In today’s manufacturing industry, efficiency is paramount. With growing competition, optimizing production processes is more critical than ever before. One crucial element in achieving that optimization is takt time. In this article, we will explore its significance, calculation, implementation, and benefits in production.
What is Takt Time?
Takt time is a concept used in lean manufacturing that refers to the rate of production to match customer demand. Simply put, it is the duration to have one unit of product or service, including any necessary setup or downtime.
Definition and Origin of Takt Time
The word takt time comes from the German word ‘takt,’ which means ‘pulse.’ Toyota introduced it as part of the Toyota Production System to improve productivity and efficiency. It is the heartbeat of a production line, helping to synchronize processes and reduce waste.
Regarding manufacturing, takt time is an essential tool that helps companies optimize their production processes. It is calculated as the available production time divided by the customer demand. This calculation enables companies to determine the required pace of production to meet customer demand while minimizing waste and maximizing efficiency.
For example, let’s say that a company has eight hours of production time available each day, and the customer demand is 480 units per day. The takt time for this scenario would be one minute per unit (480 units/480 minutes = 1 minute per unit). The company must produce one unit every minute to meet customer demand.
Importance of Takt Time in Lean Manufacturing
Takt time is a fundamental tool in lean manufacturing and is highly significant. It helps companies to meet customer demand, increase production efficiency, reduce waste, and improve overall quality. By identifying the required pace of production based on customer needs, companies can develop a synchronized and lean workflow.
One of the benefits of using takt time is that it helps to identify bottlenecks in the production process. When an operation takes longer than the takt time, it can cause delays and reduce efficiency. By identifying these bottlenecks, companies can take steps to eliminate them and improve their production process.
Another benefit of takt time is that it helps to reduce inventory waste. By producing products at the required pace, companies can avoid overproduction, which can lead to excess inventory and waste. This can reduce costs and improve profitability.
In conclusion, it is a critical tool in lean manufacturing that helps companies to optimize their production processes, reduce waste, and improve overall efficiency. By calculating the required pace of production based on customer demand, companies can develop a synchronized and lean workflow that maximizes efficiency and profitability.
Calculating Takt Time
Calculating takt time is a critical component in optimizing production processes. It refers to manufacturing a particular offering to fulfill consumer expectations. It is determined by dividing the time allocated for production by the customers’ requirements. Understanding the components of takt time calculation is crucial to achieving maximum efficiency in production.
Key Components for Takt Time Calculation
- The total available production time in a shift, day, or week
- The total number of products or services customers require in that period.
Takt Time Formula and Examples
The formula is:
Takt Time = Available Production Time ÷ Customer Demand
For example, suppose a company has eight hours of available production time in a day and customer demand for 800 units per day.
Takt Time = 8 hours ÷ 800 units
Therefore, the takt time, in this case, would be one unit every thirty-six seconds.
It is important to note that the takt time differs from cycle time. Cycle time refers to the duration it takes to complete one production unit. In contrast, takt time is the production rate of units that meets the customer demand.
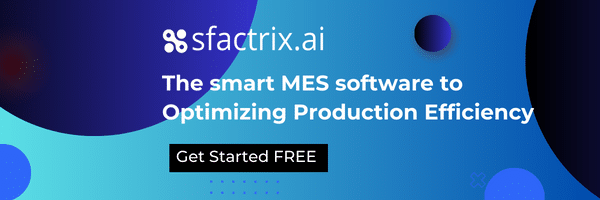
Common Mistakes in Takt Time Calculation
While the formula for takt time is straightforward, it is essential to avoid common mistakes when calculating it. Errors in calculating it can result in a mismatch between production capacity and customer demand, leading to waste and inefficiency. Some common mistakes to avoid include the following:
- Using the wrong time for available production.
- Using the faulty unit of measurement for customer demand
- Not taking breaks or downtime into account when calculating available production time
- Not factoring in variability in customer demand
By avoiding these common mistakes, companies can accurately calculate takt time and optimize their production processes to meet customer demand efficiently.
Implementing Takt Time in Production
Implementing takt time is crucial to achieving lean manufacturing and optimizing production processes. Takt time is required to produce one product unit to match customer demand. It helps manufacturers to synchronize production processes, eliminate waste, and maximize productivity.
Implementing takt time requires understanding the workflow and effectively balancing workload and resources. Here’s what you need to do:
Aligning Production Processes with Takt Time
Aligning production processes with takt time requires a synchronized workflow that matches customer demand. Breaking down the production process into smaller steps and synchronizing them helps to identify bottlenecks and optimize flow. It involves analyzing the production process to identify areas for improvement to eliminate waste and improve efficiency. A pull system can also help align production processes with customer demand.
For instance, if a customer orders 100 units of a product in a week, the time for producing one unit would be 8 hours (assuming a 5-day workweek). Therefore, it is essential to synchronize the production process to create one unit every 8 hours to match customer demand.
