance service strategies ensure the proper functioning and longevity of various systems, equipment, and infrastructure. Here’s a breakdown of the three types of maintenance that are conducted in the organization periodically.
Schedule-Based Maintenance
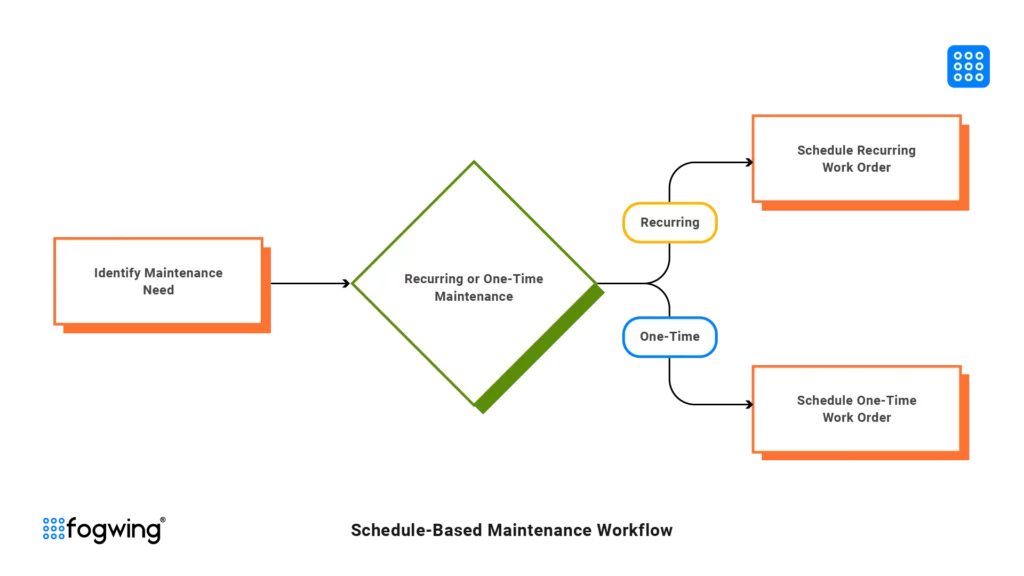
This type of maintenance follows and maintains a predetermined schedule. The assets are serviced, inspected, or replaced regularly, regardless of their current condition, based on historical data, manufacturer recommendations, or industrial standards associated with the assets.
Scheduled-based routine maintenance helps the organization’s equipment to remain in good working conditions by preventing unexpected breakdowns or downtime. However, Scheduled maintenance can also lead to over-maintenance if performed too frequently or can also miss the issues if performed too infrequently.
Condition-Based Maintenance
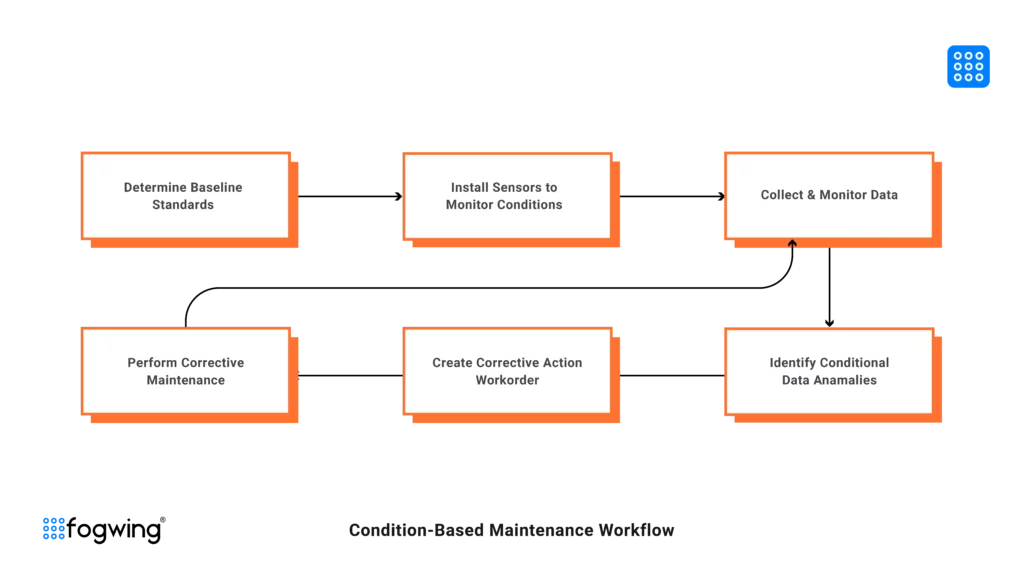
Condition-based maintenance relies on real-time data and asset monitoring to assess the current condition of an organization’s assets.
