Maintenance management has evolved with the Industry 4.0 revolution. Advancements in technology and data-driven approaches have streamlined asset management, making the choice between preventive and predictive maintenance crucial for businesses.
Striking the right balance between these two maintenance approaches enhances asset performance. This blog will discuss the benefits, how to select, and the key differences between preventive and predictive maintenance strategies.
What is Preventive Maintenance?
Preventive maintenance is an asset maintenance strategy employed to maintain the asset. It organizes regular maintenance activities to ensure the equipment functions correctly without unexpected breakdowns.
The maintenance team here does not wait for an asset to break down to perform reactive maintenance. The team schedules the maintenance activity of the assets based on usage, manufacturer’s requirements, and time.
Preventive and predictive maintenance both focus on minimizing equipment failures, like keeping your car or AC in top shape. Instead of waiting for a breakdown, you proactively inspect, clean, lubricate, and replace parts before issues arise.
What is Predictive Maintenance?
Predictive maintenance takes asset upkeep processes one step ahead of preventive maintenance. It utilizes AI and IoT technologies to monitor asset conditions and predict when an asset can fail.
Predictive maintenance and preventive maintenance aim to prevent unexpected failures, but they differ in approach. Predictive utilizes real-time data, machine learning, and IoT sensors to monitor asset health and foresee failures before they occur.
For example, a vibration sensor is connected to a machine to determine an unusual pattern. f vibration levels deviate from the normal range, the system predicts a possible bearing failure. The maintenance team will be alerted about the potential asset failure to conduct maintenance operations.
Difference Between Preventive and Predictive Maintenance
The difference between predictive and preventive maintenance is in its execution — preventive maintenance is time-based. In contrast, predictive maintenance is condition-based, which is why it is more efficient at avoiding unnecessary servicing.
The following table illustrates the differences between Preventive Maintenance and Predictive Maintenance in detail:
Feature | Preventive Maintenance | Predictive Maintenance |
Definition | Scheduled maintenance is performed at regular intervals to prevent asset failures. | Maintenance based on real-time data analysis to predict and prevent failures. |
Approach | Time-based or usage-based. | Condition-based and data-driven. |
Technology Used | Essential tools and scheduled inspections. | IoT sensors, AI, machine learning, and real-time monitoring. |
Maintenance Frequency | Performed at fixed intervals, regardless of the actual condition. | Performed only when required, based on real-time equipment conditions. |
Cost Efficiency | This may lead to unnecessary maintenance costs if scheduled too frequently. | Reduce unnecessary maintenance costs by accurately predicting failures. |
Downtime Reduction | It helps minimize downtime but may not always be efficient. | Significantly reduces unexpected downtime by addressing issues before they occur. |
Implementation Complexity | It is more straightforward to implement with essential planning. | Needs investments in advanced technology and skilled people. |
Industries Used | Manufacturing, healthcare, aviation, and facility management. | Industries with high-value assets like power plants, oil & gas, and smart factories. |
Example | Regular servicing of a vehicle every 6 months. | A machine sensor detects increased vibration and alerts for maintenance before failure. |
Both preventive and predictive maintenance play a crucial role in asset management. While preventive maintenance ensures routine servicing, predictive maintenance optimizes maintenance schedules using advanced analytics. The choice depends on industry needs, budget, and technological capabilities.
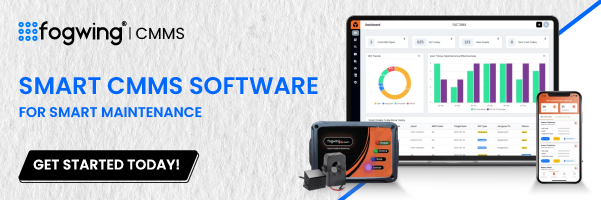
Pros and Cons of Preventive Maintenance Strategies
Preventive maintenance methods serve as proactive maintenance strategies in asset maintenance. While preventive maintenance has advantages, it also has a few challenges.
Pros | Cons |
Reduces Unexpected Downtime Regular maintenance scheduling minimizes sudden equipment failures, ensuring smooth operations. | Higher Maintenance Costs Assets may receive unnecessary servicing, leading to increased maintenance expenditures. |
Extends Asset Life Span Routine lubrication, servicing, and parts replacements improve equipment longevity. | Increased Labor & Resource Allocation Regular inspections require additional manpower, time, and resources. |
Easy to Adopt Unlike predictive maintenance, preventive maintenance relies on simple time or usage-based scheduling. | Scheduled Downtime Assets may be taken offline for maintenance, even when they are operating well, affecting productivity. |
Enhances Workplace Safety Regular maintenance reduces the risk of asset failures and workplace accidents. | Not Always Cost-Effective In some cases, predictive maintenance may offer a more efficient and cost-saving alternative. |
While preventive maintenance and predictive maintenance both aim to enhance asset performance, businesses must assess their needs carefully to determine the best approach. Fogwing CMMS can help streamline preventive maintenance strategies, optimize resource allocation, and reduce unnecessary costs.
