- Technical Guide
Machine Condition Monitoring Simplified
What is Machine Condition Monitoring?
Machines are tools that are created by humans to simplify the harder and complex works. Over the human evolution, humans started created tools from stone age period such as hammers to today’s advanced robotics system. In the industrial business, machines are key components of the business to facilitate operations fasters. Machines are deployed to execute the actions faster and efficiency. However, any kind of machines could break at some point in lifetime due to various environment conditions and usage basis.
Even though the purpose of tools are to simplify the actions; it requires continuous machine condition monitoring process to ensure that equipment itself operates efficiently as per terms. Machine conditions monitoring is the process to measure various operating conditions from the machines to understand the health of the components that are involved in machine functions.
Traditionally, specialized industry operators are allocated to put time and efforts to physical reach the machines for visually checking the operating conditions. In this approach, the operator should reach the machine to visually check the conditions which create risk for worker safety as well. This kind of manual visual checks are error prone due to oversights in naked eye visual checking. The success rate of such visual checks to prevent machine failure are estimated around 55% success only.
What is Remote Monitoring?
With advancement of wireless communication and Internet of Things (IoT) facilitates to measure the equipment parameters remotely using advanced sensors and connected devices. The retrofit sensors are equipped to read the data up to 99% accuracy which are connected to wireless devices to send the data to common data aggregators for analysis. This solution helps to connect with any machine in remote locations and read the parameters without physically sending operators to the remote location. This approach produces higher accuracy in preventive maintenance planning resulted in lower cost of operations.
How to monitor machines remotely?
Traditionally machine performance data is captured on demand basis, analyzed periodically to understand the conditions because data collection required enormous manual efforts in physical checking. By contrast, remove monitoring helps to gain access to the data from anywhere at any time on real time basis to instantly aware of the situation and also to persist the historic data of the machine performance and health conditions.
The effective Remote monitoring and machine condition analysis system required five primary components.
1. Retrofit Sensors
2. Wireless Connectivity Management (IoT)
3. Data Storage
4. Data Processing Engine
5. Visualization
By connecting the retrofit sensors into the existing machines at various checkpoints to read the sensible information from the machines. For example, reading the performance of the water pumping motor required to measure the energy consumption, speed of the rotor and vibration or noise generated by the motors. These sensor data should be stream to the centralized data storage environment (preferably cloud storage) for processing and persistency.
The connectivity between the sensor and remote data storage environment required cellular or LPWAN (Low Power WAN) network to connect IoT devices to internet. The device connectivity and communication management required centralized device management solution such as Industrial IoT. Industrial IoT platform are design to deploy, connect and manage the sensor connectivity through wireless devices through centralized web portal.
Once the data are consolidated in the data storage either as structured or unstructured, these data should be processed to combining the various parameters of data received from the sensors. The data transformation and enrichment processes are required to compare the various data checkpoints to arrive the meaningful insights of the equipment performance and utilization. The entire process is considered as data engineering and analytical procedure to arrive the metrics of information about overall equipment performance.
At the end, machine operators and industrial managers required visualization tool to practically see the data insights generated by the data processing engine. These visualization and data insights graphs helps to predict the equipment conditions and failure even before it occurs.
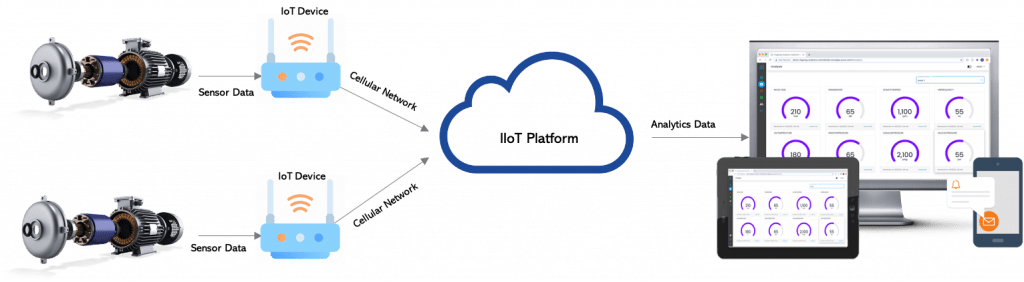
Role of Industrial IoT in Machine Condition Monitoring:
The Industrial IoT is kind of centralized middleware solution to manage the communication and machine health conditions between industrial machine and cloud data storage. The industrial IoT platform provides set of device management features from declaration of edge, connectivity, security, centralized hub for data aggregation and processing together. The centralized IIoT Management console provided by Fogwing IIoT platform is the one of such IoT Platform environment to manage the entire machine condition monitoring eco system. To explore further about IIoT here.
Conclusion:
The current economic situation across the world, every industry is exploring the possibilities to reduce the operating cost by deploying automated solutions. Physical visit and visual check are the most expensive operating procedure which should be replaced by taking advantage in technologies such as IoT and Analytics.