In condition-based periodic maintenance, sensors and monitoring devices attached to the devices gather the data like temperature, vibration, fluid level, and many more, based on which the maintenance managers perform the maintenance activities. This approach minimizes downtime and optimizes maintenance efforts by addressing problems immediately.
Prediction-Based Maintenance
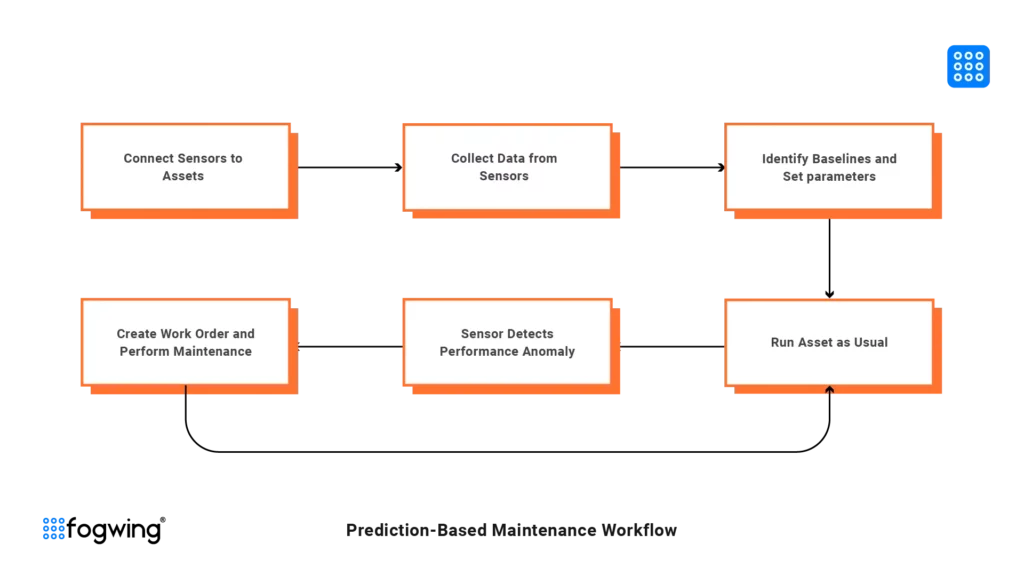
Prediction-based maintenance takes condition-based periodic maintenance service a step further. It involves advanced analytics, machine learning, and artificial intelligence to predict when maintenance is required.
The predictive algorithm can forecast when assets are likely to fail by analyzing historical data, current conditions, and other factors. It helps organizations to conduct even more precise planning of routine maintenance activities, reducing disruption and increasing equipment uptime.
Each type of Periodic Maintenance has advantages and disadvantages, and choosing which approach to utilize often depends on factors such as the criticality of the equipment, resource availability, budget constraints, and the potential consequences of failures.
In recent times with the advancement in technologies like sensors, data analytics, and machine learning, there has been a growing trend toward adopting more condition-based and prediction-based maintenance strategies due to their potential for optimizing maintenance efforts and cost reduction.
Benefits of Periodic Maintenance Service
Prolonged Asset Lifespan
Regular maintenance is a preventive measure against premature asset failures. Maintaining your assets can help them last longer, avoid pricey repairs, and save you funds in the long run. Regularly maintaining and servicing your assets can help you identify potential problems early on. Handling minor issues before they escalate into notable failures endures less stress and wear over time, which results in prolonged operational lifespans, saving organizations from substantial costs associated with frequent replacements. Moreover, extended asset life contributes to sustainable practices by minimizing the environmental impact of manufacturing and disposal of new equipment by investing in periodic maintenance. It also enables the business to make the most of its capital investments and reduces its carbon footprint.
