In recent years, technological advancements have revolutionized Visual Inspection. Today, machines can visualize elements better than humans. Rapid technological advances, innovations in artificial intelligence, robotics, and high-resolution imaging are transforming how we examine and assess various assets and equipment. This revolution opens the door to previously unimaginable levels of precision and enhances the accuracy and speed of inspections.
In this dynamic landscape, the integration of cutting-edge technology and inspection revolutionizes the manufacturing industries. This blog post will show how groundbreaking technologies transform visual inspection in manufacturing, from intricate manufacturing processes to complex quality control systems.
What is Visual Inspection?
Visual Inspection in Quality Control (QC) is a process in which products or materials are examined and assessed using visual means to ensure they meet specified quality standards. Instead of relying solely on automated systems or machinery, this type of inspection involves human visual inspection to identify defects, irregularities, or deviations from the desired quality criteria.
Visual inspection is particularly crucial in industries where the appearance, surface finish, or overall aesthetics of a product are critical factors. This method allows inspectors to detect issues such as scratches, discolorations, misalignments, or other visual defects that may impact the product’s quality and customer satisfaction. Advanced technologies, including computer vision and image recognition, may also be integrated to enhance the efficiency and accuracy of visual quality inspection processes.
It is a fundamental part of the production process as it enables organizations to detect any faults or defects that can impact the quality and functioning of end products. It ensures that the manufacturers meet their quality standards and deliver products that meet customer expectations.
Traditionally, Visual inspection in manufacturing industry involves manual checks by trained professionals. While this method effectively detected the surface-level defects, it was time-consuming and prone to human error. However, with rapid technological advancement, manufacturers can now incorporate various automated systems for more efficient and accurate visual inspections.
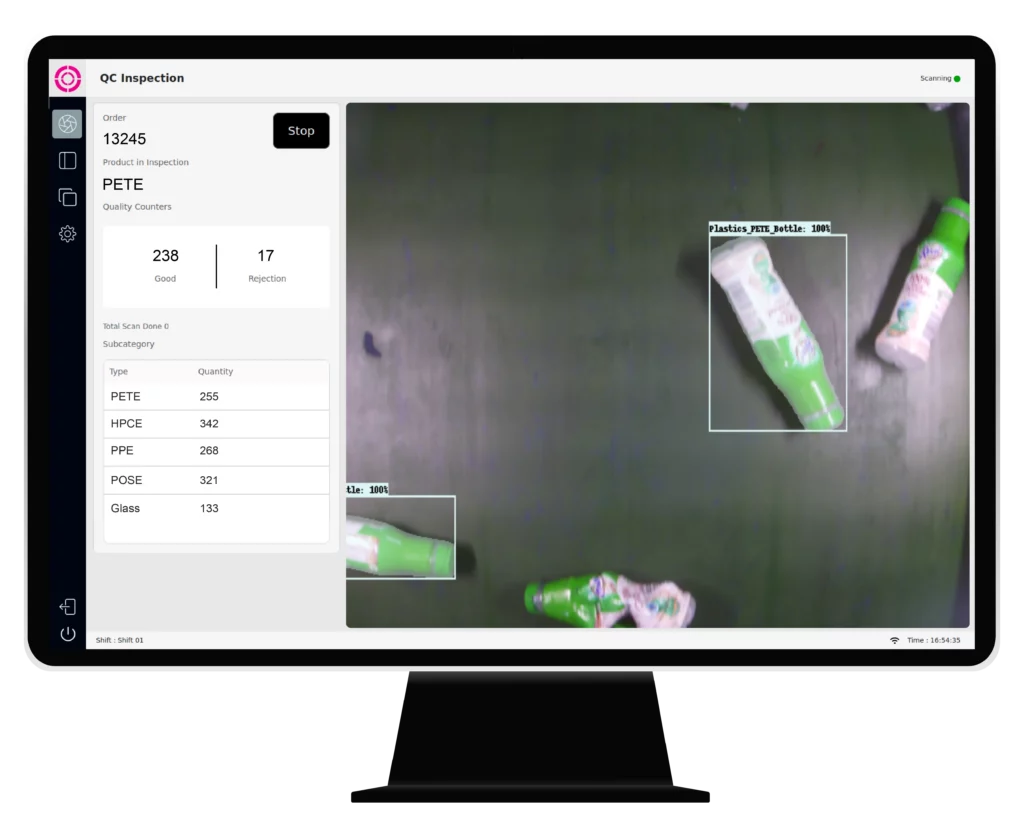
One of the most significant advancements is the machine vision systems. Machine Vision combines hardware and software technologies designed to capture images, process them, and extract the relevant information for decision-making purposes. This technology has significantly increased the speed and accuracy of visual inspection processes while reducing costs associated with a manual workforce.