Pros and Cons of Predictive Maintenance Strategies
Predictive maintenance is a data-driven maintenance strategy that helps businesses optimize asset performance by predicting failures before they occur. However, it comes with both benefits and challenges. The table below highlights the key pros and cons of predictive maintenance strategies:
Pros | Cons |
Reduces Maintenance Costs Maintenance is performed only when necessary, reducing unnecessary servicing expenses. | Expensive Investments Requires IoT sensors, data analytics tools, and software, making it costly for small businesses. |
Increases Operational Efficiency Real-time insights enable businesses to schedule maintenance without disrupting production. | Requires Skilled Workforce Industries need trained personnel to operate and interpret predictive maintenance technologies, increasing labor costs. |
Minimizes Unplanned Downtime Predictive insights help prevent sudden equipment failures, ensuring smooth operations and higher productivity. | Implementation Challenges Integrating predictive maintenance into existing systems requires advanced planning and technical expertise. |
Enhances Workplace Safety Early detection of potential issues reduces the risk of hazardous equipment malfunctions. | Not Suitable for All Equipment Some machines may lack measurable performance indicators, limiting predictive maintenance applications. |
While predictive maintenance and preventive maintenance both offer advantages, businesses must evaluate their operational needs and resources to determine the best approach.
Industries Best Suited for Preventive and Predictive Maintenance Approaches
Specific industries are well-suited for Preventive and Predictive maintenance strategies. When choosing these strategies, industries consider operational needs, asset criticality, and technological capabilities.
To determine the best asset maintenance strategy, companies tend to compare the benefits of Preventive vs Predictive maintenance. Some tend to follow preventive maintenance, whereas others adopt predictive maintenance. The company’s choice relies on individual operational requirements and objectives.
Manufacturing: Preventive and predictive maintenance is crucial in helping manufacturers minimize downtime and boost overall productivity. Preventive maintenance involves regular servicing of equipment to keep it running smoothly. It utilizes sensors to monitor equipment health and find potential failures before they happen.
Healthcare: Predictive and preventive maintenance are vital in healthcare to ensure the reliability of medical equipment. Preventive maintenance adheres to strict schedules for servicing MRI machines and ventilators. In contrast, predictive maintenance identifies potential failures in real time.
Automotive & Transportation: Preventive and predictive maintenance ensure that vehicles and transportation systems operate efficiently. Preventive maintenance involves regular servicing of engines and brakes. Whereas, predictive maintenance utilizes IoT sensors to help fleet managers identify you wear in-vehicle components.
Energy and Utilities: Energy and utilities rely on predictive and preventive maintenance to ensure an uninterrupted power supply and reliable infrastructure. Preventive maintenance involves scheduled transformer servicing, while predictive maintenance monitors grid performance to avert unexpected failures.
Oil and Gas: In the gas and oil sectors, predictive and preventive maintenance are essential in preventing costly shutdowns and ensuring safety. Preventive maintenance involves regular inspections, whereas predictive maintenance employs vibration analysis and real-time monitoring to identify potential leaks.
How can Fogwing CMMS empower a preventive maintenance strategy?
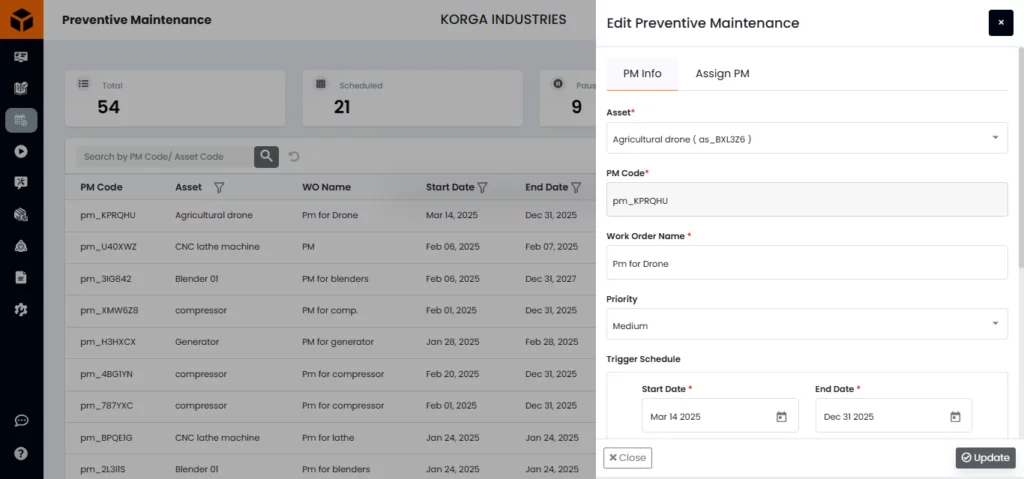
Fogwing CMMS enables industries to carry out a preventive maintenance strategy by automatically scheduling maintenance, monitoring work orders, managing parts inventory and maximizing asset performance. It helps businesses plan maintenance based on usage or time, optimizing asset reliability and minimizing unplanned breakdowns.