Minimized Downtime
One of the most significant advantages of routine maintenance is its ability to reduce unplanned downtime. When assets fail without warning, all the operations associated with that asset halt, leading to lost productivity, missed deadlines, and dissatisfied customers. Regular maintenance enables organizations to proactively identify and address potential issues, preventing breakdowns before they occur. It also enhances overall productivity and customer satisfaction. Moreover, reduced downtime translates to tangible financial savings, as companies avoid the cost associated with emergency repairs, rushed shipments, and overtime wages for maintenance personnel.
Enhanced Operational Efficiency
Assets that undergo regular maintenance are optimized for organizational efficiency. This optimization ensures consistent performance and reduces energy consumption and wastage of resources. The periodic maintenance enables the fine-tuning of the assets to operate at their best, requiring less energy to perform tasks, leading to lower utility bills and reduced environmental footprints. Additionally, organizations influence sustainable practices by minimizing wastage of resources and aligning with modern expectations for responsible resource management. The collective effect of enhanced operations leads to long-term cost savings and a positive public image.
Predictable budgeting
Periodic maintenance service enables organizations to effectively plan and allocate resources by anticipating maintenance costs based on regular schedules, allowing the business to give budget more accurately. This predictability prevents financial surprises caused by sudden breakdowns or emergency repairs that can strain you financially. Predictable budgeting promotes monetary stability and facilitates long-term planning and investment decisions. With periodic maintenance, organizations can confidently allocate funds for maintenance activities. Ensuring that the necessary resources are available when required. This strategic approach to budgeting enables organizations to maintain their operations without excessive financial strains.
Enhanced Safety
Periodic maintenance service not just ensures optimal equipment performance but also enhances safety in the workplace. Manufacturing equipment usually poses significant risks to personnel, potentially leading to accidents, injuries, and even fatalities. By conducting routine inspections and maintenance, businesses can create a safer environment for employees, contractors, and visitors. A safe workforce boosts employee morale, reducing absenteeism due to injuries and preventing costly legal liabilities resulting from negligence. Investing in safety through periodic maintenance is a proactive measure that protects human lives and safeguards a company’s reputation and financial stability.
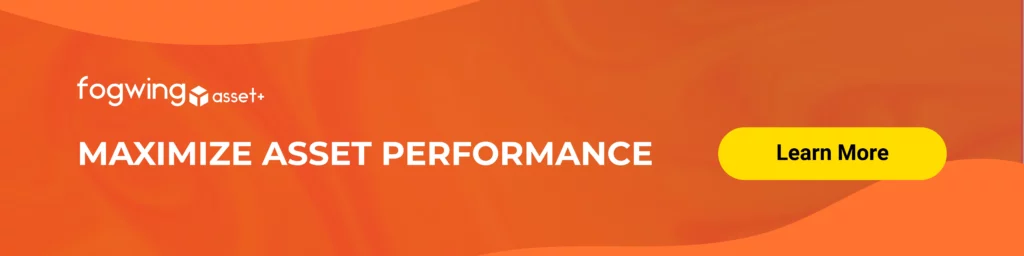
How Does Fogwing CMMS Makes Life Easier?
Regular maintenance is critical in keeping assets running smoothly, but keeping track of every maintenance task can be daunting. It’s where a computerized maintenance management system (CMMS) can be a lifesaver. A good CMMS makes the tracking and scheduling of the maintenance services and helps organizations run smoothly, and prevents costly repairs down the roads.
An advanced CMMS platform like the Fogwing Asset+ platform simplifies your life by offering a centralized location for maintenance-related activities and information. It helps organizations schedule maintenance tasks, track parts inventory, and generate reports to help them identify trends.