One such technological development is Fogwing vision systems – which use cameras, sensors, and machine learning algorithms to mimic human vision detection capabilities.
The primary goal of this system is to create a sophisticated object prediction model that can autonomously and accurately identify objects. Fogwing vision can detect contaminations with precision and speed that surpasses manual inspection.
Overall, visual inspection in manufacturing is an essential aspect of modern industry that helps ensure the quality and safety of products. By implementing advanced technologies, manufacturers can streamline their inspection processes, reduce costs associated with defective products, and improve customer satisfaction. As technology advances, visual inspection will evolve, leading to more effective manufacturing processes in the manufacturing industry.
Which Industries Demand Visual Inspection?
Various industries have utilized visual inspection in manufacturing methods for decades. However, technological advancement has made these methods efficient, accurate, and reliable. A broader spectrum of sectors uses them to ensure quality control and enhance productivity.
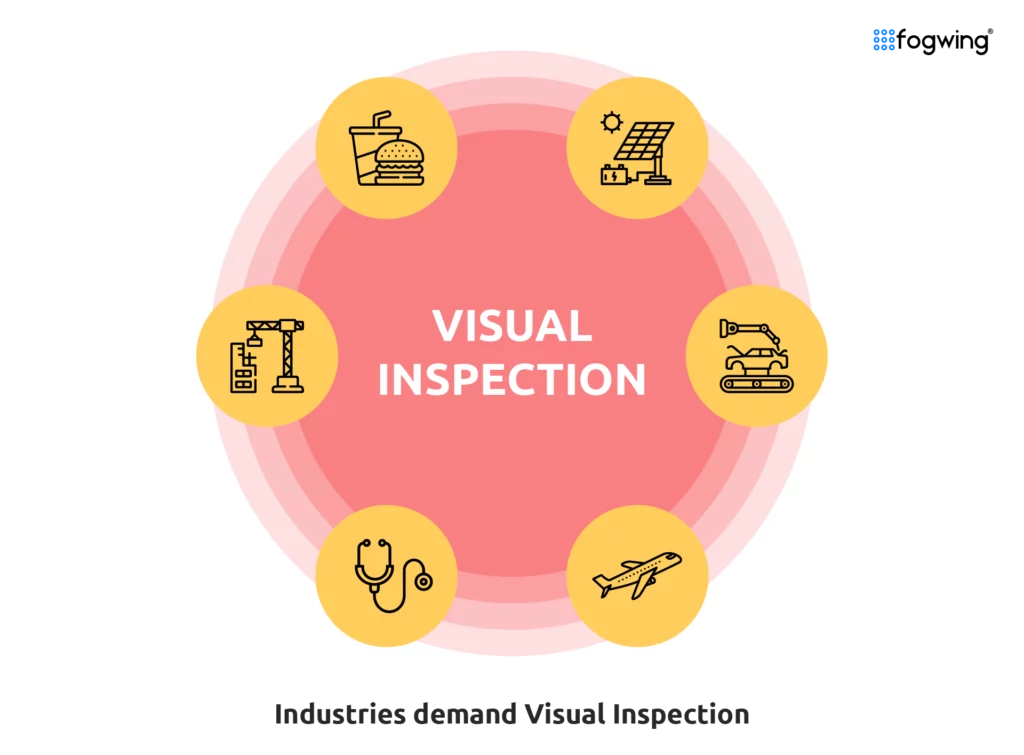
Manufacturing
The manufacturing sector is a primary industry that relies on visual inspection systems. With the production of various goods, such as automobiles, electronics, pharmaceuticals, and consumer goods, the manufacturing unit must ensure that its products meet the required quality requirements before reaching the consumers or market.