Balancing Workload and Resources
Another essential aspect of implementing takt time is balancing workload and resources. Ensuring that production processes align with customer demands means balancing workload and resources effectively. Utilizing a resource management system can help achieve this equilibrium. It involves analyzing the production process to identify areas that require additional resources and allocating them accordingly. It also includes optimizing production processes to ensure workers evenly distribute the workload.
Effective resource management can eliminate waste, reduce lead times, and improve productivity. It involves monitoring production processes constantly to identify areas that require additional resources or adjustments to workload.
Adjusting Takt Time for Variability and Downtime
Adjustments to takt time may be necessary to account for variability in production or other factors that impact production efficiency. For instance, periods of downtime or equipment malfunctions may require modifications to time. Therefore, it is crucial to monitor production constantly and adjust as needed.
Adjusting takt time requires a thorough understanding of the production process and the factors that impact production efficiency. It involves analyzing production data to identify areas requiring adjustments and modifying accordingly.
In conclusion, implementing takt time is crucial to achieving lean manufacturing and optimizing production processes. It requires understanding the workflow, balancing workload and resources effectively, and adjusting takt time for variability and downtime. By implementing takt time, manufacturers can synchronize production processes, eliminate waste, and maximize productivity.
Benefits of Takt Time Optimization
Optimizing takt time yields several advantages to manufacturers, including:
Improved Production Efficiency
Optimizing takt time improves production efficiency by reducing waste, increasing flow, and synchronizing production processes with customer demand. This optimization results in more efficient use of resources, reducing production time and improving overall profitability.
For example, suppose a manufacturing company produces 100 units of a product daily, and the takt time is 10 minutes per unit. Optimizing the takt time allows the company to reduce the time to produce each unit to 8 minutes. The takt time optimization would result in a total production time of 800 instead of 1000 minutes, allowing the company to make more units daily.
Optimizing takt time also helps identify and eliminate non-value-added activities in the production process. Doing so makes the production process more streamlined and efficient, reducing production time and cost.
Reduced Waste and Inventory
By synchronizing production processes to match customer demand, it reduces the need for excess inventory, thus reducing the waste produced by overproduction.
Overproduction can lead to a build-up of inventory, which ties up resources and increases the risk of obsolescence. Optimizing takt time makes the production process more aligned with customer demand, reducing the need for excess inventory and minimizing the risk of waste.
Additionally, takt time optimization can help identify and reduce other forms of waste, such as defects, overprocessing, waiting, and unnecessary motion.
Enhanced Customer Satisfaction
Aligning production processes with customer demand means consistently delivering products and services on time. This enhanced customer satisfaction is vital to retaining and attracting customers.
By optimizing takt time, manufacturers can ensure that they produce the correct number of products at the right time while reducing the risk of stockouts and delays. This optimization, in turn, leads to improved customer satisfaction and loyalty.
Moreover, takt time optimization can help identify opportunities for product and service improvements, leading to higher customer satisfaction levels.
In conclusion, optimizing takt-time has several benefits for manufacturers, including improved production efficiency, reduced waste and inventory, and enhanced customer satisfaction. By implementing it optimization, manufacturers can streamline their production processes, reduce costs, and improve profitability.
Conclusion
Takt time is an essential concept in production optimization. Understanding its significance and implementation is vital to increasing production efficiency, reducing waste, and enhancing customer satisfaction. By utilizing time in production, manufacturers can achieve leaner operations and gain a competitive edge.
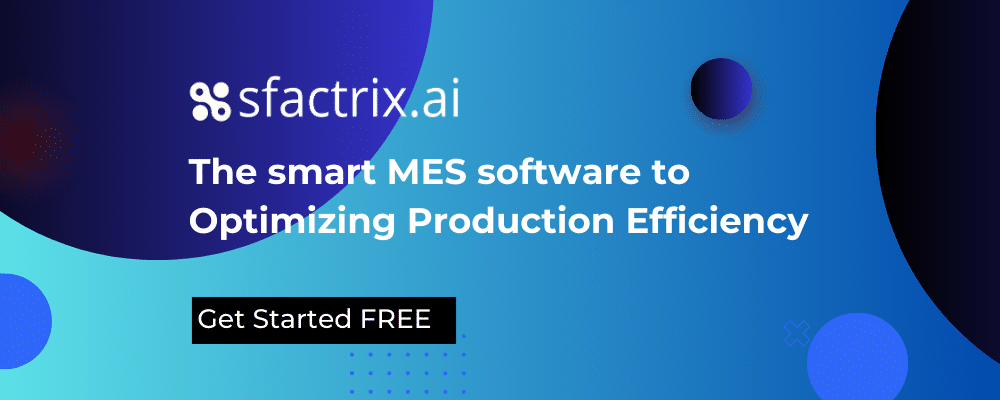