Do you want to avoid complicated manufacturing processes, endless documentation, and inefficient workflows? Look no further! Revolutionize your manufacturing operation with SFactrix production monitoring. In today’s fast-paced industrial world, visual factory methods have emerged as the ultimate solution to enhance productivity, eliminate waste, and streamline operations. But what exactly is a visual factory? How does it work its magic? Join us on this exciting journey as we dive deep into the realm of visual factories and uncover how they can revolutionize your business. Strap tight because this comprehensive introduction will give you insights and strategies that will forever change how you perceive efficiency!
What is Visual Factory?
A visual factory is a management system and methodology that utilizes visual cues, tools, and techniques to improve productivity, efficiency, and communication in manufacturing environments. It transforms complex information and processes into easily understandable visuals, such as color-coded indicators, charts, and displays, to aid decision-making, problem-solving, and process optimization. Additionally, a visual factory management system can help reduce errors by visually displaying how components must be assembled or operated. Making this information easier to understand can help reduce waste and improve productivity in the manufacturing process.
By implementing visual factory principles, companies create a more transparent and organized work environment where employees can quickly identify issues, monitor production status, and collaborate effectively. This approach fosters an environment of continuous improvement. It empowers workers at all levels to contribute to process enhancements and productivity. It is an integral part of Lean Manufacturing and significantly promotes workplace safety, reduces waste, and drives overall operational excellence.
Benefits of Implementing a Visual Factory
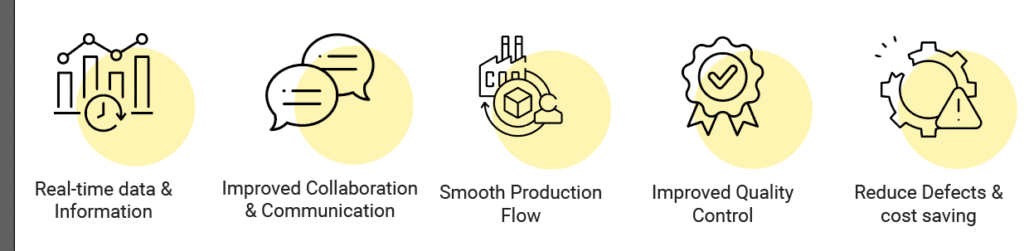
When it comes to manufacturing, a visual factory is a production system with transparent information regarding the production process. It means that all workers involved in the manufacturing process have access to real-time data and information about production status.
There are many benefits associated with implementing a visual factory system. One of the most significant benefits is improved communication and collaboration between workers. When everyone has access to the same information, it can reduce confusion and errors.
Another benefit of visual factories is that they can help to improve productivity. When workers have visibility into the entire manufacturing process, they can identify areas with bottlenecks or inefficiencies. By eliminating these bottlenecks, production can flow more smoothly and quickly.
In addition, visual factory can also help to improve quality control. When everyone can see what is happening at each production stage, it becomes easier to identify potential problems and take corrective action before defects occur.
Visual factory management also leads to cost savings. Visual factories help organizations save money on their overall manufacturing costs and maintain just-in-time manufacturing practices by improving collaboration and communication, increasing productivity, and reducing waste or defects.
Finally, visual factories provide an opportunity for continuous improvement and innovation. By presenting real-time visibility into the production process, workers can use the data to explore new ideas and identify potential improvements that could lead to better products.
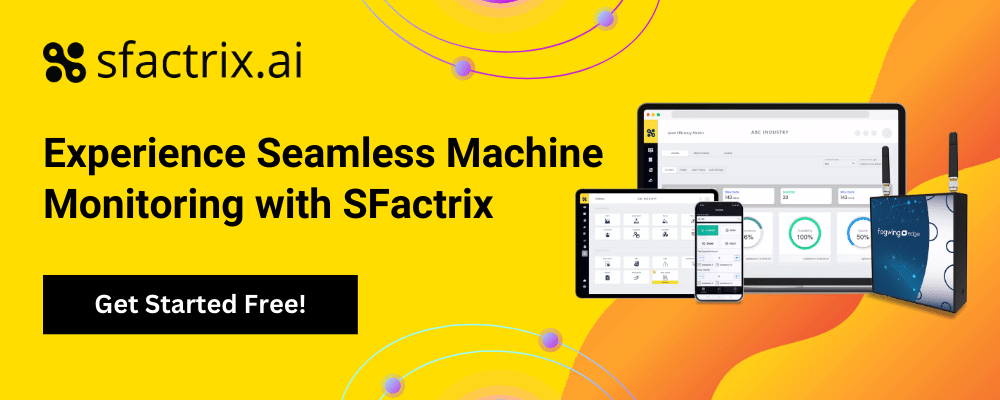
What is a visual factory in Six Sigma?