Here are a few points on how Fogwing CMMS makes life easier:
Maintenance Scheduling: Fogwing Asset+ platform understands the importance of Periodic maintenance and allows organizations to schedule periodic maintenance tasks based on predefined intervals. By seamlessly integrating the understanding that regular upkeep is the cornerstone of sustained asset performance, this platform empowers organizations to plan maintenance strategies meticulously based on predefined intervals.
The platform seamlessly integrates the arrangement of work order schedules, functioning as a digital conductor. Daily, weekly, monthly, or yearly maintenance routines can be laced into the maintenance operations effortlessly using the Fogwing Asset+ platform. It also provides the means for maintenance managers to define the frequency of maintenance activities with finesse. With periodic maintenance, Fogwing Asset+ ensures that each step taken is a stride toward preventing disruptions and extending the lifespan of invaluable assets.
Centralized Asset data: Smart Asset management solutions like Fogwing Asset+ provide a centralized repository for storing and managing asset-related information. It includes equipment, machinery, systems, and maintenance history details. The maintenance managers and technicians can remotely access the asset maintenance-related data like part inventory information, supplier information, scheduled maintenance work order, maintenance technicians, advanced Open AI GPT powered maintenance checklist, and many more.
With all this data at your fingertip, it’s now more accessible for organizations to schedule, manage, and conduct periodic maintenance with Fogwing Asset+, an intelligent CMMS A Platform. You can now track and organize all your regular maintenance in one place. It means no more missed appointments or scrambling to find the proper paperwork. Our system also makes it easy to generate reports to see how the organization’s assets perform.
Automated Work Orders: Th Fogwing Asset+ automates the creation of Asset maintenance work orders with the help of a fully-fledged IoT-integrated Fogwing Asset+ CMMS solution. It ensures that maintenance activities are organized and assigned efficiently based on the mentioned threshold meter value and rules.
A work order will be generated when the IoT meter value meets the defined regulations or requirements. The Fogwing IoT metering feature simplifies the Periodic maintenance services. Asset management platforms may integrate with sensors and IOT devices to monitor the condition of assets in real time. It enables organizations to identify issues requiring attention between scheduled maintenance intervals.
Conclusion
In conclusion, periodic maintenance is indispensable for sustaining seamless operations, preventing unexpected breakdowns, and extending asset lifespan. It safeguards organizations against the disruptive vision of asset failures that can bring productivity to a grinding halt. This blog has taken you on a journey through the world of periodic maintenance, highlighting its pivotal role in enhancing asset productivity and longevity.
To Simplify the adaptation of periodic maintenance, a reliable partner is required, and the Fogwing Asset+ Platform can add simplicity to this complex process, ensuring meticulous maintenance scheduling and centralized data. It empowers organizations to schedule periodic maintenance tasks with precision, integrating seamlessly into the rhythm of operations. In essence, routine maintenance service isn’t just a practice but a strategic approach ensuring asset performance and longevity. With the support of advanced platforms like Fogwing Asset+, the journey toward optimized asset management becomes more accessible, efficient, reliable, and ultimately more successful.
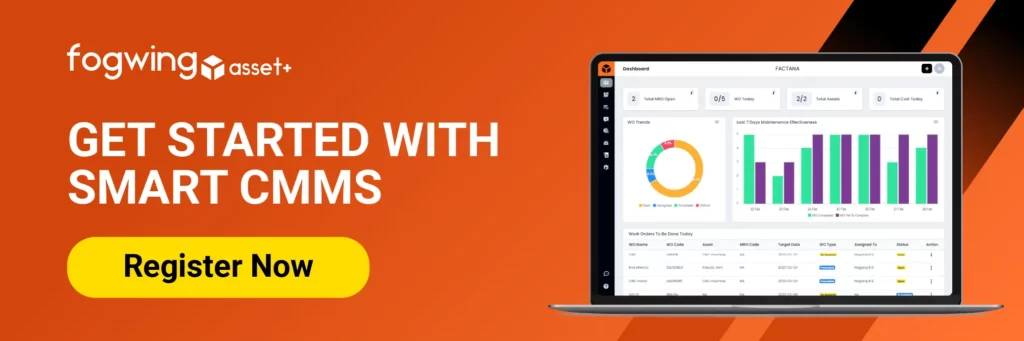