In manufacturing sectors, visual inspection techniques are used at different stages of production to check for defects or irregularities in shape, color, size, or surface finish.
Healthcare
Visual or quality inspection is paramount in healthcare, ensuring patient safety and effective treatment. To detect any flaws before use, it is essential to thoroughly examine various medical devices, such as syringes, vials, and implants.
Machine vision systems and endoscope cameras are examples of visual inspection systems that help identify potential issues with medical equipment that could put patients at risk.
Food Processing
Ensuring food safety and maintaining high hygiene standards is vital in the food processing sectors. From visually inspecting raw ingredients to finished products on an assembly line, these methods help detect foreign objects or any contaminations that could compromise food quality.
It mitigates the risk of development recalls, safeguards consumer health, and serves as a cornerstone for meeting the rigorous regulatory standards mandated by food associations. This unwavering commitment to quality underscores the industry’s dedication to providing safe and wholesome consumables.
Aerospace
In the aerospace industry, visual inspection is paramount for ensuring the integrity and reliability of aircraft components. Highly trained inspectors meticulously inspect critical parts like engines, airframes, and avionics systems to detect even minute imperfections that could compromise aircraft safety.
An automated visual inspection guarantees that each component meets strict quality standards before integration by identifying and rectifying defects during production. This rigorous process safeguards against potential failures in flight and upholds regulatory compliance. Visual inspection systems are pivotal in delivering the highest-quality aircraft, guaranteeing safe and reliable aircraft for commercial or military use.
Contruction
In construction, inspections are fundamental for ensuring structural integrity and compliance with building codes. Trained reviews assess various aspects of construction projects, including foundations, framing, electrical systems, and finishing work. They identify potential defects, deviations from plans, and safety hazards through scrutiny.
Visual inspection systems are crucial in quality control, ensuring that construction projects meet industry standards and regulatory requirements. Additionally, they contribute to structures’ overall safety and longevity, assuring both builders and occupants.
Energy
In the energy industry, visual inspections are essential for maintaining operational efficiency and ensuring safety. Skilled assessments examine critical components of energy facilities such as power plants, pipelines, and renewable energy installations.
They assess equipment for signs of wear, damage, or potential faults, helping to prevent costly breakdowns and ensuring uninterrupted energy production. It also plays a crucial role in compliance with regulatory standards, environmental protection, and workplace safety. By identifying and addressing issues early on. Visual inspection systems contribute to the reliability and sustainability of energy infrastructures, benefiting industry stakeholders and consumers.
Why do Industries Follow Visual Inspection Guidelines?
Visual inspection is crucial to quality control and assurance in various industries such as manufacturing, automotive, aerospace, and healthcare. It involves examining an object or surface using the human eye to detect defects, flaws, or imperfections that may affect its functionality or safety.
With technological advancements, inspection methods have significantly evolved, making it possible to detect even the tiniest of defects that may not be visible to the human eye.
However, with more sophisticated quality inspection tools and techniques, there often needs to be more clarity about the requirement for inspection.
This section will discuss some situations where there is a need for quality inspection despite technological advancement.
Quality Control in Manufacturing
One of the primary applications of visual inspection is in manufacturing processes. Manually inspecting each unit is impossible in the highly automated production line, where thousands of products are manufactured daily.
It is where advanced visual inspection systems scan products for any physical defects or deviations from desired specifications. These systems can identify even the tiniest imperfections by analyzing high-resolution images with image recognition algorithms powered by AI/ML technology.
Deterioration Detection in Infrastructure
Quality inspections also play a critical role in monitoring infrastructure assets like bridges, roadways, railway tracks, pipelines, etc. Automated visual inspection systems combined with advanced cameras, drones, and sensors make it possible to examine these structures regularly and accurately to identify signs of wear and take corrective measures before they become a hazard.
Product Packaging Verification
Packaging is a vital bastion, safeguarding product quality and guaranteeing consumer safety across various sectors. Employing visual inspection methods such as label verification and checking for defects ensures the authenticity of products before they embark on their journey to end-users. This meticulous process upholds quality standards and fortifies trust between producers and consumers.