In Six Sigma, Visual Factory refers to the use of visual management techniques and tools to enhance process efficiency, quality control, and communication. It complements the principles of Six Sigma by providing a visual representation of process performance and making critical information easily accessible to all stakeholders.
Visual Factories in Six Sigma utilize visual cues like charts, graphs, and color-coded indicators to convey information about process metrics, defects, and performance trends. These visual representations enable quick identification of variations and deviations from the desired performance levels, facilitating timely decision-making and problem-solving.
The main goals of the visual factory in Six Sigma are to improve process visibility, identify root causes of defects, and engage employees in the continuous improvement process. Organizations can create a more transparent and data-driven environment by implementing visualization principles, driving better process control and optimization, leading to higher efficiency and quality outcomes. The visual factory is integral to Six Sigma and can help organizations achieve their manufacturing goals.
Visual Factory Software and Technology
Visual factory software and technology are essential in making communication and collaboration more effective in manufacturing. By automating the capture of data and making it available in real-time, th solutions help reduce production disruptions and downtime. Additionally, it enables informed decision-making about process improvements by giving users access to data visualization tools.
It can also monitor and control production processes, allowing users to view machine performance data and quickly diagnose issues. Visualization software solutions also enable users to simulate scenarios before implementing process changes by capturing data from multiple sources in a consolidated view. Finally, many visual factory solutions feature notifications that alert users when the current state of the production process is not meeting specified levels or targets.
Overall, visual factory software and technology can help improve the efficiency of manufacturing operation by providing users with the data needed to make informed decisions. Automating data capture, tracking process performance in real-time, and providing access to visualization tools can all help reduce waste and increase overall productivity.
Implementing Visual Factories: Best Practices
- Define Clear Goals: Establish specific objectives for the visual factory implementation.
- Engage Employees: Involve all employees in the planning and execution process.
- Practical Training: Provide comprehensive training on visual factory management principles and tools.
- Pilot Project: Start with a smaller pilot project to test and refine the practices.
- Visual Communication: Use transparent and standardized visual cues for easy understanding.
- Visual Management Boards: Display key metrics and progress on visual management boards.
- Regular Reviews: Continuously review progress and identify areas for improvement.
- Leadership Support: Obtain strong support from leadership to drive the initiative.
- Celebrate Successes: Recognize and celebrate achievements to motivate employees.
- Continuous Learning: Foster a culture of continuous improvement and learning.
- Sustainability: Integrate visual factory practices into the daily operations for long-term success.
Enhancing Efficiency with Visual Factory Tools
Enhancing efficiency with visual factory techniques or tools is key to optimizing manufacturing processes. These tools leverage visual cues and technology to streamline workflows, reduce waste, and improve overall productivity. Here are some frequently used visual factory tools for enhancing efficiency:
Kanban Systems
Kanban system facilitates visualizing tasks and inventory levels. They help regulate production flow, minimize overproduction, and ensure just-in-time delivery of materials, leading to efficient resource utilization.
Andon Systems
Andon systems use visual and audible signals to alert teams about issues or abnormalities on the production floor. Prompt notifications enable quick response and resolution of problems, minimizing downtime and enhancing productivity.
The 5S methodology
The 5S methodology involves sorting, setting order, shining, standardizing, and sustaining workplace cleanliness and organization. Maintaining a clutter-free and organized environment improves efficiency, reduces errors, and boosts employee morale.
