In today’s rapidly evolving industrial landscape, achieving manufacturing excellence has become a continuous and dynamic endeavor. Central to this pursuit is the strategic optimization of machine efficiency – a critical factor that directly influences productivity, cost-effectiveness, and overall operational success. When seamlessly integrated with lean manufacturing principles, machine efficiency becomes a formidable catalyst for revolutionizing operations and propelling businesses toward unparalleled achievements. This comprehensive exploration delves deep into the intricate relationship between machines’ efficiency and lean processes, unveiling how they synergistically coalesce to streamline operations, reduce wastage, and elevate the overarching performance paradigm.
The Foundation of Machine Efficiency:
If you want your machines to operate at peak efficiency, it’s essential to ensure they have a strong foundation. It means having a well-designed layout, a preventive maintenance program, and an operator training plan.
A well-designed layout is the first step to ensuring machine efficiency. The form should be designed so materials can flow smoothly and operators can move quickly from one task to another. Preventive maintenance is also critical to keeping machines running efficiently. A good preventative maintenance program will identify potential problems before they occur and correct them before they cause downtime. Operator training is essential to maximize the efficiency of each machine. Operators should be appropriately trained to use the machine and its controls and perform basic maintenance tasks.
The above steps help you create a strong foundation in your lean operation. Investing in these areas ensures your machines run at their best, contributing to your overall success.
Understanding Lean Manufacturing:
In the realm of operational excellence, the principles of lean manufacturing stand as a beacon of systematic refinement. Eliminating waste, enhancing process efficiencies, and creating tangible value for customers, lean manufacturing embodies a holistic approach that seeks to eliminate non-value-added activities, trim excesses in inventory, and drastically reduce downtime. At its core, lean manufacturing orchestrates a harmonious and streamlined production flow, agilely responding to shifting customer demands flexibly and precisely.
How Real-Time monitoring improve Machine Efficiency?
To understand how real-time monitoring elevates machine efficiency in Lean operations, it is first necessary to understand what Lean operations are. Lean operations are defined as a method of manufacturing that relies on a continuous flow of work to minimize waste and unnecessary steps. The goal of Lean is to increase value for the customer while using fewer resources.
One of the fundamental principles of Lean is the identification and elimination of waste. Many types of waste can occur in manufacturing processes. Still, they can be broadly classified into defects and variations. Defects are errors or mistakes that result in a product that does not meet the customer’s requirements. Variation is any deviation from the ideal manufacturing process, including excessive cycle times, downtime, or material waste.
Continuous improvement is essential to Lean operations, and real-time monitoring can play a significant role in this by providing data that identifies areas where improvements can be made. For example, if cycle times are too long, adjusting the process to reduce them may be possible. Or if there is a high material waste rate, changes could be made to reduce or eliminate it. By constantly looking for ways to improve efficiency, Lean operations can create more value for the customer while using fewer resources.
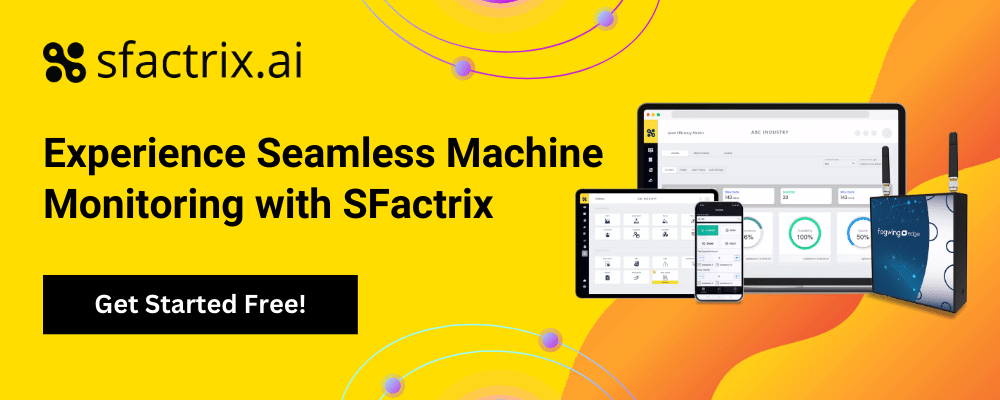
How to calculate the efficiency of a machine?