Medical Device Inspection
Upholding impeccable quality in the production of medical devices is paramount to guarantee patient well-being. It plays a vital role in meticulously identifying imperfections that might compromise the functionality or safety of these critical instruments.
This stringent inspection process is conducted throughout manufacturing and before the devices are introduced to the market, assuring unwavering adherence to industry standards.
Automotive Industry
Visual inspection is a cornerstone in the automotive industry, safeguarding vehicle performance and safety. Whether dissecting car bodies for imperfections or pinpointing faulty components within engine and electronics, this meticulous process guarantees that each vehicle departing the factory floor surpasses rigorous quality benchmarks. It is essential to recognize even the slightest defects, ensuring a standard of excellence that drivers can rely on.
Hazard Detection in High-Risk Environments
Industries like oil and gas, chemical production, and mining involve operations in hazardous settings, demanding vigilant monitoring for potential dangers.
Visual inspection guidelines, employing drones equipped with thermal cameras or specialized sensors, prove indispensable in identifying leaks, monitoring gas emissions, and detecting hazardous conditions. This proactive approach is instrumental in ensuring the safety and well-being of workers operating in these critical industries.
What are the Steps in Visual Inspection?
Visual inspection is a multi-step process that involves preparation, visual assessment, magnification, automated systems, specialized tests, documentation, and re-inspection.
This process helps identify and prevent potential issues in products or equipment and ensures their safety and quality. Technological advancements have made inspection faster, more accurate, and more reliable.
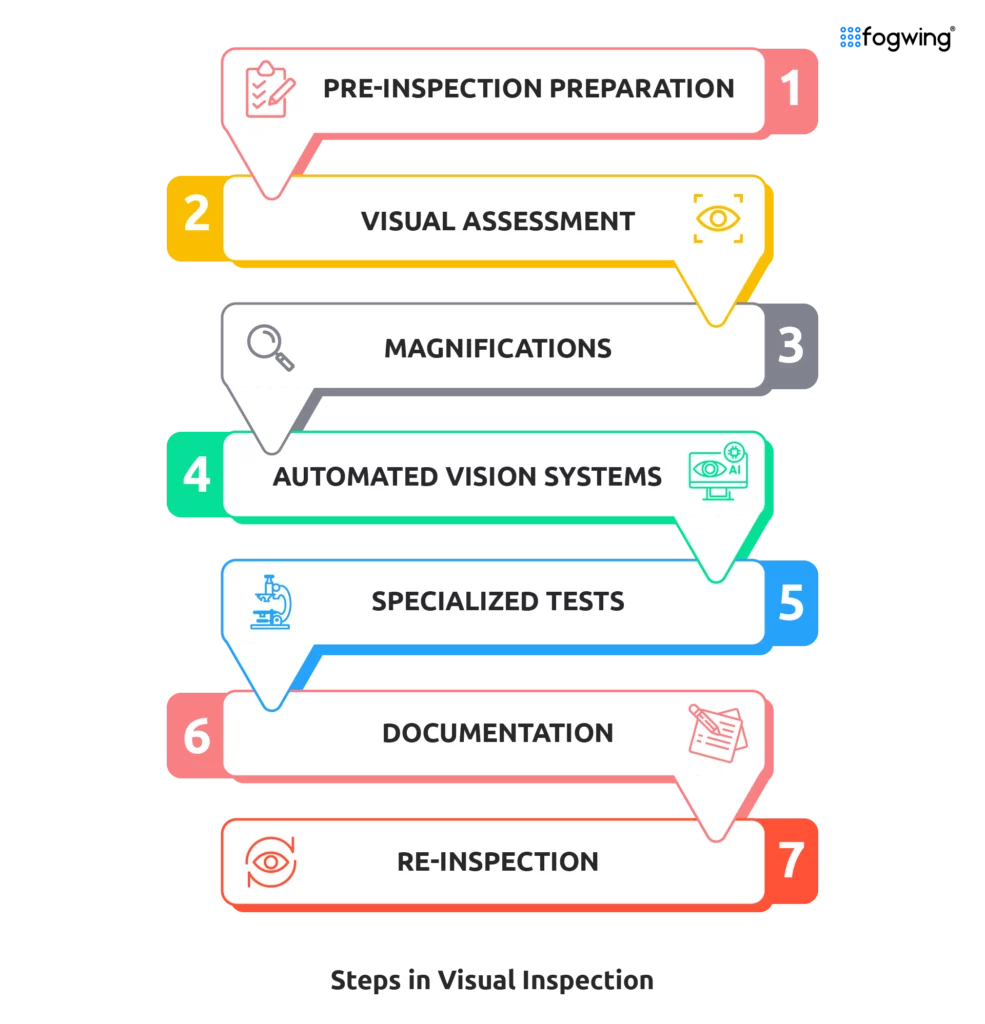
- Pre-Inspection Preparation: Preparing adequately before conducting an automated visual inspection is essential. Pre-inspection preparation involves identifying the purpose of the assessment, understanding the specifications and requirements of the object being inspected, gathering all the necessary tools and equipment (e.g., lighting sources, magnifying glasses), and ensuring a clean and suitable environment for the inspection.
