Are you aware of the saying “prevention is better than cure”? Well, the same principle applies to maintaining a manufacturing plant. Like your body needs regular check-ups and maintenance to function at its best, so does your industrial plant. Plant maintenance is not just about fixing things when they break; it’s about proactively ensuring everything runs smoothly, efficiently, and safely.
In this blog post, we will introduce you to the world of plant maintenance – what it entails, why it’s crucial for the organization operating a manufacturing facility, and how you can implement an effective maintenance system in your plant. And discover how effectively it can transform your business operations from good to great !
What is Plant Maintenance?
Plant maintenance refers to the regular and systematic inspection, repair, and upkeep of equipment, machinery, and infrastructure in a manufacturing plant or industrial facility. It involves a proactive approach, like regular inspections, repairing, and maintaining different components to ensure all parts function optimally to avoid unexpected downtime or expensive breakdowns.
Plant Maintenance includes preventive, predictive, corrective, emergency, and condition monitoring maintenance.
In simple terms, manufacturing plant maintenance is like taking your car for regular check-ups and tune-ups to avoid unexpected breakdowns on the road. Just like how you change the oil regularly or replace worn-out parts in your vehicle, it ensures that all assets in a production facility work smoothly.
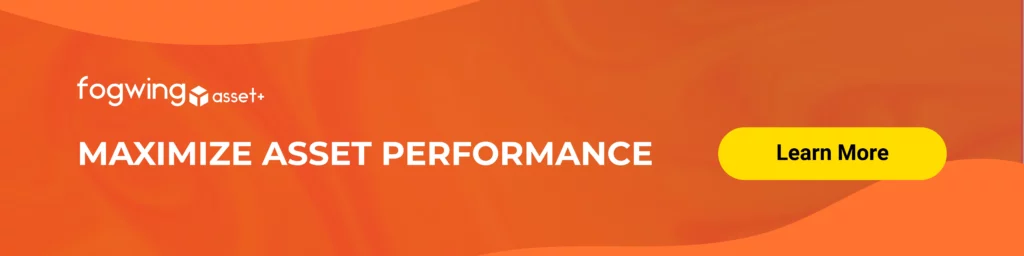
Types of Plant Maintenance Operations
Plant maintenance encompasses many activities essential to keep the industrial plant in working condition. There are different types of plant maintenance, each serving a specific purpose in ensuring the optimal functioning and longevity of equipment and machinery :
1. Preventive Plant Maintenance
Preventive maintenance is a crucial aspect of manufacturing plant maintenance. It focuses on preventing breakdowns by conducting routine inspections, lubrications, cleaning, and replacing parts before they break or crash.
These regular activities help identify potential issues early on, minimize unplanned downtime, and extend the lifespan of critical assets by scheduling maintenance tasks daily, monthly, yearly, or based on asset requirements.
By standing ahead of maintenance requirements, manufacturers can conserve time, money, and resources in the long run. Additionally, a Computerized Maintenance Management System (CMMS) can streamline the scheduling process by automating reminders and generating work orders.
2. Predictive Plant Maintenance
Predictive maintenance is a foresighted manner types of plant maintenance that predicts when equipment failures are likely to happen with the help of machine monitoring techniques and data analysis, predictive maintenance can identify early indicators of potential asset-related issues, allowing for timely intervention and preventive measures.
Preventive maintenance minimizes unplanned downtime by analyzing historical data and patterns of the assets. It pinpoints the optimal time for asset servicing or replacements and prevents unexpected breakdowns that could disrupt production schedules.
3. Corrective Plant Maintenance
Corrective maintenance is an essential aspect of manufacturing plant maintenance that focuses on fixing or repairing assets after malfunctioning or breakdown.
Corrective maintenance occurs when an unexpected asset failure emerges to restore the functionality and performance of the affected components. It involves reactive repairs or part replacements with minimal disruption to the production process.
In this types of plant maintenance activity, maintenance technicians thoroughly analyze the root cause of the problem and determine the best course of action to rectify it. It might involve replacing faulty parts, repairing damaged components, or even redesigning certain elements to prevent future issues.
4. Condition Based Maintenance
Condition monitoring is a crucial types of plant maintenance that continuously monitors equipment and systems to identify potential issues or asset failures. This collected data helps organizations detect early signs of malfunctioning before they escalate into major problems.
It prevents unexpected asset breakdowns and costly downtime by monitoring variables such as temperature, vibration, pressure, and fluid level in real-time.
Visual inspection, non-destructive testing, thermal imaging, acoustic emission analysis, and oil analysis are techniques employed in Condition monitoring to identify abnormal patterns or deviations from normal operating conditions.
5. Breakdown Maintenance
When it comes to the maintenance of industrial plants, emergencies can arise unexpectedly. And these emergencies need immediate attention and action to prevent further damage or disruptions in the production process.
The primary goal of emergency maintenance in plant maintenance is to assess the issue and implement an effective solution quickly. Emergency maintenance may involve temporarily shutting down certain assets or systems to address the problems.