Efficiency of a machine is a crucial metric that indicates how well a machine performs in converting input resources (such as energy, time, or raw materials) into desired output (production, products, or services). Calculating the efficiency of a machine involves measuring the actual output achieved by the machine and comparing it to the potential or ideal production under optimal conditions.
The machine efficiency formula is as follows:
Machine Efficiency(%) = (Actual Output / Potential Output) x 100
Here’s a breakdown of the components and steps involved in the above calculation.
Actual output refers to the machine’s product or service during a specific period which can be calculated in terms of units, quantity, weight, volume, or any relevant unit of measurement.
Potential output, or Ideal Output, represents the maximum output the machine can achieve under perfect or ideal conditions. It is often determined based on the machine’s design specifications, production capacity, and operating parameters.
Calculation: To calculate machine efficiency, divide the actual output by the potential production and multiply by 100 to derive the result as a percentage.
Machine Efficiency(%) = (Actual Output / Potential Output) x 100
It’s important to note that machines’ efficiency calculations can vary based on the specific industry, process, and context. Additionally, other factors such as downtime, idle time, and maintenance activities can impact the accuracy of the calculation. Additional metrics such as uptime, availability, and utilization may also be considered to obtain more accurate and comprehensive insights into machine performance.
Furthermore, calculations can be further refined by considering various losses, such as:
Idle Time
Time during which the machine is not in operation but should be.
Downtime
Time during which the machine is non-operational due to planned or unplanned maintenance, repairs, or other reasons.
Setup Time
Time required for setting up the machine for a new production run.
Speed Losses
Slowdowns or reduced speed of the machine due to various factors.
Quality Losses
Time spent on rework or scrap due to defects in the output.
What is the Significance of Efficient Machines?
Machine efficiency is of paramount importance in modern manufacturing and industrial processes for several compelling reasons:
- Cost Savings: Efficient machines reduce resource consumption, lowering operational costs.
- Productivity: High efficiency leads to increased output within the same timeframe.
- Competitive Edge: Cost-efficient production allows competitive pricing and market advantage.
- Resource Conservation: Lower energy use and waste align with sustainability goals.
- Quality: Efficient machines produce fewer defects and higher quality output.
- Equipment Lifespan: Well-maintained machines last longer, reducing maintenance and replacements.
- Lean Principles: Efficient machines support waste reduction and improvement in lean manufacturing.
- Safety: Fewer breakdowns enhance workplace safety and morale.
- Strategic Insights: Efficiency data informs decisions, like capacity planning and innovation.
What 3 ways is Machine Efficiency achieved?
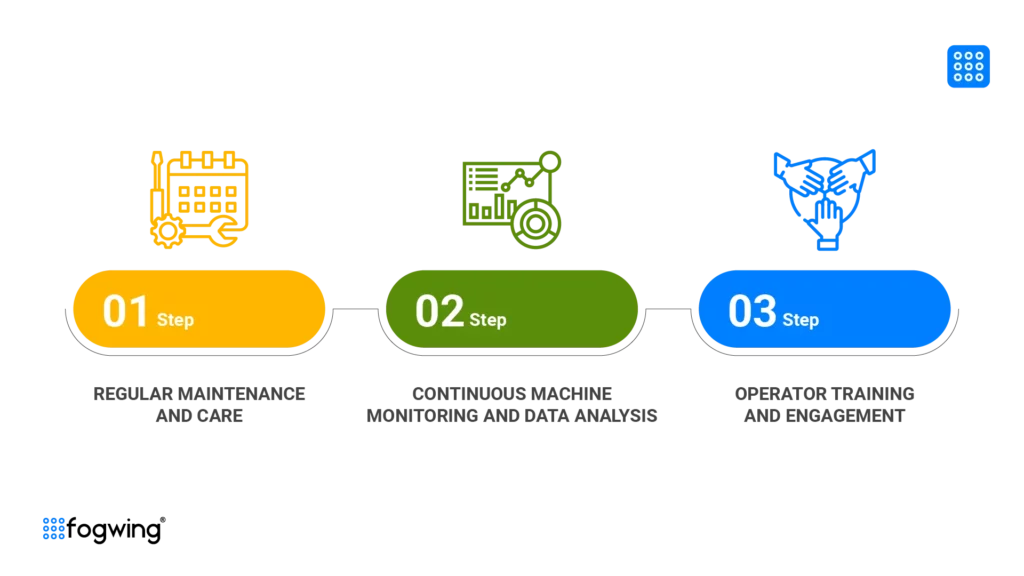
It can be achieved through strategies and practices that optimize machine operation, maintenance, and utilization. Here are three key ways to achieve the highest efficiency of a machine:
Regular Maintenance and Care:
Proper and regular maintenance is essential for optimizing machine health. It includes preventive maintenance routines, timely repairs, and calibration to ensure that machines operate at peak performance levels. By addressing issues before they escalate and maintaining optimal working conditions, machines are less likely to experience downtime or breakdowns, increasing overall efficiency.