- Visual Assessment: The first step in visual inspection is closely evaluating the object’s external appearance with the naked eye. This technique helps identify any visible imperfections such as scratches, dents, cracks, discoloration, or foreign particles on the surface. The visual assessment also includes checking whether the products meet specific size requirements or labeling standards.
- Magnifications: During initial visual assessment, defects may not be visible to the human eye. That’s where embellishment enhances visibility by providing a closer look at objects’ minor details. Traditional magnification tools include hand-held microscopes or loupes. However, technological advances have introduced digital microscopes with high-definition cameras for accurate and efficient inspections.
- Automated Vision Systems: With the introduction of automation in various industries, visual inspection processes have also become more automated. Computerized vision systems can utilize cameras and computer algorithms to capture and analyze images of objects at high speed. These systems can identify defects with accuracy and consistency, reducing human errors and increasing the efficiency of the inspection process.
- Specialized Tests: In certain instances, standard visual inspection guidelines alone may not detect flaws or imperfections in objects. In such cases, conduct specialized tests to ensure the proper functioning and safety of the inspected object. These tests may include X-rays, dye penetrant testing, or ultrasonic testing.
- Documentation: After conducting a visual inspection, it is essential to document all findings accurately. This step involves recording any defects or abnormalities found during the inspection and their locations on the inspected object. Detailed documentation aids in tracking defects over time and making informed decisions about repairs or replacements.
- Re-Inspection: Re-inspection is crucial to address all identified defects appropriately. This step involves checking for the necessary repairs or changes made after the initial inspection. It is essential to repeat the inspection process until organizations resolve all the faults and the object meets the required standards.
Challenges with Traditional Visual Inspection Approaches
Visual inspection is a crucial aspect of quality control in various industries, such as manufacturing, food processing, and pharmaceuticals. It involves examining products or components for defects or deviations from desired specifications. However, the existing visual inspection approach faces numerous challenges that hinder its effectiveness and efficiency.
One of the main challenges organizations face with current inspection methods is human error. Manual inspection heavily relies on the human eye to detect defects. However, it is well-known that human perception can be unreliable due to factors such as fatigue, distraction, and individual differences in vision capabilities. It can lead to consistency in detecting defects, resulting in a high rate of mistakes.
Another challenge traditional inspection methods face is their limited scope and capability. These approaches are often time-consuming, making it challenging to quickly inspect large quantities of products. Additionally, manual inspections may not be feasible for reviewing products with complex geometries or requiring detailed examination at a microscopic level.
Furthermore, traditional inspection techniques need more consistency and standardization. Different inspections may have varying expertise and experience, leading to discrepancies in identifying and classifying defects. It can impact product quality control and add to the cost of production due to rework or rejected products.
Moreover, manual vision inspections are prone to subjective interpretations based on personal biases or expectations. It can result in overlooking certain defects based on preconceived notions, challenging establishing a consistent and objective quality control process.
How Fogwing Vision is Helping in Visual Inspection?
Fogwing Vision Platform is an advanced solution poised to revolutionize the industry benchmark in visual inspection. This technology helps automated quality inspection through an advanced computer vision model, promising unparalleled accuracy by seamlessly melding IoT and ML technologies.