While conducting emergency maintenance, plant managers and technicians must have clear protocols to ensure everyone knows their roles and responsibilities, enabling them to respond swiftly and efficiently.
Each types of plant maintenance is significant in maintaining operational efficiency within manufacturing plants; however, implementing a combination explicitly tailored to your facility’s needs may yield the best results.
Best Practices of Industrial Plant Maintenance
Implementing the best practices in an advanced plant maintenance system ensures your equipment’s optimal functioning and longevity. Here are a few vital best practices that can help you maximize efficiency and minimize downtime.
Regular Inspections:
Regular inspections of your organization’s assets enable you to identify any potential issues or indications of wear and tear before they escalate into significant problems. This proactive approach allows you to schedule necessary repairs and maintenance on time, preventing costly breakdowns and production delays in organizations.
Prioritize preventive maintenance:
By following a comprehensive maintenance schedule that includes tasks such as lubrication, calcination, cleaning, and components/Parts replacements at predetermined intervals, you can extend the lifespan of your equipment while reducing unexpected failures of organizational assets.
Invest in employee training:
A well-trained workforce is critical for effective plant maintenance. Ensure your employees receive proper training on operating procedures and essential troubleshooting techniques to actively contribute to identifying early signs of malfunctioning and taste appropriate actions.
Incorporating these best practices into your maintenance strategy will enhance productivity and preserve time and money by reducing unplanned downtime and unnecessary plant repair and maintenance. Remember that each facility or organization that needs asset maintenance might have unique requirements; thus, adapting these practices to suit your needs will yield the best results.
Benefits of Plant Maintenance
Increase Equipment Reliability:
Organization asset maintenance ensures that all the machinery and assets are inspected, serviced regularly, and repaired when needed. The maintenance team can prevent unexpected breakdowns and costly downtime by proactively addressing potential issues. With increased reliability, the production process operates efficiently, meeting the production targets and reducing the reactive repairs, which can be time-consuming and disrupt the operation.
Enhanced Safety:
A well-maintained plant is a safer place for maintenance workers and is one of the significant benefits of plant maintenance. Regular maintenance practices promptly identify and address safety hazards, lowering the risk of accidents and injuries.
For example, exposed wiring or malfunctioning safety mechanisms of faulty assets in organizations can be detected during manufacturing plant maintenance and repair, reducing the risk of accidents and injuries. Prioritizing safety throughout the maintenance process creates a workspace where the employees feel safe and secure, improving morale and productivity.
Cost Saving:
Planned maintenance offers significant cost benefits for a plant by conducting routine inspections and preventing maintenance, reducing the likelihood of substantial breakdowns and emergency repairs, which reduces the need for costly replacements and rush orders for repair and maintenance—moreover, plant maintenance results in lower energy consumption and reduced operational costs.
Extended Asset Lifespan:
Regular servicing and well-maintained assets prevent assets’ premature wear and tear, resulting in increased asset lifespan. Addressing minor asset issues early on helps an organization control the problems from escalating into more significant and costly failures. This prolonged lifespan increases the return on investment for assets and positively impacts the plant’s financial health.
Compliance and Quality Assurance:
Compliance with industrial regulations and quality standards is vital for any organization’s success. Best plant maintenance ensures that the assets meet the regulatory requirements and obey the quality assurance programs. Regular inspections and maintenance help organizations identify potential non-compliance issues early, allowing prompt corrective actions.
Following compliance and quality assurance enhances the organization’s reputation and develops customer confidence.
In summary, plant maintenance is a vital practice that provides numerous benefits for factories and facilities in maintenance. It promotes smooth operations, ensures workspace safety, minimizes costs, prolongs asset lifespan, and helps maintain quality standards. Best plant maintenance managers can optimize efficiency, productivity, and profitability in the long run by investing in proper maintenance strategies.
What is Plant Maintenance Program
A plant maintenance program is a structured plan designed to ensure the smooth operation, reliability, and longevity of equipment and systems within a facility. It includes strategies, tasks, and schedules to proactively manage and maintain assets, minimizing downtime and repair costs.
Key benefits of a robust plant maintenance program include:
- Improved Equipment Reliability: Regular inspections and preventive maintenance reduce the risk of unexpected breakdowns.
- Cost Savings: Proactive maintenance prevents costly repairs and extends the lifespan of assets.
- Operational Efficiency: Well-maintained equipment operates at peak performance, ensuring smooth workflows.
- Enhanced Safety: Adhering to maintenance schedules minimizes risks and ensures a safe working environment.
- Regulatory Compliance: Detailed maintenance records help meet industry standards and legal requirements.
By implementing a plant maintenance program, organizations can foster a culture of efficiency, reliability, and sustainability, paving the way for long-term success.
Role of CMMS in Plant Maintenance
Computerized Maintenance Management Systems (CMMS) play a pivotal role in modern plant maintenance, streamlining operations, improving equipment reliability, and enhancing overall productivity. Here’s how CMMS impacts plant maintenance processes:
1. Centralized Maintenance Data Management
CMMS serves as a centralized hub for storing all maintenance-related data, including equipment details, maintenance schedules, work orders, and historical records. This centralized repository ensures easy access to critical information, enabling maintenance teams to make data-driven decisions.