Digital Dashboards
Interactive digital dashboards display real-time production data, KPIs, and performance metrics. Accessible information empowers decision-makers to make data-driven choices promptly, leading to better operational outcomes.
Production Flow Analysis
This visual factory method helps visualize production flow, and mapping workflows helps identify bottlenecks and areas for improvement. Production flow analysis optimizes processes, reduces cycle times, and enhances overall efficiency.
Work Instruction Software
Digital work instructions provide visual guidance for workers, making tasks easier to understand and execute accurately. This reduces the likelihood of errors and rework, saving time and cost.
Error-Proofing (Poka-Yoke)
Incorporating error-proofing mechanisms prevents mistakes and defects in the production process. Visual cues and devices ensure that correct procedures are followed, leading to higher product quality and efficiency.
Visual Signals and Markings
Clearly labeled tools, equipment, and workstations with optical signals facilitate easy identification and retrieval, reducing search time and improving workflow efficiency.
Overall Equipment Effectiveness Monitoring
Overall equipment effectiveness monitoring (OEE) tracks the performance of individual machines or lines against predetermined standards. The information can be displayed visually to identify and address issues quickly.
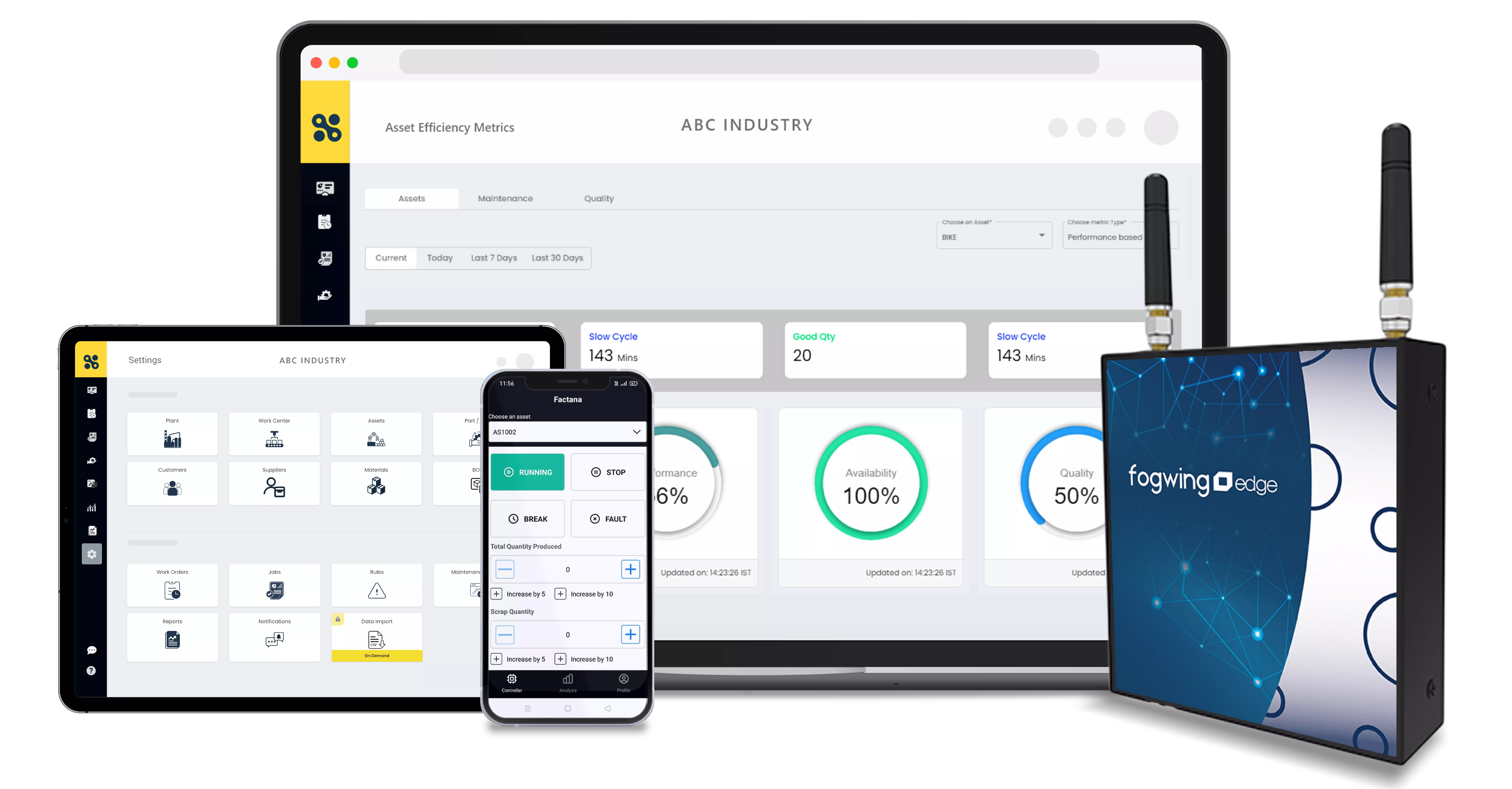
Visual Factory Management with SFactrix
SFactrix production monitoring is an all-in-one solution for all your visual factory needs. SFactrix, integrated with IoT, an inbuilt manufacturing intelligence module, provides a comprehensive suite of features to enhance your operations.