Fogwing vision empowers organizations to pinpoint contamination levels and defects with accurate precision. Comprising Fogwing Vison cloud, Fogwing Agent on edge, and Fogwing edge vision device, this innovation promises a proactive approach, ensuring swift interventions and constant enhancements.
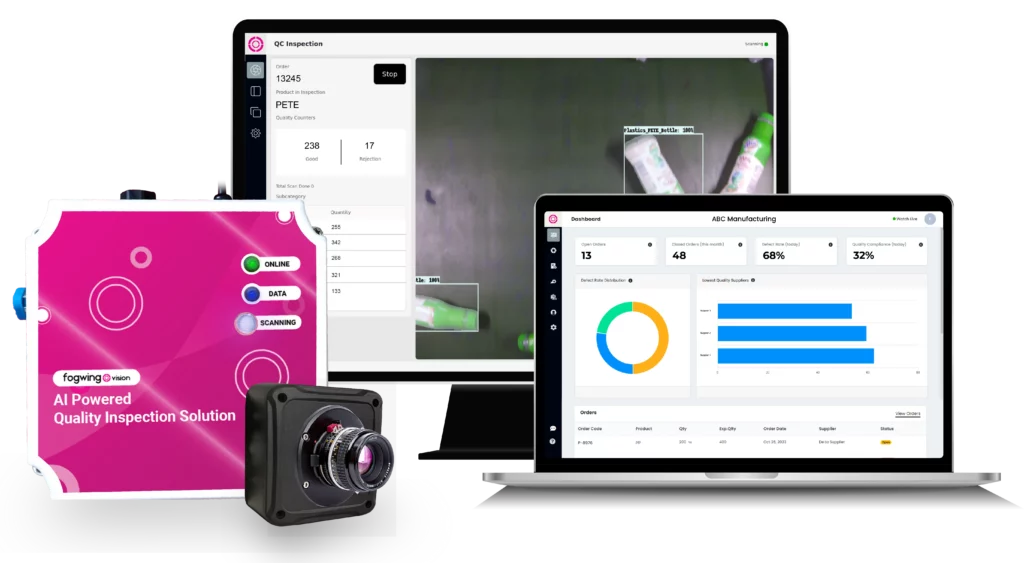
Stay tuned for the grand launch of Fogwing Vision, announcing a new era of ai visual inspection where precision meets innovation.
How to Overcome Visual Inspection Challenges
Industries are adapting automated visual inspection systems to overcome the visual inspection challenges. These systems use advanced technologies such as computer vision, machine learning (ML), and artificial intelligence (AI) visual inspection to enable quick and accurate inspections without intervention.
Inspection systems can be programmed with specific defect detection and classification criteria, resulting in consistent and standardized assessments. They are also capable of inspecting products at high speeds. They can handle large volumes of items in a short period. It significantly improves efficiency and reduces production costs.
Another benefit of visual inspection is its ability to inspect products with complex geometries or those requiring detailed examination at the microscopic level.
These systems can capture images from multiple angles, magnify images, or use different lighting techniques to enhance defect detection accuracy. Furthermore, unlike humans, automated vision systems do not suffer from fatigue or distractions, ensuring round-the-clock inspections without compromising accuracy.
It offers real-time data analysis, altering operators about potential issues before they result in significant defects or downtime in production. By implementing automated visual inspection systems, industries can enhance product quality control while reducing the costs associated with manual inspection. These systems can also improve customer satisfaction by ensuring products meet the desired specifications and minimizing the chances of defective products reaching consumers.
Conclusion
In conclusion, visual inspections have become integral to various industries because they enhance efficiency and accuracy and maintain high-quality standards. With continuous technological advancements and innovations in this field, these methods play an even more critical role in various industries.
From automated algorithms to high-resolution imaging technologies, these advancements are revolutionizing multiple sectors, such as manufacturing, healthcare, waste management, and food production.
As technology evolves and improves, we can expect even more innovative tools and techniques for visual inspection in manufacturing to enhance quality control processes across different sectors further. It is an exciting time for this field of study, and we look forward to seeing how it will continue to shape our world.