2. Streamlined Work Order Management
Managing work orders manually can lead to inefficiencies, delays, and errors. CMMS automates the work order lifecycle, from creation and assignment to tracking and closure. Maintenance managers can prioritize tasks, allocate resources effectively, and monitor progress in real-time, ensuring no maintenance activity is overlooked.
3. Proactive Preventive Maintenance
With CMMS, organizations can shift from reactive to preventive maintenance. By scheduling routine inspections and maintenance activities based on usage data or time intervals, CMMS helps prevent unexpected equipment failures, reducing downtime and repair costs.
4. Real-Time Asset Tracking
A robust CMMS integrates with IoT devices and sensors, enabling real-time asset condition monitoring. Maintenance teams can track key performance indicators (KPIs) such as temperature, vibration, and pressure to detect anomalies early and take corrective action before minor issues escalate into major problems.
5. Enhanced Compliance and Reporting
Many industries require adherence to strict regulatory standards for safety and environmental impact. CMMS simplifies compliance by maintaining detailed records of maintenance activities, inspections, and certifications. Automated reporting tools ensure that plants meet regulatory requirements with ease.
6. Cost Optimization
Unplanned maintenance can be costly due to emergency repairs and downtime. CMMS helps optimize costs by providing insights into maintenance trends, resource utilization, and asset lifecycle management. Predictive analytics powered by CMMS can forecast maintenance needs, enabling better budgeting and resource allocation.
7. Improved Communication and Collaboration
Effective maintenance requires seamless communication between teams. CMMS facilitates collaboration by providing a unified platform where technicians, managers, and stakeholders can share updates, report issues, and track work progress in real-time.
8. Extended Equipment Lifespan
By ensuring timely and consistent maintenance, CMMS helps extend the operational lifespan of plant assets. Well-maintained equipment operates more efficiently, reducing energy consumption and wear and tear.
Fogwing CMMS for Plant Maintenance
Fogwing CMMS is a comprehensive solution designed to revolutionize plant maintenance operations. With advanced features tailored to industrial needs, Fogwing CMMS empowers maintenance teams to achieve efficiency, reliability, and cost savings. Here’s how Fogwing CMMS supports plant maintenance:
- Centralized Data Management: Provides a unified platform to manage maintenance schedules, work orders, asset history, and compliance records.
- Preventive Maintenance Scheduling: Automates maintenance schedules based on usage or time, reducing unplanned downtime and extending asset life.
- IoT-Driven Asset Monitoring: Integrates with IoT sensors for real-time condition monitoring, enabling predictive maintenance and early fault detection.
- Seamless Work Order Management: Simplifies task assignment, tracking, and completion to enhance workflow efficiency.
- Enhanced Reporting and Compliance: Offers automated reporting tools to meet regulatory standards and maintain audit-ready documentation.
- Cost Optimization: Leverages AI-powered analytics to identify maintenance trends and optimize resource allocation, minimizing operational expenses.
- User-Friendly Interface: Designed for ease of use, ensuring quick adoption and effective communication among team members.
- Scalable and Customizable: Adapts to the unique needs of your plant, growing with your operations and integrating seamlessly with existing systems.
With Fogwing CMMS, plant maintenance transforms into a proactive, data-driven process, ensuring peak operational performance and long-term success.
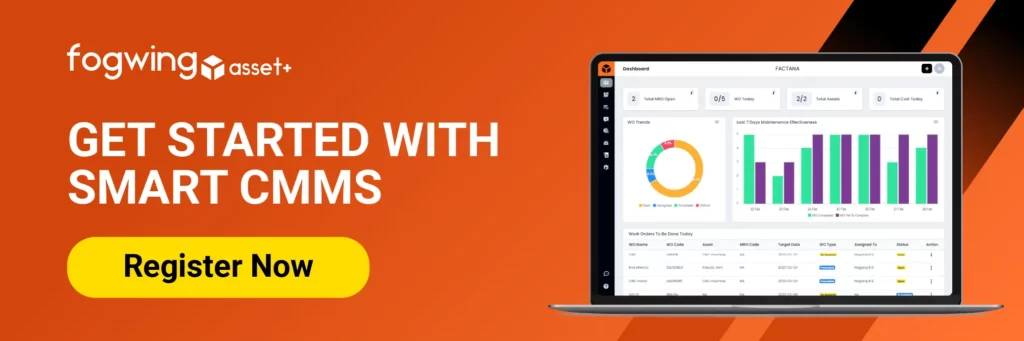
Conclusion
Any manufacturing facility needs the best plant maintenance service to ensure equipment and machinery’s smooth operation and longevity. By implementing the comprehensive maintenance service, manufacturers can minimize downtime, increase productivity, and reduce repair and replacement costs.
Effective industrial plant maintenance service enhances safety and improves product quality and customer satisfaction by prioritizing regular inspection and proactive strategies to identify potential issues before they become critical problems. Manufacturers can ensure uninterrupted operations while prolonging the lifespan of their valuable assets.