It offers reports and insights, enabling industries to track performance trends and optimize preventive maintenance approaches for improved efficiency and cost reduction. By leveraging automation and analytics, industries can shift from reactive maintenance to proactive asset management, ensuring long-term operational success.
How do you choose the proper Maintenance operations for your Industries?
Choosing between the preventive and predictive maintenance examples depends on various factors, such as budget, asset criticality, operational goals, and technological capabilities.
Here are the key factors to consider when deciding the best maintenance approach for your business:
1. Character of Assets and Equipment:
- If your industrial assets need regular upkeep, you can consider Preventive and Predictive maintenance options.
- If you have highly complex machinery, you can consider predictive maintenance because of its IoT sensors and real-time data analysis techniques.
2. Maintenance Budget and Expenses:
- Preventive maintenance requires a lower initial investment but might lead to unnecessary servicing expenses.
- AI and IoT technologies might be expensive to install for the first time, but they reduce maintenance costs in the long run.
3. Industry and Compliance Requirements:
- Sectors such as Healthcare and aviation apply Preventive maintenance because of their stringent regulatory demands, as it provides them with compliance.
- Industries such as manufacturing, oil and gas, and utilities usually rely on predictive maintenance to reduce downtime.
4. Downtime Tolerance and Production Impact
- If your business cannot afford unexpected downtime, predictive maintenance is a better choice, as it detects failures before they occur.
- If scheduled downtime is manageable, preventive maintenance may be cost-effective.
Conclusion
Choosing between preventive and predictive maintenance is crucial for optimizing asset performance and reducing operational disruptions. While preventive maintenance and predictive maintenance both aim to enhance equipment reliability, the key difference between preventive and predictive maintenance lies in their approach.
Industries need a robust maintenance management system to implement an efficient strategy and Fogwing CMMS offers the ideal solution. It helps optimize operations, minimize downtime, and reduce costs by blending preventive and predictive maintenance for long-term efficiency, compliance, and asset longevity
FAQs
1. What is the difference between predictive maintenance and preventive maintenance?
Preventive maintenance follows a scheduled routine to prevent failures, while predictive maintenance uses real-time data and analytics to detect potential issues before they occur.
Predictive maintenance reduces unnecessary servicing, whereas preventive maintenance ensures regular checkups to minimize unexpected breakdowns.
2. Is predictive maintenance a type of preventive maintenance and what are the main types of maintenance?
Yes, predictive maintenance is a type of preventive maintenance, but with a data-driven approach.
Main Types of Maintenance:
- Corrective Maintenance
- Preventive Maintenance
- Predictive Maintenance
- Condition-Based Maintenance
- Reliability-Centered Maintenance (RCM)
3. How do predictive maintenance and preventive maintenance work?
Predictive maintenance and preventive maintenance both aim to prevent equipment failures, but work differently. Preventive maintenance follows a fixed schedule for inspections and servicing, while predictive maintenance uses real-time data and AI to detect potential failures before they occur.
4. What are the biggest challenges in implementing predictive maintenance?
- Requires IoT sensors, AI, and data analytics, which can be costly.
- Needs skilled personnel to interpret predictive insights.
- Handling large volumes of sensor data efficiently.
- Ensuring compatibility with legacy equipment.
- Employees may resist shifting from traditional maintenance
- Requires high-quality data to avoid false alarms or missed failures.
5. How do you determine the appropriate balance between preventive and predictive maintenance?
Finding the right mix of preventive and predictive maintenance depends on various factors, including asset type, budget, and operational needs. Here’s how to achieve the best balance:
- Assess Asset Criticality
- Evaluate Cost vs. Benefit
- Analyze Failure Patterns
- Use Hybrid Approaches
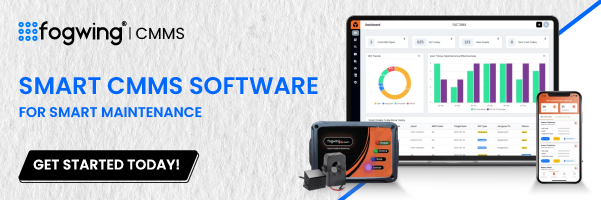