SFactrix production monitoring system collects real-time data from sensors, machines, equipment, and other relevant sources. The collected data is aggregated, analyzed, and displayed on the dashboard providing the complete visualization of factory operation. The dashboard visually represents the production key performance indicators (KPIs) and other relevant metrics. The operators, supervisors, and plant managers can access these dashboards to monitor production in real-time.
SFactrix production monitoring system dashboard displays performance metrics such as cycle time, downtime, quality, yield rate, defect rate, machine status, and overall equipment effectiveness (OEE). These metrics provide direct insights into the efficiency and effectiveness of the production process.
Businesses gain instant visibility into production efficiency and quality control by capturing real-time quantity and rejection count data. It helps Identify potential issues promptly and allows the production team to take immediate corrective actions and optimize their operations.
This visual factory tool is designed to be user-friendly, allowing operators and managers to grasp the state of production and make informed decisions quickly. Businesses can continuously improve processes, optimize resource allocation, reduce downtime, and enhance overall productivity by clearly and visually representing production operations.
To know more about how to improve OEE in your production operations, read this blog, 5 Ways To Improve OEE In Manufacturing Operations | Fogwing.io
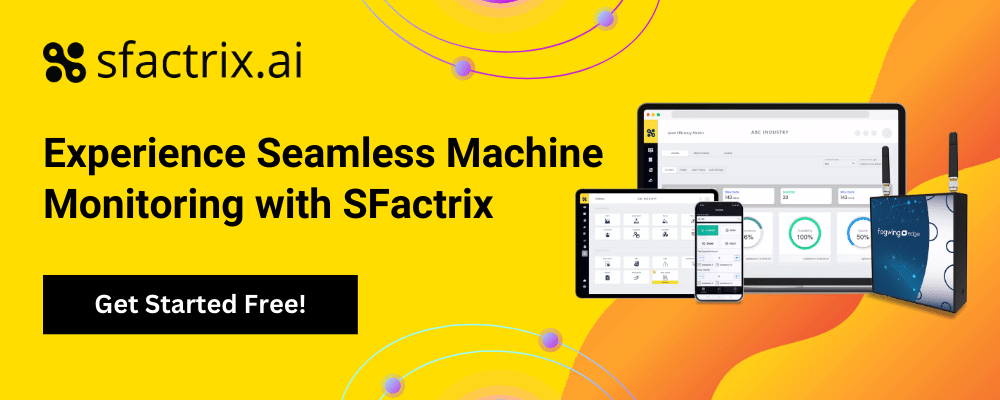
Conclusion
In conclusion, visual factory is a powerful management system that revolutionizes manufacturing. By leveraging visual cues, technology, and continuous improvement, it enhances productivity, reduces waste, and empowers the workforce. Despite challenges, engaging employees, securing leadership support, and using practical tools are critical to successful implementation. Embracing visual factories fosters a culture of transparency and responsiveness, driving manufacturing processes toward efficiency, profitability, and long-term success.