Continuous Machine Monitoring and Data Analysis:
Implementing real-time monitoring systems and data analytics allows for collecting and analyzing machine performance metrics. Manufacturers can identify inefficiencies, patterns, and potential issues by closely monitoring energy consumption, cycle times, throughput, and error rates. This data-driven approach enables decision-making for process improvements and adjustments that enhance machine efficiency.
Operator Training and Engagement:
Well-trained operators who understand machine functions and operational best practices are crucial in achieving machine or equipment efficiency. Comprehensive training ensures operators can operate machines optimally, troubleshoot minor issues, and perform routine maintenance tasks. Additionally, fostering a culture of employee engagement and ownership encourages operators to take pride in machine performance, leading to greater attentiveness and care.
These three strategies work together to create a holistic approach to achieving machine efficiency. Regular maintenance, data-driven insights, and skilled operators contribute to a well-rounded system that maximizes the output, minimizes downtime, and optimizes resource utilization, ultimately leading to enhanced machine efficiency.
Strategies for Integrating Machine Efficiency & Lean Manufacturing
There are several ways to integrate the two aspects. One way is to use machines that are specifically designed for lean manufacturing. These machines are typically more efficient and faster than traditional machines, and they can help to reduce waste and improve quality. Another way to integrate is to implement lean principles throughout the organization. This means training all employees in lean principles, designing Lean workflows, and measuring progress using Lean metrics. It is essential to improve machine efficiency and lean manufacturing practices continuously. This can be done by analyzing data, experimenting with new ideas, and constantly striving for improvement.
Finally, technology can be used to facilitate the integration of machine or equipment efficiency and Lean operations. Automation can reduce waste and increase accuracy. In contrast, artificial intelligence (AI) can help to analyze data and identify areas for improvement.
How SFactrix Machine Monitoring helps in achieving Machine Efficiency?
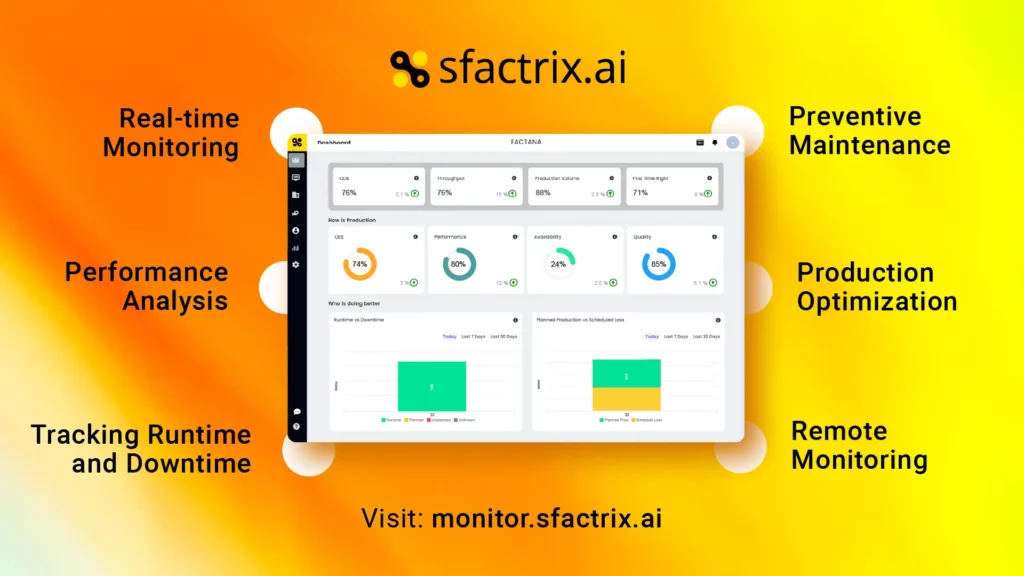
SFactrix machine monitoring software enables manufacturers to connect their machines to the software via IoT connectivity and monitor various production and machine metrics and key performance indicators (KPIs). Users can monitor the real-time data of their machines and make the right moves and actions to improve the machine’s overall operability. SFactrix machine monitoring is loaded with advanced features which help in enhancing efficiency of a machine. A few are listed below.
Real-time monitoring
SFactrix provides real-time data on machine performance, allowing operators to closely monitor key metrics such as machine uptime, downtime, and production rates. This real-time visibility helps identify any issues or bottlenecks affecting machine efficiency.
Performance analysis
SFactrix collects and analyzes data on machine parameters such as operating temperature, speed, and power consumption. By analyzing this data, operators can identify patterns or trends that can help optimize machine performance and improve efficiency.
Runtime and Downtime tracking
SFactrix tracks runtime and downtime events and provides detailed information on the total planned production or quality production as per the machine runtime. It also provides the reasons for downtime, including equipment failures, changeovers, and maintenance activities. By understanding the causes of downtime, operators can take proactive measures to reduce and eliminate these issues, improving the overall efficiency of machines.
Preventive maintenance
SFactrix leverages machine learning algorithms to predict potential equipment failures or downtime and alerts the operators. By identifying signs of impending failures, operators can schedule preventive maintenance activities, avoiding unplanned downtime and minimizing disruptions to production. This proactive approach results in efficient machines by maximizing uptime and reducing unnecessary maintenance costs.
Production optimization with OEE monitoring
SFactrix provides insights into production rates and overall equipment effectiveness (OEE) metrics such as availability, performance, and quality. By analyzing these metrics, operators can identify opportunities for process improvement, optimize production schedules, and enhance overall machine efficiency.
Remote monitoring
SFactrix enables remote monitoring and control of machines, allowing operators to access real-time data and make necessary adjustments from anywhere. This capability improves decision-making, reduces issue response times, and increases overall machine efficiency.
By leveraging SFactrix machine monitoring, manufacturers can gain valuable insights into machine performance, optimize operations, and achieve higher efficiency levels, leading to increased productivity and reduced costs.
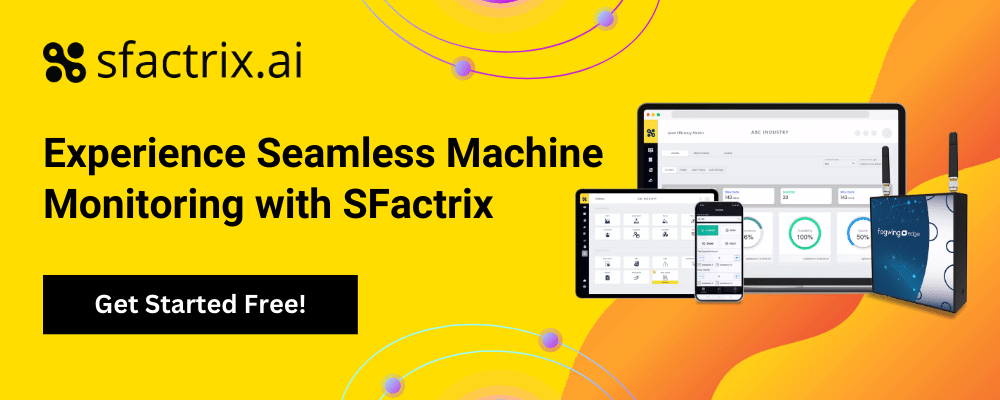
Conclusion:
To improve your lean operation, you must first understand the value of machine or equipment efficiency. Let’s so lets you set realistic expectations for your team and ensure everyone works towards a common goal. Additionally, the efficiency of machines can help you identify areas of improvement within your process and make necessary changes to improve your overall operation.
Finally, it is essential to remember that machine efficiency is an ongoing process. Regular maintenance and upgrades should be conducted to ensure you are getting the most out of your machines and the time your team spends working on them. Doing so can improve your lean operation and create a more efficient business.